The realm of manufacturing has undergone revolutionary changes with the advent of 3D printing technologies. Among these innovations, Multi Jet Fusion (MJF) stands out as a groundbreaking method, offering unprecedented capabilities for custom part manufacturing. Developed by HP, MJF provides a unique approach that blends speed, precision, and flexibility, making it a highly sought-after technology in various industries. This article delves into the intricacies of MJF, its advantages, and its transformative impact on custom part manufacturing.
Understanding Multi Jet Fusion (MJF)
Multi Jet Fusion (MJF) is an additive manufacturing process that builds parts layer by layer using a fine-grained polymer powder. Unlike other 3D printing technologies such as Stereolithography (SLA) or Fused Deposition Modeling (FDM), MJF does not rely on a laser or a filament. Instead, it employs a combination of a fusing agent and a detailing agent, which are selectively deposited by an array of inkjet nozzles onto a powder bed. These agents are then exposed to infrared light, causing the fusing agent to absorb heat and melt the powder, while the detailing agent helps define edges and smooth surfaces.
This process allows MJF to produce parts with high accuracy and fine detail, along with excellent mechanical properties. The technology is particularly well-suited for creating complex geometries and intricate designs that would be challenging or impossible to achieve with traditional manufacturing methods.
1. Speed and Efficiency
One of the most significant advantages of Multi Jet Fusion (MJF) is its exceptional speed. MJF achieves this by printing multiple parts simultaneously within a single build cycle and utilizing rapid heating and cooling processes facilitated by fusing agents and infrared light. This efficiency leads to significantly shorter lead times, making MJF an ideal choice for rapid prototyping and small-to-medium production runs.
2. Superior Part Quality
MJF produces parts with outstanding surface quality and fine details. The precision of the inkjet nozzles, combined with the fine-grained powder, results in smooth surfaces and sharp edges. Additionally, the detailing agent ensures that the parts have well-defined features, reducing the need for extensive post-processing. This high level of detail is crucial for applications requiring tight tolerances and complex geometries.
3. Excellent Mechanical Properties
The parts produced by MJF exhibit excellent mechanical properties, including high strength and durability. The homogeneous nature of the fused material ensures consistent performance across the entire part, making MJF parts suitable for functional applications. These mechanical properties can be further enhanced by using advanced materials specifically designed for MJF, such as high-performance polymers and composites.
4. Material Versatility
MJF supports a wide range of materials, allowing manufacturers to choose the best material for their specific application. Common materials include Nylon 12, Nylon 11, and TPU (thermoplastic polyurethane), each offering unique characteristics such as flexibility, chemical resistance, and impact strength. This material versatility enables MJF to cater to various industries, including automotive, aerospace, medical, and consumer goods.
5. Design Flexibility
The layer-by-layer nature of MJF allows for the creation of highly complex and intricate designs that would be impossible or cost-prohibitive with traditional manufacturing methods. Designers can take full advantage of this capability to create lightweight structures, integrated assemblies, and custom features tailored to specific needs. This design freedom opens up new possibilities for innovation and optimization in product development.
Applications of MJF in Custom Part Manufacturing
1. Rapid Prototyping
MJF is an excellent choice for rapid prototyping due to its speed, precision, and ability to produce high-quality parts. Designers and engineers can quickly iterate on their designs, test functionality, and make necessary adjustments before moving to full-scale production. This iterative process significantly reduces development time and costs.
2. End-Use Parts
Beyond prototyping, MJF is also suitable for producing end-use parts, particularly for low-to-medium volume production runs. The technology’s ability to produce durable, high-performance parts makes it an attractive option for industries requiring custom components, such as aerospace and medical devices. For example, MJF can be used to manufacture lightweight, complex brackets for aircraft or patient-specific surgical guides for medical procedures.
3. Custom Tooling and Fixtures
Manufacturers can leverage MJF to create custom tooling, jigs, and fixtures tailored to their specific production needs. These custom tools can improve manufacturing efficiency, reduce setup times, and enhance product quality. The ability to quickly produce and iterate on these tools enables manufacturers to respond rapidly to changing production requirements.
4. Consumer Products
The consumer goods industry can benefit from MJF’s ability to produce highly customized products with intricate designs. From personalized accessories to custom-fit wearables, MJF allows manufacturers to offer unique products tailored to individual preferences. This customization capability can drive customer engagement and create new market opportunities.
Challenges and Considerations
While MJF offers numerous advantages, there are also challenges and considerations to keep in mind. The initial investment in MJF equipment can be significant, and the cost of materials may be higher compared to traditional manufacturing methods. Additionally, the technology requires a certain level of expertise to optimize the printing process and achieve the best results.
Post-processing can also be a consideration, as some parts may require additional finishing steps such as sanding, dyeing, or coating to meet specific aesthetic or functional requirements. However, these challenges are often outweighed by the benefits of speed, quality, and design flexibility that MJF provides.
Future Prospects
The future of Multi Jet Fusion looks promising as the technology continues to evolve and mature. Ongoing advancements in material science and process optimization are expected to further enhance the capabilities of Multi Jet Fusion. As the demand for customized products and rapid production grows, Dainsta is playing a crucial role in shaping the future of manufacturing. Its ability to quickly and efficiently produce high-quality, custom parts aligns seamlessly with the industry trends of personalization and on-demand manufacturing.
Conclusion
Multi Jet Fusion (MJF) represents a significant leap forward in the field of custom part manufacturing. Its combination of speed, precision, and versatility makes it an ideal choice for a wide range of applications, from rapid prototyping to end-use parts. As industries continue to embrace the benefits of 3D printing, MJF is poised to become a cornerstone technology, enabling new levels of innovation and customization in manufacturing. By harnessing the power of MJF, manufacturers can unlock new possibilities and stay ahead in an increasingly competitive landscape.
Read more from techbullion
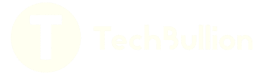