Introduction to Gummy Manufacturing
Gummy manufacturing is a meticulously structured process that involves the convergence of food science and modern production techniques to create a vast assortment of gummy candies that appeal to diverse consumer preferences. Central to this process are principles of consistency, quality control, and safety, which ensure that the final products are not only flavorful but also comply with stringent health standards. Manufacturers deploy advanced machinery, formulations, and methodologies to produce gummies in various shapes, sizes, and flavors, catering to the evolving tastes and dietary requirements of consumers globally. This guide aims to dissect the manufacturing stages, explore the equipment used, and discuss best practices, thereby providing a comprehensive overview of the gummy production landscape.
What is a Gummy Machine?
Understanding the Functionality of Gummy Machines
A gummy machine is a specialized piece of confectionery equipment designed to automate the gummy production process, ensuring uniformity and efficiency. Principle components of a gummy machine typically encompass a mixing unit, a molding system, and a cooling and setting conveyor. The mixing unit is responsible for combining various ingredients such as gelatin, sweeteners, flavorings, and colorants under precise conditions. Modern gummy machines use advanced sensors and control systems to maintain critical parameters like temperature and mix viscosity, ensuring a consistent product batch after batch.
The molding system, often employing starchless or starch-based technologies, is where the liquid mixture is deposited into molds to give gummies their distinctive shapes. Starchless molding systems are praised for their hygiene and speed, using silicone or plastic molds that can be rapidly filled and cooled. Data from industry suppliers reveal that these advanced systems can produce upwards of 30,000 gummies per hour with remarkable replicability. Once cast, the gummies are transferred via a conveyor through a cooling tunnel, solidifying the mixture. The integral role of this equipment in gummy candy manufacturing cannot be overstated; it is the cornerstone of mass production that meets both industry and regulatory standards for quality and safety.
Types of Gummy Machines Available in the Market
The market offers a spectrum of gummy machines designed to cater to various scales of production and specific product types. Broadly categorized, these machines can be classified into small-scale batch cookers for boutique confectioneries and fully automated, continuous systems for large-scale manufacturers. Batch cookers are typically favored by artisans focusing on customized gummy productions, whereas continuous systems are the backbone of high-volume, standardized gummy candy production.
Choosing the Right Gummy Machine for Your Production Line
Selecting an appropriate gummy making machine for a production line necessitates an analysis of production volume, desired product characteristics, space considerations, and budget constraints. Small to medium-sized enterprises might prioritize versatility and ease of use, while large manufacturers generally seek high-speed, dedicated machines that can integrate into existing automated lines.
Key Features to Look for in a Gummy Machine
When procuring a gummy machine, critical features to evaluate include the precision of depositing systems, speed of production, quality of temperature regulation, and compatibility with various gummy formulations. Innovations such as servo-driven depositing and remote monitoring capabilities are also garnering attention for their role in enhancing product consistency and enabling proactive maintenance.
Maintaining and Cleaning Your Gummy Machine
Proper maintenance and cleaning are crucial to prolong the life of a gummy machine and ensure compliance with hygiene standards. It entails regular checks on gaskets and seals, calibration of sensors and control systems, as well as adherence to a cleaning regimen that accommodates the specific design of the machine, such as detachable components and food-grade lubricants that prevent sugar crystallization and buildup.
How to Choose the Best Gummy Machine for Your Needs
Assessing Your Production Requirements
When assessing your production requirements, it is imperative to quantify your expected throughput and evaluate the scope for scalability. Analyze the demands of your product portfolio, as varied gummy shapes and formulations may influence the specifications of the machine you require. Consistency in output volume and quality must align with your business objectives to justify the investment.
Considerations for Selecting the Right Gummy Making Machine
Selecting the right gummy making machine encompasses a comprehensive evaluation of its operation parameters. The machine should be congruent with your facility’s current technology infrastructure and should exhibit compatibility with ancillary equipment. Prioritize machines that offer modular adaptations to keep pace with changing market trends and product diversification.
Ensuring Quality Control in Gummy Production
Quality control in gummy production is not merely a regulatory requirement but a critical component of customer satisfaction and brand reputation. The right gummy making machine should exhibit superior control mechanisms, allowing for meticulous regulation of parameters such as gummy weight, firmness, and ingredient dispersion to ensure a consistently high-quality product.
Optimizing Efficiency and Yield with the Right Gummy Machine
Optimizing efficiency and yield is central to maximizing profitability. Machines enhanced with intelligent software for real-time analytics and adjustments can substantially reduce waste and downtime. Additionally, equipment that enables rapid changeovers between different gummy formulations or shapes can drive efficiencies and expand production capabilities.
Comparing Different Gummy Maker Machines in the Market
An objective comparison of different gummy maker machines available in the market should involve a detailed inspection of their technologically advanced features, energy consumption profiles, and ease of maintenance. Evaluating customer reviews, after-sales service quality, and warranty terms can also be pivotal in making an informed purchasing decision.
Essential Components and Accessories for Gummy Manufacturing
The Role of Molds in Gummy Production
Molds are a fundamental element in gummy manufacturing, dictating the size, shape, and intricacy of the finished candies. The precision of mold design can significantly impact demolding processes and final product quality. Employing robust molds that resist deformation ensures consistent gummy dimensions and contributes to an efficient production line.
Utilizing Silicone for Gummy Making
Silicone materials are increasingly favored in gummy production due to their flexibility, non-stick properties, and durability. These materials enable manufacturers to produce complex shapes with great detail while also ensuring a smooth release of the gummy product, limiting waste and preserving structural integrity.
Automating the Process: Auxiliary Equipment for Gummy Machines
Automation through auxiliary equipment, such as depositor pumps and conveyor systems, is integral to upscaling gummy production. These innovations streamline the manufacturing process, from accurate ingredient deposition to seamless transport of molds through the setting, curing, and packaging stages.
Infusion and Flavoring Techniques for Gummy Manufacturing
Advanced infusion and flavoring techniques are employed to achieve a homogenous distribution of tastes and active ingredients within gummy candies. This includes the precise injection of flavorings, colorants, and functional components, such as vitamins or supplements, ensuring an enjoyable and consistent consumer experience.
Understanding the Importance of Quality Ingredients and Starch in Gummy Production
High-quality ingredients are the cornerstone of exceptional gummy production. The selection of premium gelatin or pectin, along with superior starches, can profoundly influence the texture, clarity, and shelf-stability of gummy candies. Starches play a particularly crucial role, often used in mold-making to create a non-stick environment and to absorb excess moisture, which enhances the structural properties of the gummies.
Troubleshooting Common Issues with Gummy Machines
Avoiding Common Mistakes in Gummy Making with the Right Gummy Machine
Selecting an appropriate gummy making machine is crucial to address the substantial challenges encountered during production. Proper maintenance and calibration of such equipment are non-negotiable to prevent mold and quality control issues, which can lead to inconsistencies in shape and ingredient distribution. Routine checks and adherence to manufacturing guidelines minimize potential production line disruptions and downtime, which are often costly. When it comes to the infusion of flavors and active ingredients, advanced dosing systems can resolve distribution problems, ensuring uniformity in taste and potency. By understanding and implementing these parameters, manufacturers can steer clear of the common mistakes associated with gummy making and maintain a high standard of product output.
Trends and Innovations in Gummy Machine Technology
The Impact of Automation and Industry 4.0 in Gummy Manufacturing
The integration of automation and Industry 4.0 into gummy manufacturing has revolutionized the production process, yielding substantial improvements in efficiency, consistency, and scalability. Utilization of smart sensors and control systems permits real-time monitoring and adjustments, reducing the margin of error and enhancing the precision of the final product. Consequently, this paradigm shift propels a reduction in labor costs and an increase in the capacity to respond swiftly to market demands.
Integrating Digitalization and Smart Technologies in Gummy Production
The incorporation of digitalization and smart technologies within gummy production workflows is imperative for the evolution of the industry. Centralized digital control systems and advanced analytics empower manufacturers to optimize operations and predict maintenance needs, thus averting unforeseen downtime. Significantly, this digital shift fosters enhanced product traceability and quality assurance throughout the manufacturing cycle.
Emerging Trends in Edible Production: The Future of Gummy Making Machines
As consumer preferences evolve, gummy making machines must adapt to suit emerging trends and dietary requirements. The advent of multi-flavor and multi-layered gummies necessitates sophisticated machines that can handle intricate production processes without compromising quality. There is a marked inclination towards machinery that supports the creation of edibles with enhanced nutritional profiles and those catered to specific dietary restrictions, reflecting the future trajectory of the gummy manufacturing sector.
Enhancing Sustainability and Eco-Friendly Practices in Gummy Manufacturing
Sustainability is ascending as a pivotal factor in the manufacturing sector, including gummy production. Innovations in machinery are increasingly oriented towards minimizing energy consumption and waste production. Manufacturers are envisioning the use of biodegradable materials and renewable energy sources to power their operations, elucidating a commitment to eco-friendly methods which, in turn, can attract a conscientious consumer base.
Exploring the Potential of 3D Printing for Gummy Molds and Production Equipment
The potential application of 3D printing technology in the fabrication of gummy molds and production equipment signifies a transformative prospect for customization and speed-to-market. Advanced 3D printing can offer unparalleled flexibility in mold design, allowing for rapid prototyping and enabling manufacturers to swiftly cater to niche markets and limited-edition product lines. This technology stands to redefine supply chain dynamics by enabling on-site production of equipment components, reducing reliance on external suppliers.
Read More From Techbullion
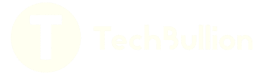