When purchasing machining abs plastic , you may encounter some common problems. This guide may help you; please read on
What is abs plastic and what are its properties?
ABS plastic is short for Acrylonitrile Butadiene Styrene. It is a common thermoplastic that can be used for a variety of things, from toys and electronics to automotive parts. It is common to find ABS plastic in the construction of FDM 3d printers.
ABS plastic has a number of properties that make it an excellent choice for 3d printing:
ABS can withstand high temperatures, making it ideal for use in hot extrusion processes.
It is strong and durable, so it can be used to print functional parts that will last over time.
How is abs plastic machined and what are the challenges involved?
Abs plastic machining is a challenging process. The material has high impact strength and low stiffness, which means that it will absorb energy during impact. Since it is a thermoplastic, it can be recycled and reused many times over.
The key challenges to machining abs plastic are:
1) High-temperature molding processes require high temperature cutting tools and coolant systems to prevent thermal distortion of the part.
2) Abs plastic can be machined with carbide tools but not with abrasive tools like HSS or cobalt steel tools because they tend to chip more easily. Carbide tooling is more expensive than HSS tooling but lasts longer, so there is less need for frequent tool changes during production runs.
3) ABS can be machined with a wide variety of tools including: carbide, HSS and cobalt steel tools. Carbide and HSS tooling are more expensive than cobalt steel but last longer so there is less need for frequent tool changes during production runs.
4) ABS plastic has a high thermal conductivity which makes it easy to machine using coolant systems that maintain the temperature of the cutting tool below its melting point.
What types of equipment or tools are used to machine abs plastic parts and products
The most common machining process used to machine ABS plastic parts and products is subtractive machining. This process uses a blade or cutting tool to remove material from the workpiece by cutting off chips and shaving them away.
The most common types of tools used for subtractive machining are:
Roughing tooling – roughing tools are designed to remove large amounts of material quickly, with minimal surface finish. They are typically used on the initial cuts in the part design; for example, milling out a bulkhead or cutting features into an existing piece
Finishing tooling – finishing tools are designed to produce a high quality surface finish on the workpiece, while also removing less material than a roughing tool would. Finishing tools can be used either before or after roughing operations. For example, if you need to make multiple secondary cuts that do not require much material removal (such as pocket molds), then you may use a finishing tool instead of a roughing tool
Specialty cutters – there are many specialty cutters available for use in plastics machining operations, such as slot drills, hole saws and broaches. These tools are designed specifically for use with ABS plastics , and can be used to cut out holes or other shapes in the material.
What factors need to be considered when machining abs plastic components
Are there any special safety precautions that need to be taken when working with abs plastic
ABS plastic is a tough and durable material. It’s an engineering plastic with good resistance to impact, heat, and chemicals. ABS can be used in a wide range of industries from automotive applications to aerospace manufacturing. However, there are several safety precautions that must be taken when working with ABS plastics.
Here are some tips for handling ABS:
Always wear protective eye gear when cutting or drilling ABS because it tends to splinter and fly off in large pieces during these processes.
Wear gloves during the machining process because small particles of ABS can get into the skin and cause irritation.
Keep your work area clean so that you don’t accidentally swallow any small pieces of ABS while working in it.
Wash your hands thoroughly after working with ABS plastics because these materials can irritate your skin when they come in contact with it for long periods of time or if they get on your skin under certain circumstances (for example, if you spill some water on yourself while working with them).
What finishing processes can be used on machined abs plastic parts
Finishing processes can be used on machined ABS plastic parts
Surface treatments are vital to ensure that your part has the best possible look and functionality. Most plastic products will undergo some type of surface treatment to improve their appearance and performance.
Types of finishes for plastic parts:
There are several types of finishing processes for machined ABS plastic parts. The most common types include anodizing, painting, electroplating and powder coating. Each type of process has its own advantages and disadvantages when producing ABS plastic parts.
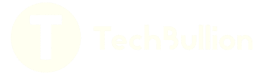