George Gemeinhardt of Northfield, IL, is a retired manufacturing manager whose main role was overseeing, planning, and coordinating the daily production process in manufacturing facilities. He has seen plenty of equipment downtime, scrapped products, and disengaged employees, costing manufacturing stakeholders much in lost profit and brand reputation.
But, when certain manufacturing techniques are put in place that emphasize the best way for work activities to flow seamlessly, he was surprised at how quickly and efficiently operations could be turned around.
The way of 20th Century manufacturing business models has caused an evolution in how large factories produce products. The implementation of the assembly line by Henry Ford, the use of plastics and plastic injection/extrusion machinery, and the introduction of robotic automation are likely the three most important manufacturing changes in current history that are comparable to the existing three main manufacturing management techniques of:
- Lean Manufacturing
- TPM (Total Productive Maintenance)
- Six Sigma
The Value of Lean Manufacturing
Lean manufacturing is about cutting the fat in manufacturing. This means reducing wasted time, energy, and materials in every phase of the production process, says George Gemeinhardt. A lean manufacturing company takes a top-down approach to make its products.
This starts with determining the product’s market price (along with the value to and the demand of customers) and implementing a system where manufacturing meets market demand and customer expectations. But it’s more complicated. There is a whole team of lean manufacturing experts whose role in the company is to continually create a competitive advantage by lowering operational costs to increase profits.
Improving Product Quality with Six Sigma
George Gemeinhardt agrees that better products will increase brand visibility, customer loyalty, and corporate profits. This is the goal of Six Sigma manufacturing principles – to engage in manufacturing management techniques that significantly reduce product defects or errors, resulting in a competitive edge and greater brand loyalty.
Six Sigma looks more closely at improving not only ‘on-the-floor’ activities but also the business processes behind manufacturing. Companies like General Electric and Honeywell were adopters of Six Sigma Lean Manufacturing processes. And both companies attributed this manufacturing management technique to record-breaking profits due to cost savings delivered by “business and operational excellence.”
TPM – A Holistic Approach to Manufacturing
Total Productive Maintenance or TPM focuses on the employees, machines, equipment, and supporting processes that can be maintained and improved to increase the integrity of production and the brand’s quality. Gemeinhardt can relate to a healthy and vibrant production process necessary for healthy profits.
TPM manufacturing is proactive and looks to reduce significantly equipment breakdowns, employee accidents, product defects, and processes that are running slowly. This is in opposition to the reactive and sometimes typical factory floor where equipment is run until it breaks down or needs servicing.
And, when employees are included as a vital component of the manufacturing process, George Gemeinhardt understands that Total Productive Maintenance as a manufacturing philosophy can be a win-win situation for workers and stakeholders.
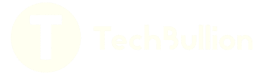