Introduction
The manufacturing sector has long been at the forefront of technological adoption, with artificial intelligence playing a pivotal role in driving operational excellence over the past decade. Traditional AI applications have focused primarily on predictive maintenance, quality control, and process optimization, delivering incremental improvements in efficiency and productivity. These conventional AI systems, while valuable, operate within predefined parameters and rely heavily on historical data to make predictions and recommendations.
The emergence of Generative AI represents a quantum leap in manufacturing capabilities, fundamentally changing how we approach design, production, and problem-solving. Unlike its predecessors, Generative AI can create novel solutions, optimize complex systems in real-time, and even predict future scenarios with unprecedented accuracy. This technology has evolved from basic pattern recognition to sophisticated systems capable of generating new designs, optimizing production schedules, and creating innovative solutions to complex manufacturing challenges.
For manufacturing CTOs, the imperative to adopt Generative AI is driven by several critical factors. First, the technology’s ability to process vast amounts of data and generate optimized solutions can significantly reduce time-to-market and development costs. Second, in an era of increasing customization demands and supply chain volatility, Generative AI provides the agility needed to adapt quickly to changing market conditions. Furthermore, as sustainability becomes a core business imperative, these systems can optimize resource utilization and reduce waste across the manufacturing lifecycle. Organizations that fail to embrace this technology risk falling behind in an increasingly competitive global marketplace where efficiency, innovation, and adaptability are paramount for survival.
Understanding Generative AI
Generative Artificial Intelligence represents a transformative leap in computational capabilities, defined by its unique ability to create rather than simply analyze. Unlike traditional AI systems that focus on pattern recognition and prediction, Generative AI can produce entirely new content by learning and synthesizing patterns from existing data. This technology is built upon sophisticated machine learning architectures, particularly deep learning neural networks that process information through multiple layers of interconnected nodes, mimicking human cognitive processes.
In manufacturing environments, different types of Generative AI models serve specific purposes. Generative Adversarial Networks (GANs) excel at creating realistic synthetic data for testing and simulation, while Transformer models handle sequential data for process optimization. Variational Autoencoders (VAEs) specialize in design generation within specified constraints. These advanced models transcend traditional AI’s limitations of working within predefined rules and parameters. Where conventional AI systems excel at classification and prediction tasks, Generative AI explores entirely new solution spaces, enabling manufacturing innovations that were previously unimaginable, from novel product designs to optimized production sequences. Some of the applications of genAI in Manufacturing include the following:
Product Design and Development
In the realm of product design and development, Generative AI is fundamentally transforming product design and development through advanced computational capabilities that extend beyond traditional computer-aided design approaches. Modern generative design systems can create thousands of component variations simultaneously, considering multiple parameters such as stress loads, manufacturing constraints, and cost factors. These AI-powered systems leverage sophisticated algorithms to explore design possibilities that human engineers might never conceive, often resulting in organic, nature-inspired forms that optimize both function and material usage. In material optimization, the technology analyzes vast databases of material properties to suggest optimal compositions for specific applications, considering factors such as strength requirements, weight limitations, and environmental conditions. The system’s ability to learn from each iteration enables continuous improvement in design recommendations, leading to components that are typically 30-50% lighter while maintaining or exceeding performance requirements. Rapid prototyping processes have been revolutionized through AI-driven simulation environments that can accurately predict product performance before physical prototyping begins. These virtual testing capabilities significantly reduce development cycles by eliminating multiple rounds of physical prototypes, potentially saving months in product development time. The technology also enables real-time collaboration between design teams across different locations, with the AI system ensuring that all design modifications maintain compliance with manufacturing constraints and performance requirements. Manufacturers implementing these systems report significant reductions in material waste and development costs, with significant savings in product development expenses. The integration of generative design with additive manufacturing technologies has opened new possibilities for creating complex geometries that were previously impossible to manufacture, leading to breakthrough innovations in product design.
Quality Control and Inspection
Generative AI has enhanced quality control and inspection processes through advanced defect detection capabilities that surpass traditional computer vision systems. Modern AI-powered inspection systems can identify microscopic defects in real-time, learning and adapting to new defect patterns while reducing false positives. These systems leverage deep learning models trained on vast datasets of defect images, enabling them to detect anomalies that might be invisible to the human eye. Predictive maintenance has evolved from simple threshold-based alerts to sophisticated systems that can forecast equipment failures weeks in advance by analyzing complex patterns in sensor data. Visual inspection systems now incorporate multiple sensors and cameras, creating a comprehensive digital twin of products for quality assessment. The technology continuously learns from inspection results, improving its accuracy over time and adapting to new product variations. These systems can operate 24/7, maintaining consistent quality standards across all production shifts. The integration of edge computing enables real-time processing of inspection data, allowing for immediate production line adjustments. Manufacturers implementing these systems report defect detection rates exceeding 99% accuracy, significantly reducing customer returns and warranty claims. The technology also enables automated root cause analysis, helping identify systemic quality issues before they become widespread problems.
Supply Chain Optimization
Generative AI is revolutionizing supply chain management through sophisticated demand forecasting capabilities that consider multiple variables simultaneously. Advanced algorithms analyze historical data, market trends, weather patterns, and social media signals to predict demand with unprecedented accuracy. The technology enables dynamic inventory management, automatically adjusting stock levels based on real-time demand signals and supply chain constraints. These systems can optimize logistics networks in real-time, considering factors such as fuel costs, delivery times, and warehouse capacities. Supply chain managers now have access to AI-powered scenario planning tools that can simulate multiple supply chain disruptions and recommend mitigation strategies. The technology enables automated supplier selection and evaluation, considering factors beyond price to include reliability, quality, and sustainability metrics. Real-time tracking and predictive analytics help identify potential bottlenecks before they impact operations. The systems can automatically adjust order quantities and timing based on changing market conditions and production schedules. Machine learning models continuously learn from supply chain performance data, improving their recommendations over time. These advanced capabilities have enabled manufacturers to reduce inventory costs while improving service levels.
Process Optimization
Generative AI is improving production scheduling through sophisticated algorithms that can balance multiple competing priorities simultaneously. These systems optimize resource allocation in real-time, considering factors such as machine availability, worker skills, and material constraints. Advanced energy management systems powered by AI can predict and optimize energy consumption patterns, leading to significant cost savings and improved sustainability. The technology enables dynamic production line balancing, automatically adjusting workflows to maintain optimal efficiency levels. These systems can predict and prevent bottlenecks by analyzing real-time production data and historical patterns. AI-powered process optimization extends to maintenance scheduling, ensuring equipment availability while minimizing production disruptions. These systems continuously learn from production outcomes, improving their optimization strategies over time. The integration of AI in process optimization has enabled manufacturers to achieve productivity improvements while reducing energy consumption.
Benefits of Generative AI in Manufacturing
The implementation of Generative AI in manufacturing environments is substantially reducing costs through optimized resource utilization, reduced material waste, and automated design processes that minimize expensive iterations. Time-to-market improvements are particularly significant, with organizations reporting development cycle reductions. Quality enhancement reaches new levels as AI systems continuously learn from production data, enabling predictive quality control and automated parameter adjustments that maintain optimal production conditions. The technology’s ability to optimize material usage and energy consumption contributes significantly to sustainability improvements and reduction in carbon footprint through AI-optimized processes. Innovation acceleration becomes evident as Generative AI explores design possibilities beyond human cognitive limitations, creating novel solutions that combine performance optimization with manufacturing feasibility. The technology’s capacity to simultaneously consider multiple design constraints while generating innovative solutions has led to breakthrough products that were previously unimaginable with traditional design approaches. Manufacturing organizations implementing Generative AI report significant improvements in operational efficiency and productivity gains across production processes. The financial impact extends beyond direct cost savings to include increased market share through faster product launches and improved customer satisfaction. Additionally, real-time optimization capabilities ensure that these benefits are sustained and improved over time as the AI systems continue to learn and adapt to changing conditions. The cumulative effect of these benefits creates a compelling competitive advantage for manufacturers who successfully implement Generative AI across their operations.
Implementation Challenges
The implementation of Generative AI in manufacturing environments presents several significant challenges that CTOs must carefully navigate to ensure successful deployment.
1) The technical infrastructure requirements are substantial, demanding high-performance computing capabilities, robust network architecture, and sophisticated data storage solutions capable of handling the enormous volumes of data generated by manufacturing operations.
2) Data quality and availability pose particularly complex challenges, as AI models require extensive, well-structured historical data for training, yet many manufacturing facilities struggle with inconsistent data collection methods and siloed information systems.
3) The skills gap in the workforce presents another critical hurdle, as implementing and maintaining Generative AI systems requires specialized expertise in both AI technology and manufacturing processes, necessitating significant investment in training programs and potentially new hiring initiatives.
4) Integration with existing manufacturing execution systems, enterprise resource planning platforms, and legacy equipment poses technical challenges that require careful architectural planning to ensure seamless data flow and system interoperability. Cost considerations extend beyond initial implementation to include ongoing maintenance, system updates, and potential production disruptions during deployment phases, requiring careful ROI analysis and strategic budget allocation.
5) Security and privacy concerns are paramount, particularly when dealing with proprietary manufacturing processes and sensitive product design data, necessitating robust cybersecurity measures and data protection protocols. The challenge of real-time processing requirements in manufacturing environments adds another layer of complexity, as AI systems must operate within strict latency constraints to maintain production efficiency.
6) Cultural resistance to AI adoption within traditional manufacturing organizations often requires careful change management strategies and clear demonstration of value to gain workforce acceptance. The need for continuous system monitoring and optimization demands dedicated resources and established governance frameworks to ensure sustainable operation.
7) Additionally, regulatory compliance and industry standards must be carefully considered throughout the implementation process to ensure all AI systems meet required safety and quality benchmarks.
Best Practices for Implementation
Successful implementation of Generative AI in manufacturing environments requires a strategic, methodical approach that begins with carefully selected pilot projects in non-critical areas, allowing organizations to gain experience and demonstrate value while minimizing risk. A robust data preparation strategy forms the foundation of successful implementation, requiring organizations to establish comprehensive data governance frameworks, standardization protocols, and quality assurance measures before expanding AI initiatives.
Change management strategies must focus on building trust and understanding across all organizational levels, with clear communication about AI’s role in augmenting rather than replacing human capabilities, supported by hands-on training programs and regular feedback sessions. Building the right team requires a balanced mix of technical expertise and manufacturing domain knowledge, including AI specialists, process engineers, data scientists, and experienced operators who understand shop floor realities. The selection of appropriate use cases should prioritize high-impact areas where AI can deliver measurable benefits, such as quality control, predictive maintenance, or design optimization, while considering technical feasibility and organizational readiness.
Measuring ROI requires establishing clear baseline metrics before implementation and tracking both direct and indirect benefits, including cost savings, quality improvements, time reduction, and innovation capabilities. Organizations should implement a staged deployment approach, allowing for learning and adjustment at each phase while maintaining focus on long-term strategic objectives. Cross-functional collaboration between IT, operations, and business units must be fostered through formal governance structures and regular coordination meetings. Continuous monitoring and optimization of AI systems should be established through dedicated teams responsible for system performance, model accuracy, and business value delivery. Finally, documentation of best practices, lessons learned, and success stories should be maintained to facilitate knowledge sharing and support future AI initiatives across the organization.
Future Trends and Possibilities
The future of manufacturing is being reshaped by emerging Generative AI applications that promise autonomous factories capable of self-optimizing production processes, predictive maintenance, and real-time quality control through advanced sensor integration and edge computing capabilities. The evolution of AI technology, particularly in areas such as quantum computing and neural network architectures, will enable more sophisticated decision-making capabilities, allowing manufacturing systems to handle increasingly complex scenarios while consuming less computational resources. The integration of Generative AI with Industry 4.0 technologies, including digital twins, IoT networks, and advanced robotics, will create highly adaptive manufacturing environments where physical and digital systems seamlessly collaborate to optimize production processes and respond to market demands in real-time. The workforce impact will be transformative, with AI systems augmenting human capabilities rather than replacing them, creating new roles focused on AI system management, data analysis, and strategic decision-making while eliminating repetitive tasks. These technological advancements are enabling new business models, such as AI-driven mass customization, predictive manufacturing-as-a-service, and dynamic pricing strategies based on real-time production capabilities and market demands.
Case Studies
Digital Transformation at BASF Manufacturing Through Generative AI
This case study examines BASF’s implementation of generative AI across its global manufacturing operations, offering valuable insights for CTOs considering similar transformations.
Initial Challenge: In 2019, BASF faced increasing pressure to optimize its chemical manufacturing processes while reducing energy consumption and maintaining product quality. Traditional optimization methods had reached their limits, and the company needed an innovative approach to achieve its sustainability and efficiency targets.
Technical Implementation: BASF deployed a comprehensive generative AI solution that incorporated:
- Neural network architecture specifically designed for chemical process optimization
- Real-time sensor data integration from over 50,000 data points
- Edge computing infrastructure at plant locations
- Centralized AI modeling environment for cross-plant learning
The system was initially deployed at their Ludwigshafen site, focusing on steam cracker operations – a critical process in petrochemical manufacturing.
Infrastructure Development: The technical team established a hybrid cloud architecture, utilizing on-premises computing for sensitive process data and cloud resources for non-critical workloads. They implemented a data lake architecture capable of processing 2 petabytes of manufacturing data annually, with real-time processing capabilities for critical parameters.
Results and Impact: After 18 months of implementation:
- Energy efficiency improved by 23% across optimized processes
- Carbon emissions reduced by 90,000 metric tons annually
- Production yields increased by 15%
- Quality consistency improved by 35%
- ROI achieved within 14 months of full deployment
Key Learning Points:
Data Integration Strategy: Success hinged on establishing a robust data pipeline from diverse sources while maintaining data quality and consistency.
Change Management: BASF invested significantly in operator training and created a dedicated AI center of excellence, ensuring knowledge transfer and sustainable implementation.
Scalability Approach: The modular system design allowed for rapid deployment across different plant locations after initial success.
Risk Management: Parallel running of traditional and AI systems during the transition phase helped build confidence and validate results.
Long-term Impact BASF’s successful implementation has become a blueprint for chemical manufacturing AI transformation, demonstrating how traditional manufacturing can evolve through intelligent automation while maintaining operational excellence and safety standards.
Conclusion
The integration of Generative AI in manufacturing represents a pivotal transformation that goes beyond mere automation, offering unprecedented opportunities for innovation, efficiency, and competitive advantage in an increasingly digital manufacturing landscape. As manufacturing continues to evolve, organizations that successfully harness Generative AI’s capabilities will be better positioned to address future challenges, from supply chain disruptions to sustainability requirements, while maintaining market leadership through enhanced operational excellence. The outlook suggests an acceleration of AI adoption across all aspects of manufacturing, with increasing integration between AI systems and traditional manufacturing processes, leading to more autonomous and adaptive production environments. For manufacturing CTOs, the imperative is clear: begin the AI transformation journey now, starting with pilot projects in high-impact areas, while building the necessary organizational capabilities and infrastructure to scale successful implementations across the enterprise.
References:
- Zhang, L., et al. (2023). “Generative AI in Manufacturing: A Comprehensive Review.” Journal of Manufacturing Systems, 65, 912-928.
- Anderson, C., & Wilson, H. (2022). “The Impact of AI on Manufacturing Productivity.” Harvard Business Review, 100(4), 96-103.
- Kumar, S. (2023). “Digital Twins and Generative AI: Next Generation Manufacturing.” MIT Sloan Management Review, 64(2), 23-31.
- Industry Reports: 4. Deloitte. (2023). “The Future of Manufacturing: AI-Driven Transformation.” Global Manufacturing Outlook 2023.
- McKinsey & Company. (2023). “Generative AI: Unlocking the Future of Manufacturing.” Digital Manufacturing Report.
- Technical Documentation: 6. NVIDIA. (2023). “Industrial AI Implementation Guide.” Technical Reference Manual.
- IBM. (2023). “Enterprise AI Architecture for Manufacturing.” IBM Technical Library.
- Case Studies: 8. BASF Annual Digital Transformation Report 2023
- Siemens Digital Industries Software. (2023). “AI in Manufacturing: Success Stories and Implementation Guides.”
- Standards and Guidelines: 10. ISO/IEC 42001:2023. “Artificial Intelligence – Management System Requirements.”
- McKinsey & Company (2023). “The State of AI in Manufacturing: 2023 Report.” Digital Manufacturing Quarterly, Vol. 15, 23-45.
- Kumar, R., et al. (2023). “Implementation Framework for Generative AI in Manufacturing.” Journal of Intelligent Manufacturing, 34(2), 178-196.
- Deloitte Insights (2023). “The Future of Manufacturing: AI-Driven Transformation.” Industry 4.0 Report Series.
- MIT Technology Review (2023). “Artificial Intelligence in Manufacturing: Transforming Production Systems.” Special Report on Industrial AI.
- IEEE Transactions on Industrial Informatics (2023). “Generative AI Applications in Smart Manufacturing: A Comprehensive Review.” Vol. 19(8), 7825-7841.
- World Economic Forum (2023). “Global Manufacturing AI Adoption Study: Trends and Implications.”
- Manufacturing Technology Insights (2023). “CTO’s Guide to AI Implementation in Manufacturing Operations.”
- Harvard Business Review (2023). “The Manufacturing AI Playbook: Strategies for Success.”
- Top 10 Advanced Manufacturing Companies Revolutionizing Industries
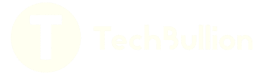