Gate valves and ball valves are two commonly used types of valves in various industrial applications, each serving distinct purposes based on specific operational needs. Understanding the differences between them can help prevent costly mistakes, inefficiencies, and system failures. This article will break down the core differences between these valves, explaining their mechanisms, applications, and the pros and cons of each, so you can make an informed decision for your specific needs.
Design Differences Between Gate and Ball Valves
Gate Valve Design: A gate valve uses a wedge-shaped gate that moves perpendicular to the fluid flow to open or close the valve. The key components of a gate valve include the body, gate, stem, handwheel (or actuator), bonnet, seat, and packing. The gate is designed to create a tight seal when closed, preventing leakage by sitting firmly against the seat. The operation of a gate valve is typically slower, requiring multiple turns of the handwheel to raise or lower the gate. Gate valves are ideal for applications where full isolation of the flow is needed, but they are less effective at throttling or regulating flow due to the nature of their design. Additionally, the gate valve’s larger body structure demands more space, which can be a consideration when selecting it for particular installations.
Ball Valve Design: A ball valve, on the other hand, features a spherical ball with a hole in the center that rotates to control the flow. The ball is housed in a valve body, with a stem that connects the ball to the actuator or handle, allowing for a quick, quarter-turn operation. When the valve is closed, the ball obstructs the flow path, creating a reliable seal. Ball valves are known for their quick, efficient operation, requiring only a 90-degree turn of the handle to either fully open or close the valve. Their design makes them ideal for applications requiring frequent cycling or quick shutoff capabilities, such as in emergency situations. Furthermore, ball valves offer superior sealing compared to gate valves, ensuring minimal leakage when in the closed position.
The design of the ball valve is more compact than that of the gate valve, making it suitable for tighter spaces. However, unlike gate valves, ball valves are generally unidirectional, meaning the flow must be aligned with the valve’s design for optimal performance. This unidirectional characteristic simplifies installation by ensuring that the flow direction is correctly aligned with the valve.
How Gate Valves Operate
Gate valves are linear motion valves, meaning they operate by moving a gate up or down to control the flow of fluid. When the valve is fully open, the gate is raised, allowing an unobstructed path for the fluid to flow through the valve, which minimizes pressure drop. Gate valves are primarily used in applications requiring full shut-off control or when a simple on/off flow is needed. The operation of gate valves requires multiple turns of the valve stem to raise or lower the gate, which can be a slower process compared to other valve types, such as ball valves.
The gate in a gate valve is typically made of a wedge or a parallel slide, and it is moved using a stem connected to the actuator. The actuator may be manual or automated, depending on the system requirements. Gate valves are designed to provide a tight seal when closed, ensuring that there is no leakage. They are often used in systems with high-pressure environments or in situations where flow regulation is not needed but rather just the full opening or closing of the valve. While gate valves are durable and suitable for many industrial applications, their slower operating speed makes them less ideal for systems requiring quick flow adjustments.
How Ball Valves Operate
Ball valves are quarter-turn valves that use a ball with a hole in the center to control the flow of fluid. When the valve handle is rotated by 90 degrees, the ball rotates, aligning the hole with the flow path to either open or close the valve. This simple quarter-turn mechanism allows for fast operation, making ball valves ideal for applications requiring quick opening and closing actions.
Ball valves offer a tight seal when closed, and their ability to operate in both fully open and fully closed positions makes them highly reliable for on/off control. Unlike gate valves, ball valves can be used in systems where some degree of throttling or flow regulation is necessary, though their primary strength lies in full-flow control. The ball’s design allows for minimal friction and pressure drop during operation, and the valve’s quick and efficient shut-off action makes it a preferred choice for high-pressure systems, water treatment, oil, and gas industries. Ball valves are also known for their durability, as they are less prone to wear and tear compared to other types of valves due to their straightforward design.
Advantages and Disadvantages of Gate Valves
Advantages of Gate Valves:
- Precise Flow Control: Gate valves are ideal for applications requiring gradual flow adjustments. Their linear motion mechanism allows operators to control flow rates precisely by partially opening or closing the valve.
- Minimal Pressure Drop: When fully open, gate valves create little resistance to the flow of fluid, making them suitable for high-pressure systems where energy efficiency and minimizing pressure loss are important.
- Durability: Known for their sturdy construction, gate valves can withstand harsh conditions, including high pressures and abrasive media. Their robust design contributes to longer service life and reduces maintenance needs.
- Cost-Effectiveness: Generally, gate valves are less expensive compared to other valve types, making them a cost-effective choice for low-pressure systems and large-scale installations.
Disadvantages of Gate Valves:
- Slow Operation: Unlike ball valves, gate valves operate slowly due to their linear motion design. This can be a disadvantage in situations that require rapid flow adjustments.
- Susceptibility to Leakage in Partial Positions: When gate valves are only partially open, they can be more prone to leakage. Proper installation and regular maintenance are required to maintain their sealing performance.
- Not Ideal for Throttling in Some Cases: While gate valves can offer flow control, their performance in throttling is often less precise than other types of valves. This can limit their use in systems where fine regulation is necessary.
Advantages and Disadvantages of Ball Valves
Advantages of Ball Valves:
- Quick and Efficient Operation: Ball valves are renowned for their swift response. The quarter-turn design allows operators to open or close the valve with ease, making them ideal for applications that demand fast and reliable shut-off.
- Excellent Shut-Off Capability: When fully closed, ball valves offer a superior seal, ensuring minimal leakage. This makes them suitable for systems where leak prevention is critical, such as in high-pressure or hazardous applications.
- Versatility in Application: Ball valves are effective across a broad spectrum of industries, handling everything from water and gas to corrosive chemicals. Their ability to perform well under high-pressure and high-temperature conditions adds to their versatility.
- Minimal Maintenance: Ball valves typically have fewer moving parts and are less prone to wear and tear, requiring minimal maintenance for long-term reliability.
Disadvantages of Ball Valves:
- Limited Flow Control: While excellent for on/off operations, ball valves are not ideal for applications that require precise throttling. They generally operate in fully open or fully closed positions, offering limited flow regulation.
- Higher Torque Requirements for Larger Sizes: In larger systems, ball valves can require more torque to operate, which might necessitate additional power or specialized equipment.
- Vulnerability to Abrasive Fluids: While ball valves are robust, they may wear out more quickly when dealing with highly abrasive fluids, especially if the ball and seat are not made from appropriate materials.
Maintenance and Durability Comparison: Gate Valve vs Ball Valve
Durability
Ball valves are renowned for their long-lasting durability, primarily due to their simple design with fewer moving parts. The design incorporates a spherical ball that rotates to either allow or block fluid flow, creating a tight seal against the valve seat. This design minimizes wear and tear, offering superior sealing efficiency even after prolonged use, which makes them highly reliable for critical applications. Ball valves are particularly advantageous in systems that require frequent operation, as they have fewer components that can wear out, reducing maintenance needs over time.
Gate valves, on the other hand, are more complex, relying on a gate (or disc) that moves vertically or slides to regulate fluid flow. This design makes gate valves more susceptible to wear, especially at the sealing surfaces. Over time, the gate and seat can degrade due to fluid friction, leading to the potential for leaks and diminished sealing capabilities. Additionally, gate valves may encounter issues with their stem, which can corrode, break, or seize, further impacting their durability. As a result, gate valves often require more frequent inspections and maintenance to ensure optimal performance.
Maintenance Requirements
Ball valves require less maintenance compared to gate valves. Due to their fewer moving parts and efficient sealing mechanism, ball valves are easier to operate and maintain. The quarter-turn operation of a ball valve also makes it less prone to damage caused by wear, as the spherical ball’s movement does not generate excessive friction. Their robust design ensures that once installed, they can operate with minimal downtime and repair needs.
Gate valves, in contrast, demand more intensive maintenance. The linear motion of the gate, which slides up and down to control flow, can cause wear on the valve seat, resulting in a gradual decrease in sealing efficiency. Gate valves are more likely to encounter operational issues, particularly in systems that experience fluctuating pressures or temperature extremes. Debris can also accumulate around the gate, further complicating maintenance. Regular servicing is required to prevent these issues from compromising the valve’s functionality.
Applications of Gate Valves
Gate valves are commonly used in industries that require full flow control with minimal obstruction. These valves are especially beneficial in systems where the flow needs to be either fully on or fully off, and precise throttling is not necessary. Their applications span a wide range of sectors:
- Oil and Gas Industry: Gate valves are widely used in the oil and gas industry due to their durability and ability to manage high-pressure environments. They are often used in pipeline systems where a reliable shutoff mechanism is needed.
- Pharmaceutical and Chemical Industries: These industries require valves that can ensure the integrity of the process and prevent contamination. Gate valves, with their tight shutoff, are ideal for controlling the flow of chemicals or pharmaceutical substances.
- Manufacturing and Automotive Industries: In these industries, gate valves are used in fluid control systems where the need for quick opening and closing is not as critical, but a full flow is required.
- Water Treatment Plants: Gate valves are used in large-scale water treatment systems where they help in isolating sections of the system or controlling the flow of water with minimal resistance.
- Marine Industry: Gate valves are utilized in shipbuilding for the control of water flow, particularly in ballast systems and other vital shipboard processes.
Applications of Ball Valves
Ball valves are widely appreciated for their ability to quickly and reliably control the flow of gases and liquids. Due to their simple quarter-turn operation, they are ideal for both on/off and low-pressure applications. Here are some of the key sectors where ball valves are frequently applied:
- Oil and Gas Industry: Ball valves are used extensively in both upstream and downstream sectors for controlling the flow of oil and gas. Their fast-opening and closing capabilities make them ideal for situations where quick action is necessary, particularly in offshore drilling and processing operations.
- Petrochemical Industry: The petrochemical industry often utilizes ball valves for controlling the flow of highly pressurized fluids in processing and refining stages. Their durability in high-pressure environments and tight shut-off capabilities make them essential in this field.
- Water Distribution and Wastewater Management: Ball valves are commonly found in water treatment and distribution systems. Their ability to provide a quick shut-off helps to reduce the risk of water hammer, a common issue in these types of systems.
- Food and Beverage Industry: In the food and beverage sector, ball valves are used to control the flow of liquids like water, syrup, and other ingredients. The valves are favored due to their hygiene standards, ease of operation, and ability to be completely sealed, preventing contamination.
- HVAC Systems: In heating, ventilation, and air conditioning systems, ball valves are employed for controlling the flow of air or fluids. Their efficient operation and minimal space requirement make them ideal for managing temperature and pressure in HVAC systems.
Key Differences Between Gate Valves and Ball Valves
Feature | Gate Valve | Ball Valve |
Operation Speed | Slower operation with multiple turns to open/close. | Quick operation with a quarter-turn (90°) to open/close. |
Flow Control | Best for full flow control, limited throttling ability. | Offers some throttling control, better for on/off control. |
Pressure and Temperature Tolerance | Excellent for high-pressure systems, performs well in both high and low temperatures. | Suitable for a wide range of temperatures, but may generate water hammer in high-pressure systems. |
Durability & Maintenance
Cost |
Requires more maintenance, especially with debris accumulation. | Low maintenance, highly durable with fewer moving parts. |
Cost | Lower initial cost, but more prone to corrosion, requiring more frequent repairs and replacements. | Higher upfront cost, but more durable and offers better longevity with tight seals, reducing long-term maintenance. |
Applications | Used in high-pressure systems, water pipelines, oil pipelines, steam systems, and large-scale industrial applications. | Ideal for quick shut-off applications, often used in residential water systems, gas pipelines, and chemical processing. |
Sealing Efficiency | May require time to fully seal, can leak if not maintained properly. | Provides a tighter, leak-proof seal, although seals may wear over time. |
Risk of Water Hammer | Less likely to cause water hammer due to slow operation. | Can cause water hammer if closed too quickly. |
Flow Rate Control | Limited throttling ability, works best when fully open or fully closed. | Better for throttling, though not recommended for continuous throttling. |
Maintenance Frequency | Requires regular inspection and maintenance to ensure optimal performance. | Requires minimal maintenance due to its simple design. |
When to Choose Between Gate Valve and Ball Valve
Choosing the right valve depends on your system’s specific requirements:
- If your application requires frequent operation and minimal leakage: A ball valve is likely your best option.
- If you need a cost-effective solution for isolating large volumes of fluid: A gate valve will likely suit your needs.
By understanding the operational differences, cost implications, and practical applications of each valve type, you can make an informed decision that meets the needs of your project, ensures safety, and avoids unnecessary operational costs.
Conclusion
Gate valves and ball valves are both essential components in controlling fluid flow, but they serve different needs based on their design, operation, and performance characteristics. Gate valves, with their linear motion and multiple turns to operate, are best for applications requiring infrequent operation, such as in high-pressure systems where gradual flow control is needed. They offer reliable shut-off but can be prone to wear and leakage over time. In contrast, ball valves provide rapid, quarter-turn operation, ideal for systems that require quick shut-off or frequent use. Ball valves are known for their superior sealing ability and durability, making them highly effective in high-pressure and corrosive environments. Though more expensive upfront, they tend to be more cost-effective in the long run due to their ease of maintenance and lower risk of leakage. The choice between the two ultimately depends on the specific requirements of the system, including flow control precision, operational speed, and long-term cost considerations.
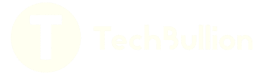