Imagine a world where you can turn your wildest ideas into tangible objects with just the touch of a button. A place where you no longer have to wait weeks or even months for a prototype to be manufactured, but instead witness your creation come alive right before your eyes. Welcome to the revolution that is 3D printing – a game-changing technology that is reshaping manufacturing processes as we know them. In this blog post, we will take you on an exhilarating journey through the transformative power of 3D printing and how it is propelling industries toward new heights of innovation and efficiency. So fasten your seatbelts and get ready to witness the birth of a whole new era in manufacturing.
Introduction to 3D Printing
3D printing is an additive manufacturing technology that creates three-dimensional objects by successively laying down thin layers of material. 3D printing is also known as stereolithography, powder bed fusion, selective deposition modeling, direct energy deposition, and many other names.
The first 3D printer was invented in the 1980s by Chuck Hull, and the technology has been increasingly adopted by manufacturing companies since then. In 2012, additive manufacturing equipment sales totaled $2.2 billion globally. In 2013, that figure grew to $3.07 billion. And in 2014, it is expected to reach $5.2 billion globally.
The benefits of 3D printing are numerous: it can be used to create complex shapes that would be otherwise impossible to manufacture; it is a much faster process than traditional manufacturing methods; it reduces waste; and it can be used to create customized products on-demand.
Despite these advantages, there are some challenges associated with 3D printing. One challenge is the high cost of 3D printers and materials; another challenge is the limited range of materials that can be used with 3D printers; and yet another challenge is the lack of standardization in the industry. But despite these challenges, 3D printing is poised to revolutionize manufacturing processes across a wide range of industries in the years to come.
Benefits of 3D Printing for Manufacturing
The use of 3D printing technology in the manufacturing process can bring many benefits to businesses, including improved product quality, reduced production costs, and shorter lead times.
Improved Product Quality: One of the main benefits of using 3D printing technology for manufacturing is the improved product quality that it can offer. With 3D printing, businesses can produce products with much finer details and smoother surface finishes than what is possible with traditional manufacturing techniques. In addition, 3D printing can enable businesses to create products with complex geometries and internal structures that would be difficult or impossible to create using traditional manufacturing methods.
Reduced Production Costs: Another key benefit of 3D printing for manufacturing is the potential to reduce production costs. 3D printing can eliminate the need for expensive tooling and other production setup costs associated with traditional manufacturing processes. In addition, 3D printed parts often require less material than their counterparts manufactured using traditional techniques, which can further reduce production costs.
Shorter Lead Times: The use of 3D printing technology can also help businesses reduce their lead times on new product development projects. With traditional manufacturing methods, businesses typically have to wait for tooling and other production setup processes to be completed before they can begin mass production of a new product. However, with 3D printing, businesses can produce prototype parts quickly and easily, without having to wait for tooling or other preparations. This enables businesses to get their new products to market faster and reduces the risk inherent in developing new products .
Different Types of 3D Printers
In the past few years, there has been a surge in popularity of 3D printing technology. This additive manufacturing process has many benefits over traditional manufacturing methods, making it an attractive option for businesses and consumers alike. But what exactly is 3D printing? And what are the different types of 3D printers available on the market today?
3D printing, also known as additive manufacturing, is a process whereby three-dimensional objects are created from a digital file. The objects are created by successively layers of material until the desired shape is achieved. This technique stands in contrast to traditional subtractive manufacturing methods, such as machining or milling, whereby objects are created by removing material from a larger block.
There are numerous advantages to using 3D printing technology. Perhaps most importantly, it allows for highly customized products to be created quickly and easily. Additionally, 3D printing can be used to create complex shapes that would be difficult or impossible to produce using traditional manufacturing methods. And because there is no need for costly moulds or dies, 3D printing can be an extremely cost-effective way to produce small batches of custom products.
There are several different types of 3D printers available on the market today. Each type has its own strengths and weaknesses, so it’s important to choose the right printer for your specific needs. Some of the most popular types of 3D printers include:
FDM Printers: FDM (fused deposition modelling) printers use molten plastic-based filaments to create 3D objects. This type of printer is relatively inexpensive and can produce highly detailed models.
SLA Printers: SLA (stereolithography) printers use a photo-reactive resin that hardens when exposed to ultraviolet light. As a result, these printers are capable of producing highly detailed and complex models with smooth surfaces.
SLS Printers: SLS (selective laser sintering) printers use a laser to fuse plastic or metal powders into an object. This type of printer can be expensive but produces very strong and robust parts suitable for use in engineering applications.
PolyJet Printers: PolyJet printers are similar to inkjet printers, except instead of printing with ink they dispense liquid photopolymers which harden when exposed to UV light. These printers are capable of producing highly precise models with intricate details and smooth surfaces.
Ultimately, there is no one-size-fits-all solution when it comes to 3D printing technology – so it’s important to choose the right printer for your specific needs. However, whatever type you decide on, you’ll be sure appreciate all the benefits 3D printing has to offer.
Applications of 3D Printing in Manufacturing Processes Platforms
A new technology called 3D printing is changing the way we create objects.3D printing is a process of making three-dimensional solid objects from a digital file. The creation of a 3D printed object is achieved using additive processes, where successive layers of material are laid down in different shapes.
3D printing has been used in manufacturing for some time now, but it is only recently that the technology has become mainstream. There are many different applications for 3D printing in manufacturing, from creating prototypes to full-scale production runs.
3D printing can be used to create prototypes of products before they go into production. This is a quick and cost-effective way to test out new designs and make sure that they meet all the necessary requirements.
3D printing can also be used for low-volume production runs. This is a great option for companies that want to produce small batches of custom products or parts without incurring the high costs associated with traditional manufacturing methods.
In addition, 3D printing can be used to create molds and tooling for injection molding and other manufacturing processes. This can lead to significant savings in time and money, as well as allowing for more intricate designs that would not be possible with traditional methods.
Design Challenges and Considerations
Additive manufacturing, also known as 3D printing, is a process of making a three-dimensional object from a digital file. The emergence of 3D printing has led to new challenges and considerations for designers and manufacturers.
Some of the challenges that need to be considered when designing for 3D printing include:
1. Material Selection: There are many different materials that can be used for 3D printing, each with its own unique properties. Selecting the right material for your application is critical to ensuring the success of your print.
2. Print Settings: The settings you use on your 3D printer will have a big impact on the final quality of your print. It’s important to experiment with different settings to find what works best for your particular design and printer.
3. Slicing: Slicing is the process of converting a 3D model into individual layers that can be printed by a 3D printer. This is a crucial step in the printing process, and there are many different slicing software programs available, each with its own advantages and disadvantages.
4. Support Structure: Support structures are necessary in some cases to prevent parts of your design from sagging or collapsing during the printing process. It’s important to carefully consider whether or not support structures are needed for your design and, if so, how to incorporate them into your overall design plan.
5. Finishing Techniques: There are many different ways to finish a print, from painting and polishing to sanding and finishing. Choosing the right finishing method for your design can make a huge difference when it comes to the quality of the final product.
Summary and Conclusions
Rapid prototyping and 3D printing technology has transformed manufacturing processes across a broad range of industries in recent years. Perhaps the most significant impact has been in the area of product development, where companies are now able to rapidly produce prototypes and test them before committing to large-scale production runs.
This has led to a more agile and iterative approach to product development, where design changes can be quickly implemented and tested. It also enables companies to bring new products to market much faster than was previously possible.
In addition, 3D printing is also being used increasingly for final production runs of certain products. This is particularly beneficial for complex or bespoke items where traditional manufacturing methods would be too slow or costly.
It is clear that 3D printing is having a major impact on manufacturing processes and will continue to do so in the years ahead.
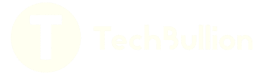