Introduction
When it comes to electronic product development, custom circuit board design plays a crucial role in bringing ideas to life. As businesses and entrepreneurs strive to create innovative products, the journey from prototype to production can be challenging. In this comprehensive guide, we will explore effective strategies for scaling up custom circuit board design, ensuring a smooth transition from concept to mass production.
Understanding the Importance of Custom Board Design
The Role of Custom Circuit Boards in Electronic Product Development
Custom circuit boards are the backbone of electronic products. They provide the necessary connections and components required for the product to function as intended. By designing a custom board, engineers can optimise the layout, minimise the size, and enhance the overall performance of the product.
Benefits of Custom Board Design
- Tailored to specific product requirements
- Improved efficiency and reliability
- Reduced costs through optimization
- Faster time-to-market
Planning and Prototyping
Defining Product Requirements
Before embarking on custom board design, it is essential to clearly define the product requirements. This includes understanding the desired functionality, power requirements, connectivity options, and any specific constraints or regulations that need to be met.
Creating a Proof of Concept
Once the requirements are established, the next step is to create a proof of concept. This involves developing a basic prototype that demonstrates the core functionality of the product. The proof of concept helps validate the design approach and identifies any potential challenges early in the process.
Iterative Prototyping and Testing
With the proof of concept in place, iterative prototyping and testing begin. This phase involves refining the design, testing different components, and optimising the layout. Rapid prototyping techniques, such as 3D printing and breadboarding, can be used to quickly test and iterate on the design.
Design Considerations for Scaling Up
Component Selection and Availability
When scaling up custom board design, component selection becomes critical. It is important to choose components that are readily available, reliable, and cost-effective. Partnering with reputable suppliers and considering alternative components can help mitigate supply chain risks.
Design for Manufacturing (DFM)
Design for Manufacturing (DFM) principles should be incorporated from the early stages of custom board design. DFM involves designing the board in a way that optimises manufacturability, reduces assembly time, and minimises potential defects. This includes considerations such as component placement, trace routing, and solder mask design.
Thermal Management and Power Distribution
As the complexity of the product increases, thermal management and power distribution become crucial factors. Proper thermal management ensures that the board operates within safe temperature ranges, preventing overheating and ensuring reliability. Power distribution networks should be carefully designed to provide stable and sufficient power to all components.
Collaboration and Communication
Engaging with Manufacturers and Suppliers
Effective collaboration with manufacturers and suppliers is essential for successful scaling up. Establishing open lines of communication, sharing design files, and discussing manufacturing capabilities can help identify potential issues early and ensure a smooth transition to production.
Cross-Functional Team Collaboration
Scaling up custom board design requires collaboration across various teams, including hardware, software, mechanical, and quality assurance. Regular meetings, design reviews, and clear documentation can facilitate effective communication and ensure that all team members are aligned towards the common goal.
Documentation and Version Control
Maintaining comprehensive documentation and version control is crucial throughout the design process. This includes schematic diagrams, board layouts, bill of materials (BOM), and assembly instructions. Proper documentation ensures that the design can be easily understood, replicated, and modified as needed.
Testing and Validation
Functional Testing
Functional testing is performed to verify that the custom board meets the desired specifications and performs as intended. This includes testing individual components, subsystems, and the overall product functionality. Automated testing tools and test jigs can streamline the testing process and ensure consistent results.
Environmental and Reliability Testing
Environmental and reliability testing helps assess the board’s ability to withstand various operating conditions and stresses. This includes tests for temperature, humidity, vibration, and electromagnetic compatibility (EMC). Rigorous testing ensures that the board can perform reliably in real-world scenarios.
Compliance and Certification
Depending on the target market and application, custom boards may need to comply with specific regulations and standards. This can include safety certifications, such as UL or CE, and electromagnetic compatibility (EMC) requirements. Engaging with certification bodies early in the design process can help ensure compliance and avoid delays in production.
Manufacturing and Assembly
Choosing the Right Manufacturing Partner
Selecting the right manufacturing partner is critical for successful scaling up. Consider factors such as experience, capabilities, quality control processes, and communication when evaluating potential partners. Building a strong relationship with the manufacturer can lead to improved efficiency, cost savings, and faster time-to-market.
Design for Assembly (DFA)
Design for Assembly (DFA) principles should be incorporated to optimise the assembly process. This includes considerations such as component placement, orientation, and accessibility. DFA helps reduce assembly time, minimise errors, and improve overall manufacturing efficiency.
Quality Control and Inspection
Implementing robust quality control and inspection processes is essential to ensure the consistency and reliability of the manufactured boards. This includes incoming material inspection, in-process checks, and final functional testing. Establishing clear quality metrics and acceptance criteria helps maintain high standards throughout the production process.
Supply Chain Management
Inventory Management and Forecasting
Effective inventory management and forecasting are crucial for scaling up custom board design. This involves accurately predicting demand, managing lead times, and maintaining optimal stock levels. Collaborative planning with suppliers and manufacturers can help ensure a stable supply of components and minimise the risk of shortages.
Logistics and Shipping
Efficient logistics and shipping processes are essential for timely delivery of the manufactured boards. Consider factors such as packaging, transportation, and customs clearance when planning the supply chain. Partnering with reliable logistics providers and implementing tracking systems can help streamline the shipping process and ensure on-time delivery.
Continuous Improvement and Optimization
Scaling up custom board design is an ongoing process that requires continuous improvement and optimization. Regularly reviewing the design, manufacturing processes, and supply chain can identify opportunities for enhancement. Implementing lean manufacturing principles, such as value stream mapping and kaizen events, can help eliminate waste and improve efficiency.
Conclusion
Scaling up custom circuit board design from prototype to production is a complex process that requires careful planning, collaboration, and execution. By understanding the importance of custom board design, incorporating design considerations for manufacturing and assembly, and establishing effective collaboration and communication channels, businesses can successfully navigate the challenges of scaling up.
Investing in thorough testing and validation, selecting the right manufacturing partner, and implementing robust supply chain management practices are key factors in ensuring a smooth transition from concept to mass production. By following these strategies and continuously optimising the process, businesses can bring innovative electronic products to market efficiently and cost-effectively.
As the demand for custom circuit boards continues to grow in the realm of electronic product development, mastering the art of scaling up becomes increasingly important. By embracing the strategies outlined in this guide, businesses can unlock the full potential of custom board design and drive success in the competitive landscape of electronic product development.
Read More From Techbullion
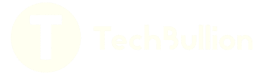