The evolution of industrial heating technologies has followed a fascinating path—from primitive open flames to complex magnetic fields. Today, induction heating stands at the forefront, offering unmatched precision, efficiency, and cleanliness. This article explores how induction heating is revolutionizing the industrial heating landscape, its technical foundations, and its real-world applications, while also examining the challenges and trends shaping its future.
1. Evolution of Industrial Heating: From Fire to Electromagnetism
Historically, industries relied heavily on combustion-based systems like coal furnaces, gas burners, and oil-fired heaters. These methods were not only inefficient but also posed safety and environmental hazards due to emissions and inconsistent heating.
As technology advanced, resistance heating became more common, offering more control but still suffering from slow response times and high energy consumption. The turning point came with the development of induction heating, a method that uses electromagnetic fields to generate heat directly within conductive materials. Originally developed in the early 20th century, induction heating has rapidly gained traction in the last few decades, especially with the rise of smart manufacturing and green technology initiatives.
2. How Induction Heating Works: Technical Insights and Core Advantages
Induction heating operates on the principle of electromagnetic induction. An alternating current passes through a coil, creating a magnetic field. When a conductive material (such as steel or copper) is placed within this field, electric currents—called eddy currents—are induced in the material, causing it to heat up due to its internal resistance.
Key Advantages of Induction Heating:
- Precision: Only the target material is heated, minimizing thermal distortion.
- Speed: Heating occurs rapidly, which increases throughput and reduces energy costs.
- Clean and Safe: No combustion, smoke, or open flame—making it ideal for cleanroom environments.
- Energy Efficiency: Up to 90% of the energy is converted directly into heat.
- Automation-Ready: Seamlessly integrates into automated and computer-controlled production lines.
For specialized needs, a high frequency induction heating machine is often used. These machines can deliver extremely localized heating, making them ideal for applications such as surface hardening and fine welding.
3. Real-World Success: Induction Heating Applications Across Industries
The versatility of induction heating makes it suitable for a broad range of industries. Some of the most prominent induction heating applications include:
Automotive Manufacturing
- Hardening of drive shafts, gears, and axles to improve durability.
- Brazing of fuel lines and air conditioning components for robust, leak-free joints.
Aerospace
- Heat treatment of turbine blades and landing gear components, where material integrity is critical.
- Precision brazing in engine and structural assemblies.
Metal Processing
- Billet heating for forging, offering uniform temperature and reduced scale formation.
- Pipe welding and coating, providing clean and strong bonds without contaminating the surface.
Electronics
- Bonding of heat-sensitive components, where non-contact heating is crucial.
- Soldering of high-performance electrical connectors, ensuring conductivity and durability.
4. Challenges and Future Outlook of Induction Heating
Despite its numerous advantages, induction heating also faces several challenges that need to be addressed for broader adoption:
Current Challenges:
- High Initial Investment: Equipment can be costly, especially for custom applications.
- Complexity in Design: Requires careful design of coils and systems tailored to each use case.
- Material Limitations: Only works with electrically conductive materials.
Future Trends:
- Integration with AI and IoT: Smarter induction systems will use data analytics for predictive maintenance and real-time process optimization.
- Portable Systems: Development of compact, mobile induction heating units for on-site repair and maintenance.
- Hybrid Heating Solutions: Combining induction with other methods (e.g., convection or laser heating) to expand its application range.
As the industrial world moves toward greener, more sustainable practices, the demand for clean, efficient, and controllable heating technologies will only grow. Induction heating is well-positioned to lead this transformation.
Conclusion
Induction heating has fundamentally changed how industries approach thermal processing. By moving away from traditional flame-based methods to the precision of magnetic fields, manufacturers gain greater control, efficiency, and environmental compliance. With continued innovation and expansion into emerging sectors, the future of induction heating is not just promising—it’s magnetic.
FAQs
- What is induction heating and how does it work?
Induction heating is a process that uses electromagnetic fields to heat electrically conductive materials without physical contact. An alternating current passes through a coil, generating a magnetic field. When a metal object is placed inside this field, eddy currents are induced in the metal, generating heat due to electrical resistance. - What are the advantages of using a high frequency induction heating machine?
A high frequency induction heating machine provides precise, localized heating with minimal thermal distortion. It is especially useful for applications requiring shallow heating depth, such as surface hardening, brazing, and fine soldering. These machines also offer fast processing times and improved energy efficiency. - In which industries are induction heating applications most common?
Induction heating applications are widespread in industries like automotive, aerospace, electronics, and metal processing. Common uses include hardening of engine parts, brazing of joints, melting and forging metals, and soldering delicate electronic components. - Are there limitations to using induction heating?
Yes, while induction heating is highly efficient and precise, it is limited to electrically conductive materials. Additionally, the initial cost of equipment and the need for custom coil design can be higher compared to traditional heating methods. - How does induction heating support sustainability goals in manufacturing?
Induction heating is a clean, flameless, and highly energy-efficient process. It produces no direct emissions, reduces energy waste, and enhances workplace safety—all of which align with sustainable manufacturing and green energy initiatives.
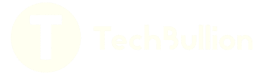