Forklifts are essential tools in many fields, like manufacturing and storage, making their reliability and performance directly affect how safe and productive things are during operations. Effective maintenance of the forklifts ensures forklifts work at optimum efficiency, which cuts down on downtime and long-term costs.
A structured plan and leveraging technological advancements are a must to find the best balance between operating efficiency and cost-effectiveness. This article delves into the most important parts of forklift maintenance and how it helps businesses run more sustainably. The Role of Forklift Maintenance in Operational Efficiency
Forklifts need to be properly maintained to operate at their best. Regular maintenance keeps machinery from breaking down, raises safety standards, and speeds up the efficiency of material handling. Forklifts that aren’t maintained regularly often break down, which adds to repair costs whilst also putting workers’ safety at risk.
Keeping forklifts in good shape results in less fuel usage, and enhanced operations, and also extends their operating lifespan. This helps cut operational costs by 25% through the machine’s lifespan1. Following repair schedules also ensures that you follow Occupational Safety and Health Administration (OSHA) rules, which lowers legal and financial risks.
Per, AllMachines, Forklifts can be categorized into multiple categories based on various factors. The Maintenance requirements also vary based on the Forklift types, however a set of practices are standard across all types and will be discussed in this article.
Types of Forklift Maintenance
Preventive Maintenance
Preventive maintenance aims to find and fix possible problems before they develop into larger issues. The tasks include lubrication, oil change, checking the tires, and evaluating the hydraulic systems. Preventive maintenance saves money and cuts down on unexpected breakdowns. Downtime can also be cut down significantly for businesses that follow a structured maintenance schedule2. Forklifts work well even under excessive work loads, if they get regular maintenance, preventing the output from being interrupted.
Predictive Maintenance
Predictive maintenance leverages data-driven insights and sensors to oversee equipment performance. It is possible to predict breakdowns before they happen by keeping an eye on tire wear, engine temperature, and battery health in real-time. Forklifts with Internet of Things (IoT) technology send alerts for important issues, so they can be fixed quickly. Predictive maintenance could prove to be very useful for fleets with high utilization rates. It is estimated that this may reduce overall maintenance expenses by as much as 20% and prolong the lifespan of the equipment.
Corrective Maintenance
Corrective maintenance involves the repair of forklifts following a breakdown or malfunction. Even though it’s sometimes unavoidable, unexpected downtime, higher repair costs, and possible interruptions to operations make it more expensive. Focusing on preventative and predictive maintenance instead of corrective maintenance is important for keeping operational costs down.
Cost Factors in Forklift Maintenance
Maintaining forklifts involves various costs, which can be categorized into direct and indirect expenses:
- Labor Costs: Skilled technicians are required for servicing and repairs, contributing to a significant portion of maintenance expenses.
- Spare Parts and Consumables: Items like filters, tires, and hydraulic oil must be replaced regularly. High-quality parts often have a higher upfront cost but provide better durability.
- Downtime Costs: Inoperable forklifts result in productivity losses, delayed operations, and potential financial penalties in logistics environments.
- Hidden Costs: Poorly maintained forklifts consume more fuel and have higher emissions, increasing operational costs and environmental impact.
A comparison of preventive vs. corrective maintenance reveals that investing in preventive measures reduces the likelihood of expensive repairs and minimizes downtime, leading to substantial long-term savings.
Strategies for Balancing Cost-Effectiveness and Efficiency
Implementing a Maintenance Schedule
Implementing a structured maintenance schedule guarantees prompt servicing and reliable performance. Service intervals recommended by the manufacturer serve as an outline for developing schedules that cater to particular operational requirements. Routine inspections help to stop small issues from developing into significant problems.
Training Operators
Operators are essential for ensuring the proper maintenance of forklifts. Effective training enables them to recognize early warning signs like unusual noises, fluid leaks, or performance drops. Furthermore, proficient operators reduce wear and tear by employing superior handling techniques.
Using Technology for Maintenance Management
Fleet management software makes maintenance more efficient by keeping an eye on service schedules, repair records, and cost trends. Forklifts that use IoT technology provide real-time insights into the engine’s condition, battery status, and the wear on the tires, which helps in planning for maintenance of the machine. A warehouse that employs IoT-integrated forklifts achieves a significant decrease in downtime through the use of real-time diagnostics.
Inventory Management for Spare Parts
Maintaining a sufficient inventory of spare parts reduces delays that may occur due to absent components during repair tasks. Too much of the inventory also has its disadvantages as it can tie up unnecessary capital. A properly prepared inventory management system ensures that the components of the machines are readily available and the finances remain stable.
Impact of Maintenance on Operational Efficiency
Proper maintenance directly impacts operational efficiency by extending the lifespan of equipment, enhancing safety, and reducing energy consumption. A well-maintained forklift fleet operates reliably, meeting the demands of dynamic environments like logistics and manufacturing.
Challenges in Forklift Maintenance
Proper forklift maintenance is important to ensure that operations run smoothly, but companies often have a hard time setting up and keeping up maintenance plans. If these problems are not dealt with promptly, they could affect safety, productivity, and how cost-effective the overall processes are.
Lack of Skilled Technicians
A notable challenge is the shortage of skilled technicians who can handle the complex tasks related to modern forklifts. The advent of advanced technologies such as IoT and AI in forklifts has led to a significant rise in the demand for specialized expertise. The difference is especially clear in remote or less industrialized regions, where the difficulty of reaching qualified service professionals poses a logistical challenge.
Inconsistent Servicing
Different maintenance methods may be used depending on operational stresses and tight schedules. Forklifts often have to work in tough conditions, so maintenance is put off to meet critical job demands. But inconsistent upkeep makes it more likely that equipment will break down when it’s least expected, which will lead to costly downtime. Adhering to strict maintenance schedules and following manufacturer guidelines can help avoid such disruptions.
High Upfront Costs for Predictive Maintenance Technologies
IoT devices and fleet management software are two main examples of predictive maintenance. These technologies have a lot of benefits, but they usually come with higher upfront costs and it might be hard for smaller businesses to justify this cost, even though they lower costs in the long-term. Businesses can use scalable and modular technology solutions to set up predictive maintenance while keeping costs low.
By acknowledging and addressing these issues, companies can establish a strong maintenance program that guarantees forklifts function effectively while maintaining cost control. Investing in technology, enhancing inventory practices, and focusing on operator training are proactive solutions that establish a sustainable framework for forklift maintenance.
Future Trends in Forklift Maintenance
AI-Powered Diagnostics
Artificial intelligence (AI) is changing the way forklifts are maintained by automatically finding problems and suggesting ways to fix them. AI-powered tools look at data from equipment to predict when repair will need to be done. This cuts down on unplanned downtime.
Autonomous Forklifts with Self-Diagnostic Capabilities
Autonomous forklifts that feature self-diagnostic systems are capable of independently detecting performance issues and alerting operators or service teams. This minimizes dependence on manual inspections.
Eco-Friendly Maintenance Practices
As sustainability concerns grow important, more eco-friendly methods are being used in forklift maintenance. Maintenance work has less of an effect on the environment when it uses recyclable parts, energy-efficient parts, and eco-friendly products.
Conclusion
Forklift maintenance is important for a smooth and efficient work process. Companies can find a balance between the maintenance costs and the efficiency of their operations by using organized maintenance schedules, modern technology, and trained operators. The use of advanced tools like IoT and AI tools makes things much more reliable and cuts down on downtime. Maintenance should be seen as an investment, not just a cost. This will help with long-term efficiency, safety, and finances.
References:
- https://www.forkliftacademy.com/cost-vs-benefit-the-roi-of-forklift-training-for-businesses/
- https://www.gminsights.com/industry-analysis/construction-equipment-fleet-management-software-market
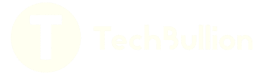