Flat tensile sample preparation is the first step in obtaining accurate and reliable tensile testing results. This process involves creating standardized specimens that reflect the material’s true mechanical properties, such as tensile strength, yield strength, and elongation. However, even minor errors in sample preparation can lead to significant discrepancies in test data, affecting product quality and compliance with industry standards.
Common mistakes, such as dimensional inaccuracies, rough surface finishes, and improper alignment during testing, not only compromise the integrity of results but also increase operational costs by requiring retests or causing equipment damage. These errors can ultimately impact quality control, research, and product development.
This article focuses on identifying the most frequent mistakes in flat tensile sample preparation and provides actionable strategies to avoid them. Taking steps to address these challenges, professionals can make certain that their tensile testing processes produce consistent, reliable, and accurate results.
Inaccurate Dimensional Machining
One of the most critical aspects of flat tensile sample preparation is machining the specimen to precise dimensions. Deviations from standardized specifications can lead to incorrect stress distribution during testing, resulting in unreliable mechanical properties measurements.
Common Mistake
Inaccurate dimensional machining often occurs due to outdated equipment, operator errors, or failure to follow standard guidelines. For example, uneven specimen widths or thicknesses can lead to stress concentrations that distort tensile strength readings.
Consequences
Dimensional inaccuracies compromise test results repeatability and reliability. Inconsistent specimen sizes can produce skewed data, making it challenging to compare results between different tests or verify compliance with standards such as ASTM E8 or ISO 6892.
Avoidance Strategies
Use Precision Equipment: The use of CNC milling machines or other precision tools specifically designed for tensile specimen preparation. These machines guarantee consistent and accurate cuts, minimizing manual errors.
Regular Calibration: Regularly calibrate machining equipment to maintain accuracy. Calibration helps detect and address tool performance deviations before they affect specimen dimensions.
Follow Standards: Follow standardized dimensions as outlined in testing protocols. Use templates or automated systems to confirm specimens meet required specifications before testing.
Poor Surface Finish and Edge Quality
The surface finish and edge quality of flat tensile samples are critical factors that directly impact tensile testing results reliability. Improper finishing can introduce stress concentrators or weaken the sample, leading to premature failure or inconsistent data.
Common Mistake
Poor surface finish is often caused by using inappropriate finishing tools or skipping essential polishing and deburring steps. Similarly, jagged edges or burrs left during machining can act as points of weakness, causing the sample to fail under stress prematurely.
Consequences
Rough surfaces and sharp edges create localized stress concentrations, leading to inaccurate measurements of tensile strength and elongation. These imperfections can also compromise test repeatability, making it difficult to draw meaningful comparisons or comply with testing standards.
Avoidance Strategies
Surface Finishing Techniques: Use grinding or polishing methods to achieve a smooth, uniform finish on the sample. This ensures consistent stress distribution during testing.
Deburring Tools: Carefully remove burrs and notches from edges using appropriate deburring tools. Rounded edges reduce stress concentration points.
Inspection Under Magnification: After finishing, inspect the sample under magnification to detect and correct any surface or edge imperfections that might impact the test.
Improper Alignment and Gripping
The way a flat tensile sample is aligned and gripped in the testing machine significantly influences the results accuracy. Misalignment or incorrect gripping can lead to uneven stress distribution, causing premature failure or skewed measurements.
Common Mistake
Samples that are misaligned during testing or gripped improperly often experience off-axis loading. This results in a non-uniform stress application, which invalidates the test and requires retesting. Additionally, using the wrong type of grip for the material or geometry can cause slippage or sample damage.
Consequences
Misalignment or improper gripping not only produces inaccurate results but also increases the likelihood of sample breakage, leading to wasted materials and time. It may also cause wear and tear on the testing equipment itself.
Avoidance Strategies
Careful Sample Alignment: Align the sample precisely within the testing grips, ensuring it is centered and parallel to the loading axis.
Appropriate Grips: Use grips designed for the material and sample geometry, such as serrated grips for soft plastics or flat grips for rigid metals, to prevent slippage or damage.
Regular Grip Maintenance: Inspect and maintain grips regularly to guarantee that they function correctly and provide consistent clamping force.
Ensuring Precision in Flat Tensile Sample Preparation
Tensile testing accuracy and reliability heavily depend on flat tensile sample preparation. Common mistakes such as dimensional inaccuracies, poor surface finishes, and improper alignment can compromise test results, leading to inconsistent data, wasted resources, and increased costs. Addressing these issues requires a proactive approach, combining precision machining, effective finishing techniques, and careful alignment practices.
Investing in high-quality tools, adhering to industry standards, and implementing regular equipment maintenance are key steps toward minimizing errors. Additionally, training personnel and enforcing standard operating procedures ensure consistency and compliance with all testing processes.
By understanding the importance of proper sample preparation and adopting best practices, organizations can achieve accurate, repeatable, and meaningful tensile testing results. In addition to supporting product quality and compliance, this also reinforces the trust in the testing process, thus contributing to overall operational success.
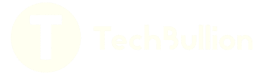