The food and beverage industry continually strives to enhance efficiency, better cater to customer preferences, and maintain a competitive edge in the market. A promising solution to these challenges lies in the integration of Customer Relationship Management (CRM) systems with Manufacturing Execution Systems (MES). Sharda Kumari’s recently published research study in the prestigious International Journal of Novel Research and Development investigates the potential benefits of merging these two systems. Her findings suggest that this integration could provide a holistic approach to decision-making processes, resulting in improved efficiency, deeper insights into consumer preferences, and a bolstered competitive position within the industry.
CRM systems play a crucial role in managing customer interactions and analyzing customer data, enabling manufacturers to gain insights into consumer preferences and market trends. MES, conversely, oversees production operations and delivers real-time insights into manufacturing processes. Combining the strengths of both systems allows manufacturers to make well-informed decisions regarding production schedules, resources, and product design, ultimately ensuring heightened customer satisfaction and loyalty.
In the realm of food and beverage manufacturing, the integration of CRM and MES systems can lead to various benefits, as highlighted in Sharda Kumari’s research paper. For instance, manufacturers can optimize their supply chain and logistics operations by predicting demand, streamlining inventory management, and reducing waste. These improvements result in cost savings and increased efficiency, which are essential in the highly competitive food and beverage industry. The integration of CRM and MES systems can enhance collaboration and communication between different departments within a food and beverage manufacturing organization. A unified source of customer and manufacturing data enables sales, marketing, production, and quality control teams to work more effectively together in developing and producing products that cater to customer needs. Integrating CRM and MES systems can assist food and beverage manufacturers in ensuring regulatory compliance. The industry is subject to strict regulations regarding food safety and quality, and a unified system combining customer feedback with manufacturing data allows manufacturers to swiftly identify and address any emerging issues. This proactive approach to quality control ensures compliance with industry regulations and helps maintain customer trust and brand reputation.
The research findings state that implementing CRM-driven optimization in MES for the food and beverage industry is a complex process and faces numerous challenges. Some of these challenges include ensuring that products meet customer requirements and preferences, and the limited research on computational models that combine CRM and MES data for decision-making purposes. The development of a computational model for CRM-driven optimization in food and beverage MES necessitates a deep understanding of the industry’s unique requirements and challenges. By incorporating advanced analytics and machine learning techniques, the computational model can process and analyze data from both CRM and MES systems, optimizing production scheduling, reducing waste, and improving overall manufacturing performance.
Sharda Kumari research underscores the potential of integrating CRM and MES systems in the food and beverage industry, offering numerous benefits such as enhanced efficiency, better alignment with customer preferences, and improved competitiveness. By overcoming implementation challenges and developing computational models that merge CRM and MES data, the food and beverage industry can unlock the full potential of CRM-driven optimization, leading to a more efficient and customer-centric industry.
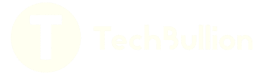