Relocating a factory is a significant undertaking that requires careful planning and precise execution. The process can involve numerous phases, each crucial for ensuring a smooth transition from one site to another. This article provides a detailed overview of a typical factory relocation timeline, offering insights into the essential steps involved and what businesses should expect throughout the process.
Phase 1: Initial Planning and Feasibility Study (3-6 Months)
The first stage of a factory relocation involves setting clear goals and evaluating the reasons behind the move. Whether it’s due to cost savings, a more strategic location, or improved infrastructure, this phase begins with an in-depth analysis. This often involves conducting a feasibility study that looks at the new location’s viability. Key factors considered in this phase include:
- Location Analysis: Assessing factors like proximity to suppliers, customers, labor availability, and transportation infrastructure.
- Cost Estimates: Estimating the total cost of the relocation, including moving expenses, new equipment, and renovations to the new site.
- Regulatory and Environmental Considerations: Ensuring that local laws, zoning regulations, and environmental policies are met in the new location.
- Risk Assessment: Identifying potential risks, such as supply chain disruptions, labor shortages, or unforeseen costs.
This phase typically takes 3 to 6 months and results in a detailed relocation plan, which includes a projected timeline, budget, and team assignment.
Phase 2: Site Selection and Preparation (3-6 Months)
Once the feasibility study confirms the move is practical, the next step is to finalize the new factory site and begin preparations for the physical move. This phase involves:
- Securing the New Location: Purchasing or leasing the new facility and ensuring all necessary permits are obtained.
- Design and Renovation: If the new factory requires modifications, the design team will create layouts to optimize the production flow, space utilization, and safety standards. Renovations may include electrical work, plumbing, or installing specialized equipment.
- Logistical Planning: Planning the logistics of the move itself, including how to transport machinery, raw materials, and finished goods with minimal disruption. This may involve choosing a professional moving company with expertise in industrial relocation.
The preparation phase typically lasts between 3 to 6 months, depending on the size of the facility and the complexity of renovations.
Phase 3: Equipment and Asset Relocation (2-4 Months)
The actual relocation of equipment, machinery, and inventory is one of the most critical stages of the timeline. This phase involves several key tasks:
- Inventory Management: Conducting a thorough inventory of all assets and categorizing them by priority. This helps ensure that essential equipment arrives first, minimizing downtime.
- Disassembly and Packing: Machinery and equipment are carefully disassembled, packed, and labeled to avoid damage during transport. Specialized packing methods are often required for sensitive or oversized items.
- Transportation and Setup: Transporting equipment to the new location is a delicate process, often requiring heavy-duty trucks or specialized vehicles. Upon arrival, the equipment is reassembled and tested to ensure it functions correctly.
This phase generally takes about 2 to 4 months, depending on the volume and complexity of the equipment involved.
Phase 4: Employee Transition and Training (1-3 Months)
Employee relocation and training is a crucial but often overlooked part of the factory move. Workers need to be informed and prepared for the changes. This phase typically includes:
- Employee Communication: Regular updates should be provided to employees throughout the process to reduce anxiety and ensure buy-in. If necessary, support is offered to workers relocating to the new site.
- Training: In the event of new equipment or systems being implemented at the new location, employees may need training to get up to speed. Proper training ensures that production resumes smoothly with minimal downtime.
- Workforce Recruitment: If the new location is in a different area, additional employees may need to be recruited to fill positions. This process requires careful planning and coordination with local recruitment agencies.
This phase generally takes between 1 to 3 months, depending on the number of employees and the scale of training required.
Phase 5: Final Commissioning and Testing (1-2 Months)
Before full-scale production can resume, the new factory needs to undergo commissioning and testing to ensure everything is operating smoothly. This includes:
- System Testing: This involves testing all machinery, production lines, safety systems, and IT infrastructure to ensure everything works as expected.
- Quality Control: Rigorous quality control checks are performed to ensure the product output meets the required standards.
- Trial Production Runs: Production is ramped up slowly with trial runs to identify any issues with processes, staffing, or equipment before going into full production.
This phase typically takes about 1 to 2 months, ensuring that all systems are functioning as intended and production capacity is fully restored.
Phase 6: Full-Scale Production and Operational Continuity (Ongoing)
Once the relocation process is complete, full-scale production can begin. However, it’s crucial to continue monitoring operations closely during the initial weeks and months to address any issues that may arise. Additionally, continuous communication with suppliers, customers, and employees will help maintain operational continuity and productivity.
A factory relocation is a complex, multi-phase process that requires careful planning and coordination. From initial feasibility studies and site selection to equipment relocation and employee transition, each step plays a crucial role in ensuring the success of the move. While the timeline can vary depending on the scale and complexity of the operation, the process generally spans from 12 to 24 months. By understanding the various stages involved and preparing adequately for each, companies can minimize disruption and ensure a smooth transition to their new facility.
Infographic provided by Equip Trucking & Warehousing, LLC, a provider of trucking services
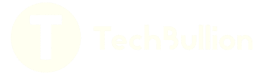