Face milling is a key milling operation of modern manufacturing. Whether you’re comparing face milling vs end milling or trying to improve your custom CNC milling projects, it’s important to understand face milling. This technique is widely used in custom metal milling and is known for its accuracy and smooth surface results.
In this article, you’ll find out how the face milling process works, the types of tools used, and how it is different from other milling methods.
Let’s dive in!
Face Milling
Face milling is a machining process used to get a smoother and flatter surface on workpieces. The goal is to remove material to give it a complete finish using rotating cutters. This process is typically done with a vertical or horizontal CNC milling machine.
Face Milling
The method is widely used on rectangular or square objects, such as metal blocks. Face milling is consistent with surface textures, as it delivers tight tolerances.
How the Face Milling Process Works
The face milling process utilizes multiple teeth that employ a rotating cutter. These inserts function as tools that spin directly into contact with the workpiece, removing thin layers from the top surface.
Firstly, the workpiece needs to be fixed firmly to the table to prevent it from slipping. The milling machine is perpendicularly positioned to the workpiece to cut it in radial and axial directions.
Next is the adjustment of the speed (spindle speed), feed rate, and cutting depth. This is done according to the material and project requirements.
However, custom CNC milling can automate the entire process by feeding the code into the computer. It ensures uniformity, reduces waste, and machines out the desired shape and form of the workpiece.
Tools Used in Face Milling
Milling bits
Many face milling tools are designed for specific applications.
Shell Mills
The most common tools include:
- Shell mills
- Fly cutters
- Indexable face mills
- Solid carbide face mills
All of these tools have a purpose. For example, fly cutters are suitable for softer metals. Whereas, carbide face mills are ideal with hard alloys. The selection of a proper tool directly affects the quality of the final surface. It also impacts the overall efficiency of the operation.
The factors influencing the tool performance include insert geometry, coating, and number of teeth. Selecting the best and right tool ensures longer tool life and better results for your custom metal milling project.
Benefits of Face Milling
Face milling offers advantages and disadvantages like any other procedure. You may improve the quality of your machining procedures by knowing their pros and cons.
Pros
- Face milling is the effective removal of material, which enables the quick processing of substantial amounts of material and greatly boosts production.
- It is appropriate for precision applications that demand tight tolerances and superior surface quality since it also offers high-grade finishes.
- Face milling is renowned for its adaptability as well because it can be used in a variety of industries and materials to meet a broad range of machining requirements.
Custom CNC milling makes it possible to maximise these advantages in a variety of sectors, all thanks to CNC technology.
Cons
- Tool wear is a serious disadvantage because constant usage can cause cutting tools to deteriorate significantly. Hence, frequent maintenance and replacement are required.
- Additionally, the intricate setup required to configure the fixtures and machines may necessitate exact alignment and trained operators, adding to the time and money required for preliminary preparations.
- When assessing face milling for particular machining applications, it is crucial to strike a balance between these factors.
Applications of Face Milling
Face milling is widely used in:
- Automotive part production
- Aerospace machining
- Mold making
- Industrial equipment manufacturing
Face milling tools help to achieve objectives such as flatness and surface accuracy with minimal error in all these areas. Hence, face milling is vital in product development for companies offering custom metal milling.
Face Milling vs End Milling
When you look at face milling and end milling, the main difference is how the cutting tool works with the material. In face milling, the flat part of the tool touches the workpiece. While in end milling, the cutting happens mainly on the sides of the tool.
End Mills
Secondly, face milling is excellent for making smooth, flat surfaces. End milling is better for making shapes, slots, and curved edges. Both methods have their uses, but face milling is usually the better choice when you need a good finish and a flat surface.
To learn more about this difference, check out this detailed guide on face milling vs end milling.
Why Choose Custom CNC Milling for Face Milling Tasks
The use of custom CNC milling in face milling helps make things more accurate and efficient. CNC machines can repeat the same steps over and over with high precision. By eliminating manual errors, they keep the same speed and cutting depth every time. Plus, CNC machines can work with different materials like brass, aluminum, and stainless steel. Creating an ideal situation for custom metal milling jobs.
Your parts meet the specification while working with skilled CNC machinists. If you’re thinking about using face milling for your project, it’s best to go with custom CNC milling services for the best results.
Final Thoughts
Face milling is a key part of fabrication and modern machining. Face milling tools are trusted for their reliability and precision in industries from aerospace to cars and industrial equipment.
Understanding the material, tool selection, and required finish is necessary before starting your next custom CNC milling job for success.
If you are looking for high-quality custom CNC milling services, check out the complete guide comparing face milling vs end milling.
FAQs about Face Milling
1. What is face milling, and how is it different from other milling types?
Face milling is a machining process that removes materials from the surface of a workpiece. It’s a different way of machining because it can cut from the face of the tool, not the sides.
2. What tools are best for face milling tasks?
Indexable cutters, shell mills, and fly cutters are the most common face milling tools. The choice of the right tool depends on the material and machine capability.
3. Can face milling be used in custom projects?
Yes. Face milling is great for custom metal projects that need flat surfaces and precise measurements. CNC machines make this process very flexible and efficient.
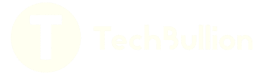