Silicon rubber is used widely in the industrial, medical devices, and electronics industries, because it is flexible, versatile, and tough. Silicone is used for a lot of applications. However, crafting designs with silicon rubber isn’t child’s play. It requires strict care about the material, how to mold and decorate. It is important to keep in mind what it is going to be used for. Additionally, pad printing machines are perfect for decorating odd, shaped silicone products.
Printing Techniques:
1. Pad Printing Machines: Pad printing machines are pretty good for marking and printing 3D shaped silicon rubber products. These machines use a specially made pad to pick up the ink from the plate to the rubber. The rubber pad ensures that prints are clear and precisely made.
Pad printing equipment is mostly used for printing and marking logos, labels, and info on medical devices, promotional products, and any other odd, shaped 3D item.
2. Screen Printing: This process includes the use of a mesh screen and a s squeegee to push ink on silicon rubber part. It is excellent for making special features and perfect for making excellent designs with different silicone inks. People use screen printing for flat, cylindrical, and cone shaped parts. Industries that use this printing method include drinkware, apparel, and industrial applications.
3. Inkjet Printing: Inkjet printing has made advancements in printing many applications. However, as of now, it is not possible to print on silicone rubber with UV inks. While inkjet printing can print full color with detailed designs, the fact that silicone is inert and has low energy level, it is not possible for UV ink to bond to silicone. It is important to note that only silicone-based ink will stick to silicone rubber.
Challenges in Printing on Silicon Rubber:
- Surface Characteristics: UV inks, solvent-based inks, and water-based inks do not stick to silicone rubber because of the low surface energy of silicone. For this reason, it is important to print silicon with silicone inks.
- Durability and Wear Resistance: Silicon rubber material can tolerate tough conditions and severe treatments like heat, chemicals, and rubbing. Printed designs need to last longer and should not fade or peel over time.
- Material Compatibility: The choice of ink should not be taken for granted—the quality and working of ink matter a lot. For instance, solvent-based inks and UV-curable inks will not bond to silicone. Therefore, it is important to use silicon-based inks. Only silicone-based inks work on silicone rubber.
- Curing Processes: Making sure the printed designs last long are a fundamental thing. To dry and cure silicone prints, you need heat. Thermal cure is the only option to dry the inks. Once the inks dry, they permanently bond to silicone rubber.
Applications of Printed Silicon Rubber Products:
- Medical Devices: Printing on silicon rubber is used widely in medical devices, such as to mark and give info on medical things like catheters and seals. Precise and strong prints are important for keeping track of medical tools.
- Consumer Electronics: Silicon rubber is used for things like phone cases and buttons. Printing enhances their looks and helps them handle daily use and different conditions more efficiently.
- Industrial Components: In factories, silicon rubber parts like seals and gaskets get printed with logos and info. The prints need to stay on, even in tough conditions, to keep things working well.
Conclusion:
Printing on silicon rubber is a mix of tech, knowing about materials, and good design. Learning these printing tricks is super important as industries keep making new and cool things. Making great prints on silicon rubber not only makes them look good but also helps them work well and last in lots of different situations.
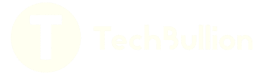