Walk-in coolers have become a cornerstone in industries ranging from food storage to pharmaceuticals, where precise temperature control and reliable cooling are essential. But what goes on behind those insulated doors? The technology behind walk-in coolers is both intricate and powerful, combining advancements in insulation, temperature regulation, and energy efficiency to keep perishable goods fresh, safe, and in prime condition. In this article, we dive into the high-tech components, mechanisms, and innovations that make modern commerical cooler doors efficient and indispensable in todayās commercial settings
Introduction
The science and technology behind commerical cooler doors allow these cold storage units to do much more than keep things cool. Through complex engineering and design, walk-in coolers manage precise temperature control, ensure consistent humidity levels, and operate with maximum energy efficiency. These cooling solutions are integral to grocery stores, restaurants, hospitals, and even scientific labs, where even slight temperature deviations can affect safety and quality. Understanding the advanced technology behind walk-in coolers helps businesses make informed decisions on selecting the best units for their needs and maintaining them for optimal performance.
Core Components of Walk-in Coolers
The primary components of any walk-in cooler include the compressor, condenser, evaporator, and fans. These parts work together to move refrigerant through the system, absorbing heat from the cooler’s interior and expelling it outside. Hereās how each component functions:
Compressors
The compressor serves as the “heart” of the cooling system, compressing the refrigerant gas and pushing it through the condenser coils. This process raises the refrigerant’s pressure and temperature, enabling it to release absorbed heat efficiently.
Condensers
commerical cooler doors down the high-temperature refrigerant from the compressor by dissipating the heat outside. Once cooled, the refrigerant returns to Ā liquid state, ready to continue circulating in the system.
Evaporators
The evaporator is located inside the walk-in cooler, where it absorbs heat from the air. This component lowers the temperature inside the cooler, keeping the interior at optimal storage conditions. High-quality evaporators also help manage humidity levels, which is essential for food preservation.
Fans
Fans ensure consistent airflow, preventing hot or cold spots and helping the evaporator absorb heat more effectively. Proper air circulation is essential for maintaining a uniform temperature throughout the cooler, enhancing efficiency and product preservation.
The Role of Insulation Technology
Insulation is at the core of every effective walk-in cooler, as it minimizes heat transfer and keeps the interior cold. The walls, ceiling, and floor of a walk-in cooler are lined with high-performance insulation materials that trap cold air and prevent outside heat from penetrating the cooler.
Types of Insulation Materials
The most common insulation material used in walk-in coolers is rigid foam, either polyurethane or polystyrene. These materials are chosen for their high R-value, or resistance to heat flow, which is essential for maintaining low temperatures with minimal energy use.
Thermal Resistance and Advanced Insulation
Some newer models of walk-in coolers feature advanced vacuum-insulated panels, which offer superior thermal resistance in thinner panels. These panels reduce the coolerās energy requirements while also allowing for a more compact design, ideal for smaller facilities.
Refrigeration and Temperature Control Systems
A walk-in coolerās ability to maintain consistent temperatures is made possible by sophisticated refrigeration and control systems. Temperature control is achieved through a thermostat that monitors the interior temperature and adjusts the cooling cycle accordingly.
Digital Thermostats and Temperature Precision
Digital thermostats provide precise temperature control, with some units offering accuracy within a single degree. This precision is essential for sensitive products, such as pharmaceuticals or delicate food items, where temperature fluctuations can compromise quality.
Adaptive Cooling Cycles
Many modern walk-in coolers are equipped with adaptive cooling cycles, which adjust the refrigeration cycle based on interior temperature and door activity. This feature helps prevent unnecessary cooling when the door is rarely opened, optimizing energy usage and prolonging the compressorās lifespan.
Humidity Control in Walk-in Coolers
Maintaining the right humidity level in a walk-in cooler is essential, particularly for food storage. High humidity can cause frost buildup, while low humidity can dry out fresh produce. Humidity control systems in high-tech coolers help maintain balanced humidity levels, preserving food quality and extending shelf life.
Smart Controls and Automation
Automation is a game-changer in walk-in cooler technology. With advancements in smart controls, users can now monitor and manage their walk-in coolers remotely. Here are some of the standout features:
Remote Monitoring
Smart control systems allow users to access temperature data, humidity levels, and door activity from a smartphone or computer. This capability is particularly valuable for facilities with multiple walk-in coolers, as it enables central management and immediate response to issues.
Data Logging and Reporting
Smart coolers come with built-in data logging systems, which record temperature and humidity data over time. This information is crucial for maintaining regulatory compliance in food and pharmaceutical industries, where records of temperature history are often required.
Energy Efficiency Innovations in Walk-in Coolers
With energy costs on the rise, energy efficiency has become a priority in walk-in cooler design. Many manufacturers are incorporating energy-saving features into their coolers to reduce operational costs and environmental impact.
Variable-Speed Compressors
Variable-speed compressors adjust their power output based on cooling demand, unlike traditional compressors that run at full power regardless of need. This innovation can save up to 30% in energy costs by reducing the workload during low-demand periods.
LED Lighting and Motion Sensors
Many walk-in coolers now use LED lighting, which consumes less energy and generates less heat than traditional lighting. Additionally, motion sensors can turn lights on only when someone enters the cooler, further conserving energy.
Improved Sealing Mechanisms
Advanced door seals and gaskets minimize air leakage, ensuring that cold air stays inside and warm air remains outside. This reduction in air exchange is crucial for maintaining interior temperatures and reducing the strain on cooling systems.
Eco-Friendly Refrigerants
As environmental regulations evolve, the use of eco-friendly refrigerants in walk-in coolers has become increasingly important. Many modern coolers now use low-GWP (Global Warming Potential) refrigerants, which reduce environmental impact while maintaining effective cooling performance.
Transition to Hydrofluoroolefins (HFOs)
Hydrofluoroolefins, or HFOs, are a newer class of refrigerants with lower GWP than traditional hydrofluorocarbons (HFCs). HFOs are gaining popularity due to their reduced environmental impact, making them a preferred choice in industries committed to sustainability.
Customizable Panels and Modular Designs
Modern walk-in coolers are highly customizable, allowing businesses to design cooling solutions tailored to their specific needs. Modular panels enable companies to expand or reconfigure their coolers as their requirements change, without needing to replace the entire unit.
Benefits of Modular Design
Modular panels are not only customizable but also easier to repair. If one panel is damaged, it can be replaced without affecting the entire structure. This flexibility makes modular walk-in coolers a cost-effective and practical option for many businesses.
Safety and Compliance Features
Walk-in coolers are also equipped with safety features that protect employees and meet regulatory standards. These include emergency release mechanisms, alarms, and safety lighting.
Emergency Release Mechanisms
In case someone becomes trapped inside, an emergency release handle allows them to exit the cooler safely. This feature is especially crucial in large walk-in coolers used in commercial or industrial settings.
Compliance with Health Standards
Walk-in coolers must meet certain standards to ensure the safe storage of food and pharmaceuticals. Safety alarms, temperature records, and data logging help businesses comply with these regulations by maintaining safe storage conditions at all times.
Future of Walk-in Cooler Technology
Looking ahead, we can expect walk-in coolers to become even more sophisticated. With advancements in artificial intelligence and the Internet of Things (IoT), future coolers will be able to self-diagnose issues, alert users to potential problems, and even adjust settings automatically based on usage patterns. This evolution in smart cooling technology promises to improve efficiency, safety, and sustainability across the cold storage industry.
Conclusion
The tech behind walk-in coolers has transformed them from basic cold storage units to sophisticated systems that optimize energy use, healthcare, and food industries. By leveraging advancements in insulation, energy-efficient components, smart controls, and eco-friendly refrigerants, todayās walk-in coolers are designed to provide precise temperature and humidity control, adapt to varying demands, and reduce energy consumption significantly
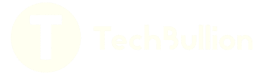