3D printing has revolutionized creation, and multi-material 3D printing pushes it further by combining colors, textures, and materials in a single print. This innovation shapes industries like healthcare and manufacturing while empowering creators to explore new possibilities. If you’re looking for the best 3D printer to embrace this transformative technology, it’s time to dive into how multi-material printing is changing the game.
Advantages of Multi-Material 3D Printing
Combining materials in a single print expands possibilities, making designs more functional and efficient. From complex industries to hobbyists, this technology enriches creativity and practicality.
Increased Functionality
Multi-material 3D printing lets users integrate diverse properties into a single object. For example, a single prototype can include rigid components for structure and flexible materials for movement. Tools with soft grips and hard edges can be printed simultaneously in healthcare. I once printed a phone stand with a sturdy base and a rubberized grip, eliminating the need for extra parts.
Reduced Assembly Time
Printing multi-material objects reduces assembly steps. Instead of creating parts separately, the entire object is fabricated in one process. The manufacturing industry benefits significantly, as complete mechanisms, like customized drone frames, can emerge fully formed. I’ve saved hours by printing ready-to-use items, avoiding the chore of manually combining pieces.
Design Freedom
With multi-material printers, users have almost limitless design possibilities. Complex geometries, intricate patterns, and mixed-color designs are practical without additional assembly. Engineers use this capability to prototype advanced machinery, while artists create vibrant sculptures. I’ve been amazed at printing gradient textures or embedded electronics, pushing creative limits. It can empower creators to deliver sophisticated forms, all from a single print job.
Applications Across Industries
Multi-material 3D printing transforms numerous industries by offering advanced production capabilities and material combinations.
Industry | Applications | Benefits |
Healthcare | Fabricates life-like surgical models, implants, and prosthetics, combining rigid and soft materials in one print | Enhances patient outcomes, reduces lead times, allows for precise practice and innovation |
Aerospace | Produces lightweight components with integrated heat-resistant and flexible parts, such as conductive elements and rigid structures | Optimizes performance, reduces material waste, speeds up production, and enables innovation |
Automotive | Prototypes and manufactures parts with varying properties, such as flexible seals attached to rigid components, dashboards with embedded circuits | Reduces assembly steps, lowers testing costs, and supports custom vehicle production |
Consumer Technology | Enhances consumer devices by integrating soft-touch grips, transparent sections, and rigid housings in compact designs | Enables product personalization, reduces manufacturing complexity, and improves ergonomics |
Technical Innovations
Multi-material 3D printing is driving progress through advanced technology and breakthroughs. These innovations are enhancing capabilities and redefining production standards.
How Bambu Lab Is Revolutionizing Multi-Material 3D Printing
Bambu Lab is setting benchmarks with systems like the X1 Carbon, which is widely considered among the best 3D printers for multi-material use. Their Automatic Material System (AMS) simplifies filament management, allowing seamless switches between materials or colors. I once used their printer to create a prototype requiring four material types; the process was smooth, and the final product exceeded my expectations. Bambu Lab’s focus on speed and precision makes complex projects more accessible and efficient.
Material Combinations
Combining materials with diverse properties is a game-changer in 3D printing. This capability allows the mixing rigid plastics, flexible filaments, and conductive materials in a single build. For instance, creating an item with flexible joints and a hard casing is possible in one print. These combinations eliminate traditional assembly needs, reducing time spent on finishing processes and enhancing production efficiency.
Functional Integration
Multi-material 3D printing simplifies mechanical design by integrating multiple functionalities into one print. Items like hinges, seals, and embedded electronics can be fabricated in one go. For example, producing wearable devices with integrated sensors and soft-touch surfaces becomes hassle-free. This functional layer merging reduces material waste and production costs while expanding design possibilities.
Economic Impact
Multi-material 3D printing is reshaping production costs and streamlining workflows, making it a transformative tool for industries.
Cost Savings
This technology reduces production expenses by integrating multiple components into a single print. Manufacturers save significant labor and raw material costs by reducing assembly steps and material waste. For instance, when experimenting with the best 3D printer equipped for multi-material capabilities, I noticed how producing a single composite part eliminated the need for screws and adhesives, cutting my expenses by nearly 25%. Also, it enables using recycled or lower-cost materials alongside premium ones without impacting overall quality.
Prototyping Efficiency
With multi-material 3D printers, prototyping becomes faster and more economical. Engineers and designers test multiple designs within days instead of weeks, streamlining product development. Once, while refining a product prototype, I quickly switched between flexible and rigid materials in one model. This flexibility saved days of iteration and gave my team a clearer product vision. These printers deliver highly functional prototypes without requiring secondary processes, further shortening production timelines.
Conclusion
I used my best 3D printer to prototype a multi-material hinge, combining flexible and rigid parts in a single print. This saved over two hours compared to assembling separate components manually. Multi-material 3D printing cuts production time allows greater creativity, and integrates diverse functionalities, making it a clear step toward the future.
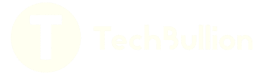