There are countless cutting technologies that the companies have been using. Waterjet cutting technology is a simpler and faster process of cutting. This process of cutting gives the most suitable cutting of a wide range of materials. A diamond or ruby nozzle fires high-pressure water into a mixing chamber. The water pressure creates a high vacuum and develops high garnet sand into the stream. The garnet sand is fired on the objects or materials to be cut. The sand particles cut the particles at high speed. This allows it to be the most versatile and powerful tool. A lot of industries have been using this tool for cutting throughout the world.
The waterjet cutter is the machine that is used for the perfect cutting of materials. It is made of three major components. These components are used for a high-pressure stream of water that makes a narrow line in the material. The cutting depends upon the thickness and the type of material. Some materials require more power for cutting.
Waterjet nozzle
The waterjet nozzle uses the configuration of mixing the chamber and the tube that allows the abrasive nozzle. This requires careful mixing with high water pressure. This results in the most efficient cutting. The cutting nozzles are tested and checked carefully. This ensures the right factory manufacturing. The majority of the companies have been using this technique to cut different materials.
Benefits of using waterjet cutting technology
You might be aware of the importance and benefits of using waterjet cutting. Waterjet cutting technology is quite beneficial, and it is the most flexible and versatile cutting technology that you can have. This cutting technology has great competition with saw and laser cutting technologies.
1. Superior quality cutting
It is to be mentioned that no cutting technology can match the level of cutting-edge technology that is made by using waterjet cutting technology. This technology gives burr-free and smooth edges. This is why the majority of the designers prefer waterjet cutting technology.
This technology uses the combination of abrasive flow rate, nozzle size, and water speed to cut the material. In the majority of the situations, waterjet technology reduces the requirements of secondary finishing. So you do not have to worry about the time. This technology gives the most superior cutting technology that helps to reduce effort, cost, and time.
2. Cost-effective and efficient
It would not be wrong to say that waterjet cutting technology has become the most effective and cost-effective solution available in the market. Waterjet cutting technology gives a cold cutting technology and procedure. However, there are some alternative hot cutting methods that can give unusual and inaccurate cutting. On the other hand, waterjet technology has a cold cutting process, and this is how you can have a cost-effective cutting experience.
Waterjet cutting technology also has a source of improving efficiency and brings time management. This technology requires a bit of secondary finishing, and edge treatment after the material is cut. Therefore, you can start managing your projects at a better speed.
3. Most accurate cuts
Waterjet cutting technology gives the most effective cutting to the manufacturers. Waterjet cutting technology gives a margin of 0.1 to 0.2mm when doing internal cuts. Logos, unique designs, custom patterns, and artwork are some things that are manufactured with the help of waterjet technology. This is how your business can give better customer service to your clients.
4. Thickness and material do not matter
You do not have to worry about the thickness and the type of material to cut when using waterjet cutting technology. Waterjet cutting technology is considered the most effective technology that cuts the majority of the available materials. You can cut steels having 25mm of thickness, composites, multilayer materials, and aluminum. Thus you can cut a wide range of materials, and you do not have to worry about the thickness of the material.
5. No heat zones
The manufacturers have to face a lot of issues while cutting these materials. Two most common issues, such as hardened edges and heat distortion, are the most common issues that the manufacturers have to face when cutting. Waterjet technology has proved to be an effective material. The heat zones have been created so that they can prove to be effective cutting technology. Workshops have been using this technology as it can eliminate the problems by choosing this technology.
6. No need to change the tools
Last but not least significant benefit of waterjet technology is that this is one of the most effective technologies. This technology allows people to cut a wide range of materials without changing the tools. There is no need to change the tools as they can cut a wide range of materials. You do not need to change the nozzle as well.
Range of materials cut by waterjet technology
A lot of people are quite interested in knowing the range of materials that the waterjet technology can cut. This has become one of the most popular technologies that can cut a wide range of materials. Therefore, a wide range of things can be cut with this technology. This technology has a great role in business, industry, and production lines.
Waterjet technology is famous for cutting, making holes in taps, cutting sinks, and making edges. This technology has proved to be a single solution to all kitchen problems. This is one of the most efficient technologies that reduce the risks of burnt edges, heat zones, dust emissions, and inaccurate cuts. This technology ensures the right manufacturing of benchtops in the first attempt. This technology can cut the whole range of products, such as granite, marble, porcelain, and engineered stones.
The bottom line
It is to be mentioned that waterjet cutting has proved to be the safest and the most versatile process available in the market. This process is capable of cutting wider and thicker materials. Moreover, this is a safe cutting for the environment, and a lot of industries have been using this technology.
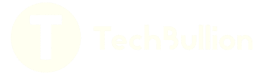