What Are Pogo Pins?
Pogo pins, also called spring-loaded pins, are electrical connectors that ensure stable connections. These small but essential components are widely used due to their durability and efficiency. Their unique design allows consistent electrical contact under frequent use. This makes them ideal for devices requiring repeated connections.
Each pogo pin has a cylindrical barrel housing a spring for smooth compression. This design reduces wear, ensuring long-lasting performance in various applications. Their versatility makes them useful in consumer electronics and medical devices. As a result, they play a crucial role in modern technology.
How Pogo Pins Work?
Pogo pins work through a simple yet efficient mechanism that ensures reliable connectivity. When a pogo pin is pressed against a mating surface, the internal spring compresses to maintain constant contact. This design helps accommodate slight misalignments and surface variations. As a result, pogo pins are ideal for high-frequency connections in electronics.
A gold-plated finish enhances conductivity and prevents oxidation, extending the pin’s lifespan. This coating ensures minimal resistance, improving overall electrical performance. The durable construction allows pogo pins to withstand repeated use without degradation. Their reliability makes them essential in various electronic applications.
Common Applications
Below are common applications for pogo pins across various industries, highlighting their versatility and reliability.
1. Consumer Electronics
Pogo pins are widely used in smartphones, tablets, and smartwatches for efficient connectivity. They enable wireless charging, data transfer, and docking with high reliability. Their compact design allows seamless integration into modern devices. This makes them essential for convenient and durable connections.
2. Medical Devices
Medical equipment relies on pogo pins for stable electrical connections in various applications. They are found in patient monitors, health trackers, and diagnostic tools. Their durability ensures consistent performance in critical medical settings. This makes them ideal for long-term, high-precision use.
3. Automotive Industry
Pogo pins play a vital role in automotive electronic systems and battery management. They are used in ECUs, infotainment systems, and safety components. Their resilience against vibrations and temperature shifts ensures reliability. This allows them to support uninterrupted vehicle operations effectively.
4. Industrial Equipment
Pogo pins enable secure connections in robotics, automation, and industrial machinery. They withstand high-cycle applications that require frequent connections. Their durability makes them perfect for demanding production environments. This ensures smooth performance in various industrial processes.
Types of Pogo Pins
Pogo pins come in various types, each designed for distinct functions and industries.
1. Standard Pogo Pins
These pogo pins have a simple structure with a spring-loaded plunger inside a barrel. They are the most commonly used type in electronic devices for reliable connections. Their durability and efficiency make them ideal for general-purpose applications. From smartphones to industrial equipment, they play a crucial role in connectivity.
2. High-Current Pogo Pins
High-current pogo pins are designed to handle larger electrical loads with minimal resistance. They use reinforced structures and low-resistance materials for stable power transfer. These pins are essential in applications like battery charging and power transmission. Their durability ensures long-lasting performance in high-power environments.
3. Coaxial Pogo Pins
Coaxial pogo pins are used in RF applications where signal integrity is essential. Their specialized design reduces interference and ensures stable high-frequency transmissions. These pins are widely used in communication systems, antennas, and testing equipment. Their ability to maintain clear signals makes them crucial in precision electronics.
4. Custom Pogo Pins
Custom pogo pins are designed to meet specific requirements in various industries. They can be modified in terms of length, shape, material, and electrical properties. Manufacturers create these pins to optimize performance for specialized applications. Their adaptability makes them valuable for unique electronic designs and prototypes.
Manufacturing Process
The manufacturing process of pogo pins involves several precise steps to ensure durability, reliability, and optimal performance.
1. Material Selection
The first step in manufacturing pogo pins is choosing high-quality materials. Brass, stainless steel, and beryllium copper are commonly used. These materials provide excellent strength, durability, and conductivity. Proper selection ensures reliable performance in electronic applications.
2. Precision Machining
The barrels and plungers of pogo pins are precisely machined for accuracy. CNC machining and stamping techniques help achieve tight tolerances. This ensures smooth operation and consistent electrical contact. Proper machining is essential for long-lasting and efficient performance.
3. Spring Assembly
A carefully designed spring mechanism is assembled inside each pogo pin. The spring provides the necessary compression for stable connectivity. Material and design selection impact lifespan and performance. A well-constructed spring ensures durability in frequent-use applications.
4. Plating Process
Gold or nickel plating is applied to improve conductivity and prevent corrosion. Gold is preferred for its superior oxidation resistance and low resistance. This plating enhances the overall performance of the pogo pin. A high-quality finish ensures long-term reliability in various environments.
5. Quality Testing
Pogo pins undergo rigorous testing before being shipped to customers. Tests include electrical conductivity, durability, and mechanical stress assessments. These quality checks ensure compliance with industry standards. Only well-tested pogo pins are used in high-performance applications.
Factors for Reliability
Several key factors determine the reliability of pogo pins, ensuring consistent performance and durability in various applications.
1. Material Quality
The reliability of a pogo pin heavily depends on the materials used. High-grade metals such as brass and beryllium copper ensure strength. Premium coatings like gold plating enhance conductivity and longevity. Proper material selection is crucial for optimal performance.
2. Spring Force
The internal spring must provide consistent force for a stable connection. Too much pressure can damage mating surfaces and reduce lifespan. Insufficient force may lead to weak or unstable electrical contact. A well-balanced spring ensures reliability and durability.
3. Contact Resistance
Low contact resistance is essential for efficient electrical conductivity. High resistance can cause signal loss, overheating, and energy inefficiency. Proper plating and material selection help maintain minimal resistance. Reliable pogo pins ensure smooth and uninterrupted power transmission.
4. Corrosion Resistance
Pogo pins must withstand humidity, oxidation, and environmental exposure. Gold plating significantly improves resistance against rust and degradation. Nickel and other coatings may offer additional protection in harsh conditions. Proper surface treatment extends the lifespan of pogo pins.
5. Mechanical Durability
A high-quality pogo pin should withstand thousands of compression cycles. Frequent use should not cause wear or impact performance. Strong materials and precision engineering contribute to long-term reliability. Durable pogo pins ensure consistent electrical connections over time.
6. Operating Temperature Range
Pogo pins must function efficiently in extreme temperatures. Automotive and industrial environments require stability under harsh conditions. High-quality materials and coatings help maintain performance. Reliable pogo pins operate seamlessly across various temperature ranges.
Innovations in Pogo Pin
Recent advancements in pogo pin technology have introduced magnetic pogo pins. These integrate magnets to provide more secure and effortless connections. This innovation enhances stability, especially in high-vibration environments. Magnetic pogo pins are becoming popular in consumer electronics and medical devices.
Another key development is the rise of multi-pin pogo connectors. These components offer multiple connection points in a single unit, increasing functionality. Improved plating techniques and high-performance alloys further enhance the durability of pogo pin connectors. These advancements make pogo pins more efficient and reliable across various industries.
Future of Pogo Pins
As technology advances, pogo pins will become even more efficient and versatile. The growing demand for compact and high-performance connectors is driving innovation. Wearables, IoT devices, and electric vehicles rely on improved connectivity solutions. Pogo pins will continue to evolve to meet these industry needs.
Emerging trends include flexible pogo pins for adaptable and dynamic connections. The use of environmentally friendly materials aims to reduce electronic waste. Continuous improvements in precision engineering will enhance reliability and durability. Pogo pins will remain essential in modern electronic applications for years to come.
Final Thoughts
Pogo pins are essential components in the electronics industry, offering reliable and high-performance connections. Their spring-loaded design ensures durability, efficiency, and adaptability in various applications. These pins are widely used in consumer electronics, medical devices, and automotive systems. Their ability to maintain stable connections makes them invaluable in modern technology.
As materials and manufacturing techniques advance, pogo pins will play an even greater role in connectivity. Improved designs will enhance their efficiency, lifespan, and versatility across industries. Understanding their functionality, types, and reliability factors is crucial for engineers and designers. With continuous innovation, pogo pins will remain a key element in future electronic developments.
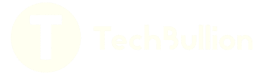