Many industries make use of variety of hardware equipment and tools in their daily operation. Industries such as construction, aviation and manufacturing make use of lifting equipment like forklifts, cranes and hooks. Operating with the right equipment increases total yield, saves time and reduces the cost of operation. However, these equipment have to be properly maintained to keep them functioning. You will need a third party quality inspection company, such as EC global inspection.
Importance of Quality Inspection for Hardware and Tools
No sudden breakdown
Carrying out regular quality inspection keeps your tools from sudden breakdown that may lead to hours or days of total unproductivity which would also increase the expense incurred by the organization. These unproductive hours may adversely affect the chain of supply and put the entire business at great risk.
It Reduces Expenses
Taking out money to carry out regular quality inspection may seem difficult or wasteful, however, you are spending less to avoid spending more on repair or purchase in the long run. More importantly, repairing equipment at the early stages of defect is much more cheaper that cases where the defect has affected other parts of the equipment
Workplace Safety
Perhaps one of the most dreaded occurrence aside sudden breakdown of equipment is fatal incidents in the workplace. Aside protecting the workers from fatal injuries, regular inspection prevents diverting funds into lawsuit and compensation for injured workers. Regular inspection will reveal defects that may become life threatening and cause damage. Carrying out quality check allows workers to go about their duties in a safe workplace.
Increased Productivity
Quality inspection also ensures that your equipment operate at full capacity. This results in optimal productivity for your business. Once defects are identified and repaired early, your tools and equipment will be kept in prime condition. As such your equipment brings great yield for a long time.
Common Issues that Arise in Hardware and Tools Manufacturing
Equipment Tracking
Equipment management is one of the most common challenges of maintenance. When pieces of equipment are moved from one location to another, chances of theft and misplacement are increased. This will inevitably affect daily operation and output. To avoid this, it is important to track equipment and keep them in safe locations.
Improper Operation
Typically, equipment operators are people who have been trained extensively on the operating procedures of a machine, rudimentary troubleshooting and how to safely operate a particular equipment. In some situations however, operators may be required to operate a machine they haven’t been trained to operate.
This situation arises due to shortage of staff, unexpected absence and cases of emergency. The best solution is to have a number of operators who are trained on how to operate a number of machines in the factory. If possible, however, all operators should have basic operational knowledge on each of the tools and equipment used in the factory.
Also, there should be a standing rule that prevents an operator from running an equipment he is in no wise qualified to operate. This will eliminate errors and damage that usually result from inadequate training. This is also in line with the stipulations of the Occupational Safety and Health Administration (OSHA).
Failure to Carry out Regular Maintenance
Most factory equipment need to be regularly maintained to keep them at optimum performance. The mistake most factory managers make is to substitute regular maintenance with eventual repairs. They neglect little defects until it worsens to a point where repair becomes absolutely necessary.
Some companies hold the wrong assumption that experienced workers will spot defects before the equipment breaks down totally. Without deliberate regular maintenance, defects might go unnoticed for a long time until it becomes aggravated.
Lack of Spare Parts
Quality maintenance planning is not complete without availability of spare parts. As such, you should ensure the availability of spare parts for parts of the equipment that are most susceptible to wear and tear. It is not advisable to wait until these parts become defective. Instead, order them early and store them until they are needed.
Understandably, it is not practical to buy spare parts for all the parts of every machine, however, you can set up regular maintenance for some parts of the equipment to ensure durability.
Tips for Conducting Effective Inspections
Follow Defined Procedure
Outlining a defined procedure helps to ensure that every one sticks to the plan and that every inspection is carried out the same way throughout the organization. State the goals of the exercise and choose the appropriate methods. The team must be trained to follow laid down procedures.
When workers do not have a defined procedure, they go about it the way they think best. If this continues, records and reports become inconsistent and create confusion for anyone trying to make sense of them. As well, procedures should be depict in a form everyone understands.
Provide Effective Training
There’s no other way to ensure effective inspections than to provide regular, quality training. The training should be carried out in a formal setting to ensure proper comprehension. The workers should also be retrained as these issues keep coming up.
Staff Accountability
Holding employees accountable is also a good way to ensure proper and thorough inspection. Therefore, both exceptional and poor performance should be documented to track improvement. Determine both individual and team goals to promote personal and shared accountability. Goals can also be used to measure progress.
Use Technology
Provide employees with the right hardware and software to manage, and report regular inspections. This may include mobile devices such as tablets, smartphones.
Conclusion
While having your own workers carry out inspections is a lot cheaper, you may want to consider a third party company with experts who are knowledgeable about industrial equipment. They are in a much better position to spot defects that may not be obvious to others. They can also determine the extent of the damage and state which defect should be prioritized over others.
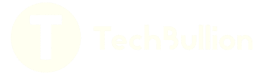