Gas cylinders are containers used to store gases at pressures higher than atmospheric pressure. Highly durable materials, such as steel or aluminum, are utilized in their construction to ensure they can safely contain gases like oxygen, nitrogen, helium, and various hydrocarbon fuels. These cylinders are ubiquitous in industrial, medical, and domestic environments, playing a crucial role in operations ranging from welding and manufacturing to providing life-supporting oxygen in healthcare settings.
The design of a gas cylinder is a critical aspect of its safety and functionality. They are engineered with a combination of strength, durability, and corrosion resistance in mind, and are subject to rigorous testing and certification processes. Valves, pressure regulators, and other safety devices are integral components of gas cylinders, ensuring controlled and safe release of the gas when used.
Safety standards and regulations governing the storage and handling of gas cylinders are strict due to the potential hazards associated with high-pressure gas containment. Users must be trained to handle, transport, and store these cylinders properly to prevent accidents. Regular inspections and maintenance are mandatory to detect any signs of wear, corrosion, or damage that could compromise the cylinder’s integrity, ensuring they continue to be operated within the bounds of safety guidelines.
Types of Gas Cylinders
Gas cylinders come in various types, each designed to hold specific gases under different conditions. The choice depends on the intended use, the required pressure, the volume of gas needed, and the chemical properties of the gas.
High-Pressure Cylinders: Typically made of steel or aluminum, they store gases like oxygen, nitrogen, argon, and hydrogen. These cylinders can withstand pressures up to 3000 psi (pounds per square inch).
Low-Pressure Cylinders: Usually made of composite materials such as fiberglass, they’re used for gases that don’t require high pressure, like acetylene.
Liquid Cylinders: Designed to hold liquefied gases such as liquid nitrogen, oxygen, or carbon dioxide, these cylinders maintain their contents in liquid form at very low temperatures.
Acetylene Cylinders: Contain a porous material soaked in acetone, within which acetylene is dissolved under pressure. They are unique due to acetylene’s properties which require it to be stored in a solution to prevent decomposition under pressure.
Propane Cylinders: Commonly used for heating and cooking, these can vary in size from small handheld canisters to large tanks.
Speciality Gas Cylinders: These are made to contain gases used in medical, food, or scientific applications, requiring specific materials or valve types to maintain gas purity and integrity. Each type is equipped with valves and regulators appropriate to the gas’s properties and the cylinder’s intended use. Safety standards and handling procedures vary depending on cylinder type and contents.
Safety and Handling Procedures
Handling gas cylinders requires strict adherence to safety standards to prevent accidents and injuries. Appropriate storage, transportation, and usage protocols are pivotal for maintaining a safe environment.
Storage Guidelines
Gas cylinders must be stored in a well-ventilated area away from direct sunlight, heat sources, and inclement weather. They should be secured in an upright position to prevent tipping and ensure valve protection.
- Ventilation: Store in a dry, cool place with adequate airflow.
- Positioning: Secure cylinders upright with chains or straps.
- Separation: Segregate full cylinders from empty ones.
Transportation Best Practices
The transportation of gas cylinders, whether by vehicle or manually, requires careful handling to avoid accidents.
- Stability: Ensure cylinders are well-secured during transit.
- Orientation: Transport cylinders upright whenever possible.
- Inspection: Regularly check for leaks or damage prior to transportation.
Usage Protocols
Before using a gas cylinder, individuals need to inspect it for any signs of wear or damage, and ensure that the gas type is appropriate for the intended use.
- Connections: Tighten all fittings securely to prevent leaks.
- Monitor: Use pressure gauges to track cylinder content levels.
- Safety Equipment: Wear appropriate personal protective equipment (PPE).
Regulatory Standards
Regulatory standards are essential to ensure the safety and reliability of gas cylinders. These regulations cover a wide range of criteria, including material selection, design, construction, and performance requirements.
Inspection Requirements
Inspection processes for gas cylinders are instituted to guarantee that they meet specific safety standards before and after entering service. They involve:
- Visual Examinations: Cylinders are consistently checked for dents, corrosion, and other surface damages that might compromise integrity.
- Pressure Tests: Hydrostatic or pneumatic testing is performed to confirm that cylinders can safely handle the designated pressure levels.
Certification Processes
Certification of gas cylinders is an extensive procedure involving several key steps:
- Material Traceability: Manufacturers must use certified materials and maintain records of their origin and specifications.
- Manufacturing Oversight: Production must follow predefined protocols, and cylinders are often serialized for traceability.
- Third-Party Verification: Certifying bodies conduct independent audits to validate that the cylinders comply with all applicable standards and regulations.
Gas Cylinder Specifications
Understanding the makeup and capabilities of gas cylinders ensures safe and appropriate usage. Specific materials, pressure ratings, and valve types are tailored to contain and deliver gases for a myriad of applications.
Material Composition
Gas cylinders are commonly crafted from high-strength steel or aluminum. Manufacturers may use composite materials like carbon fiber for enhanced strength-to-weight ratio.
Pressure Ratings
Cylinders must withstand the internal pressures exerted by the contained gas. They are usually rated in psi (pounds per square inch) or bar. Ratings can range from 300 psi to over 2,500 psi for standard models, with specialized cylinders exceeding these figures.
Valve Types
Valves are the mechanisms that control the release of gas from the cylinder. Common types include:
- CGA Valves: Denotes Compressed Gas Association standards, with specific designs for different gases.
- Pin Index Safety System (PISS): Prevents misconnection of gas-specific cylinders to equipment.
- Quarter Turn Valves: Require a 90-degree turn to open or close, providing quick access to the gas supply.
Applications and Uses
Gas cylinders are essential across various sectors for storage and transport of gases. They are especially critical in applications that require reliability and safety.
Industrial
In the industrial sector, gas cylinders contain oxygen for metal cutting and welding processes. They also store carbon dioxide for carbonation in beverage manufacturing and nitrogen for creating inert atmospheres during chemical processing.
Medical
Medical facilities utilize gas cylinders to supply oxygen to patients with respiratory issues. Nitrous oxide, often used for anesthesia, and medical air, used for patient ventilation, are also stored in cylinders.
Scientific Research
Researchers rely on gas cylinders for experiments that need specific atmospheric conditions. They store gases like argon for preserving tissue samples, and helium for gas chromatography, which requires a pure and stable gas source.
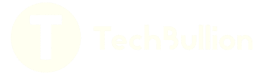