Expert analysis by Alexey Bochkarev, Software Engineering Manager
Think back to a time when you had a stalwart person, place, or thing in your life.
This could have been, for example, a favourite, all-weather vehicle that never broke down and always helped you to arrive from point A to B. Perhaps it was a piece of assembly furniture in your kitchen or a favourite app on your smartphone. The list goes on.
Wherever the object, reliability was arguably its most important quality. No matter how impressive the functionality, or flashy and attractive the appearance, no object can last in this world without rock-solid reliability. Without it, relationships would fail. Watches would stop moving. Friends, family, and colleagues would never be there in your time of need.
Now, let’s apply this to the world of production, where the quality of your products becomes a testament to your name brand and tantamount to your business’s success.
It is the ultimate stress test for a company’s long-term viability, notwithstanding other metrics like customer reviews and feedback, performance evaluations, and customer service.
5 Reliability KPIs
According to the American Society for Quality, Reliability is defined by 5 key performance indicators:
- Availability to perform a function: how well an object or feature performs an intended operation like heating, driving, cutting, computing, baking, or even AI-based tasks;
- Dependability: the rate of reliability while operating an object or executing a process. How often does an AI model deliver a correct answer? Does an operating system frequently crash or encounter security breaches?
- Durability: how durable physical products last, or how well they function before becoming obsolete after repeated use. For example, tyres wear down over time. Camping gear can tear, snap, or break. Planned obsolescence, where manufacturers break down components over an intended period, can affect car parts or light bulbs.
- Probability of success: the likelihood that the product will succeed in a market, or that an operation will execute properly. Will your project management scheme deliver a specific product to an ideal time-to-market, or will you face delays? Can your solution boost return on investment (ROI) for buyers?
- Quality over time: how well an item or process performs over time due to wear, tear, or obsolescence, whether planned or through competition.
Instilling Confidence via Consistency
After establishing a level of reliability in a project or product, reliability can offer customers, clients, and even colleagues greater confidence in what they are producing.
For instance, Project Management World outlined several benefits to reliable products:
- Reliability can foster customer loyalty and satisfaction, where they continue to buy products due to their reputation or promote them by word of mouth.
- Establishing product reliability can help brands build a positive reputation by building rapport with customers and clients, leading to greater sales and market shares.
- Reliability helps to reduce costs associated with maintaining and supporting products in the long term. Product recalls can accrue significant costs, leading to sales disruptions and warranty issues, and minimising these can save billions.
- Instilling product and process reliability provides a competitive edge over rival firms in the marketplace, allowing businesses to stand out from the crowd with their perceived commitment to manufacturing a quality product.
- Improving product and service reliability can also provide companies with an effective hedge against risk factors such as safety, legal, product, and reputational concerns.
- Finally, reliability builds positive user experiences for clients, leading to more brand and product trust for goods and services.
The Conundrum of Product Latency
A major obstacle to product reliability, either through engineering, performance, or operational, is measuring and tackling latency. This is the time it takes from receiving a request to resolving the concern.
Whilst some organisations may accept batch requests and resolve them based on sheer volume (for example, software company approaches to resolving bugs), firms must realistically determine the metrics needed to provide quality, reliable service.
Data-driven approaches can include the following:
- How well does your company handle requests
- The security of its data to prevent breaches
- Where problems originate and how rapidly they are resolved
- Using AI to predict future concerns with future prototypes and simulating past, current, and future reliability scenarios with industrial metaverse platforms
Companies should aim to reduce product recall times, tackle complaints and processing times, and provide timely updates up the chain of command. Without operating as a ‘well-oiled machine,’ companies can turn small problems into massive ones in a short time.
However, by prioritising product improvements over latency, companies can avoid severe disruptions and ensure sales revenue continuity.
One major stress test for this was the global COVID-19 pandemic, which saw business operations grind to a halt and called for huge infrastructural revamps to reduce disruptions and latency, as well as service customers.
By leveraging tools like remote guidance, Zoom and Teams, immersive collaborative platforms, and others, companies saved money, time, and headaches in their supply chains by striking a better, more conducive balance between the two without physical involvement.
Case Studies in Reliability
With the power of technology, companies are demonstrating the efficacy of new solutions capable of elevating reliability, standards, and operational efficiency in manufacturing, construction, quality assurance, and even niche services.
In one case study, Hewlett-Packard tapped Microsoft’s long-running immersive headset, the HoloLens 2, to resolve issues with massive industrial printing machines.
By allowing customers to connect with remote advisors, Microsoft empowered HP to tackle printing issues with impressive resolution times, eliminating long service calls, speeding up troubleshooting processes, and minimising printer downtimes.
Offering HP end-users VoIP meetings via the HoloLens 2, training and upskilling workers and clients for operating printers, and engaging them with walkthroughs virtually, HP and Microsoft have also shifted the paradigm for instilling reliability through customer service.
In another study in December 2023, featuring an Australian coal mining facility, Total Resource Management tested methods to improve reliability among production output figures while “keeping fixed cost unchanged.”
Through an audit, the company found that the mine had scored just 30 compared to other firms with record marks of 75, indicating major bottlenecks for the mine’s “continuous miners (CMs).” A significant cause was high downtime rates of up to 88 minutes per shift.
Other metrics included no coordinated production schedule and maintenance schedules, leading to greater capital-based downtimes. Shear shafts also continuously broke after just 1.5 days on average, causing 15 minutes of downtime per break.
After launching an improvement plan, based on the initial assessment, the mine cut its average downtime from 82 to 16 minutes and 88 to 35 minutes for development CMs and extraction CMs, respectively.
The upward trend in output reliability led to an increase in capital valued at $34.9m AUD a year. Improvements in efficiency, equipment downtime, and other serious issues were mitigated, prompting the company to assign planner positions after consultations.
Conclusions
Reliability is one of the cornerstones of the business world, and everything — even research, engineering, services, and even fast food — depends on this to deliver quality products.
Teetering between latency and product reliability is a tricky balance to strike, but executives can determine how to do so using cutting-edge tools along with tried-and-tested measures.
Although the customer is always right, they always come back due to this key ingredient.
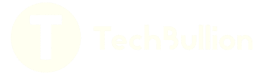