In the rapidly growing plastic industry, verifying the product’s quality and safety relative to international benchmarks is crucial. Among the numerous applications of plastics, plastic piping systems are of utmost importance because they are extensively used in the distribution of water, gas, sewage systems, and various industrial plants. Because these systems are subjected to harsh environments, physical stress, and chemical exposure, pipe testing equipment are essential to guarantee the strength, durability, and performance of plastic pipes.
This article explores the key types of pipe testing equipment used in the plastic industry, their functions, and their importance in maintaining product quality and regulatory compliance.
The Importance of Pipe Testing in the Plastic Industry
In general, plastic rather than metal is used for weight, corrosion resistance, and economy. But their accuracy depends heavily on careful manufacturing and extensive testing. What can you measure with pipe testing equipment? Pipe testing tools allow manufacturers to measure:
- Mechanical strength
- Resistance to slow crack growth
- UV stability and carbon black content
- Opacity and visual consistency
- Dimensional accuracy
Each of these attributes is vital to ensure the long-term performance of plastic pipes in real-world environments.
Key Pipe Testing Instruments and Their Functions
Over the years, numerous dedicated tools have been designed to measure specific parameters of plastic pipes. Utilizing some of the best-known testing gear, Testron Group has a complete lineup for all major kinds of tests in pipemaking.
Here are a few of the most commonly used testing instruments:
1. Pipe Notch Milling Machine
One such key piece of equipment in the area of slow crack growth resistance testing is the pipe notch milling machine. It is used to machine a notch in the wall of a pipe-shaped specimen for subsequent testing for crack propagation under stress.
Key Features:
- Intended to groove plastic pipes 63 mm to 630 mm in diameter.
- With a V-shaped carbide cutter rotating at ~700 rpm.
- Enables the user to make clean and precise notches with an accuracy of ±0.1 mm.
- The depth of the notch can be adjusted for ISO 13479, typically representing 19% of the pipe wall thickness.
- Mandrel base for stability and parallelism.
This apparatus is important in investigating how long a pipeline can resist external force attack before the microcracks grow, especially in the case of buried pipelines.
2. Opacity Tester for Pipes
Opacity can certainly be a significant quality control issue in some plastic pipes, especially those that are intended to block UV light or have even color. The opacity tester tests the transparency of plastic pipe samples to see if they have the required visual quality.
Key Features:
- Simultaneous testing of up to four specimens
- High-resolution touchscreen with digital controls.
- Positioning, analysis of results, and batch documentation in real time.
- Energy-efficient design with low maintenance requirements.
This apparatus is especially beneficial for pipes for drinking water systems, where light, if made available, would promote or degrade water quality due to algae growth.
3. Notched Constant Ligament Stress (NCLS) Tester
The Notched Constant Ligament Stress Tester (NCLS) is a precision device designed to test the resistance of high-density polyethylene (HDPE) pipes to slow crack growth under constant stress conditions. This testing is critical for predicting long-term performance, especially in applications involving buried or pressurized pipe systems.
The instrument applies sustained mechanical stress to notched specimens immersed in a controlled environment, simulating years of operational wear in a condensed time frame.
Key Features:
- Simultaneous testing of multiple notched specimens to enhance lab productivity.
- Accurate and stable temperature control to ensure reliable test results.
- Touchscreen interface with programmable settings for easy operation.
- Real-time digital monitoring and automated test result documentation.
- Compact, energy-efficient design suited for continuous lab use.
This tester is essential for pipe manufacturers and quality control laboratories aiming to meet international standards such as ASTM F2136 or ISO 13479. It helps ensure that plastic piping systems remain safe, durable, and crack-resistant throughout their service life.
4. Falling-Weight Impact Tester
The Falling-Weight Impact Tester is specifically designed to assess the impact resistance of thermoplastic pipes such as HDPE, PVC, and PP. This test simulates real-world conditions where pipes may be subjected to accidental drops or external mechanical shocks during handling, transportation, or installation.
By releasing a controlled weight from a set height onto pipe specimens, the tester evaluates the pipe’s ability to withstand sudden impacts without cracking or breaking—ensuring long-term performance and safety in field applications.
Key Features:
- Multiple testing methods, including round-the-clock and staircase procedures.
- Adjustable striker weight and drop height to accommodate various pipe standards.
- High-precision guide mechanism for accurate and consistent impact delivery.
- Anti-rebound system to prevent secondary impacts for enhanced test reliability.
- User-friendly touchscreen interface with real-time monitoring and automated data logging.
- Compliant with international standards such as ISO 3127, ASTM D2444, and EN 744.
This equipment is essential for pipe manufacturers focused on producing high-quality products that meet global safety regulations. It is especially relevant for pipes used in water supply, drainage, and electrical conduit systems, where resistance to sudden impact is a critical performance requirement.
5. Carbon Black Content Tester
The presence of carbon black in plastic pipes is crucial for UV stabilization, especially in HDPE and PP pipes. The carbon black content tester measures the precise amount of carbon black in a pipe sample, ensuring that it meets the standards for longevity and resistance to sunlight.
Key Features:
- Dual furnace configuration for simultaneous testing.
- LED display with programmable temperature segments.
- Oxygen-nitrogen switching and floating ball gas regulation.
- Designed to comply with international test methods for plastic additives.
This device provides essential data for quality control departments, especially when dealing with outdoor piping systems.
6. Hydrostatic Pressure Tester
The Hydrostatic Pressure Tester is a vital instrument for assessing the internal pressure resistance and burst strength of plastic pipes and fittings. It is commonly used to test materials such as PE, PEX, PVC, PP, and PB under constant hydraulic pressure at elevated temperatures.
By simulating long-term operational conditions, this equipment ensures that pipes can withstand internal stresses without failure—making it essential for quality assurance and compliance with global testing standards.
Key Features:
- Modular design allows simultaneous testing of multiple pipe samples.
- High-pressure water pump with stable pressure output and large reservoir.
- Precise pressure control with resolution up to 0.01 bar for accurate testing.
- Temperature-controlled chambers to maintain consistent testing environments.
- Advanced touchscreen interface with real-time monitoring and result logging.
- Integrated safety features and automatic shutdown in case of failure.
- Compliant with international standards such as ISO 1167, ASTM D1598, and ASTM D1599.
This tester is crucial for pipe manufacturers, research labs, and quality control departments. It helps validate product durability, ensures compliance with regulatory standards, and guarantees long-term safety and performance in applications such as plumbing, irrigation, and industrial fluid transport.
Industry Standards and Regulatory Compliance
The work is controlled by a series of national and international standards that stipulate the testing to which the product must be subjected in order to declare conformance with quality and performance. Notable among these are
- ISO 13479—Tests for resistance to slow crack growth in PE pipes.
- ASTM D3350—Specification for PE plastic pipe materials.
- EN 12201—Covers PE piping systems for water supply.
- IS 4984—Indian standard for HDPE pipes for water supply.
Any test machine must therefore not only secure precision and repeatability but must at the same time comply with these global standards. This guarantees they are competitive in domestic and international markets.
Why Use Testron Group’s Pipe Testing Instruments?
Among the leading equipment providers in the field, Testron Group stands out with its wide range of testing machines tailored for the plastic industry. Their devices are designed for precision, consistency, and ease of use. If you want to improve your quality control systems, take a look at their pipe testing equipment—high precision to do the job!
By investing in advanced equipment from trusted suppliers, plastic manufacturers can:
- Reduce product recalls and defects
- Minimize warranty claims and customer complaints.
- Ensure consistency across batches.
- Demonstrate compliance to regulatory bodies
- Enhance brand reputation
Testron’s instruments cater to industries ranging from construction and agriculture to telecom and industrial piping—making them a versatile choice for any plastic product manufacturer.
Benefits of Using Specialized Pipe Testing Equipment
Let’s summarize the broad benefits of integrating pipe testing into your manufacturing process:
Quality Assurance
Using testing tools for real-time monitoring can catch defects early and pave the way for each batch to meet the strict standards.
Product Longevity
With methods such as slow crack growth resistance or carbon black content testing, manufacturers can ensure that their pipes will last over time.
Cost Efficiency
Revealing and addressing problems very early in the process can cut waste, rework, and returns—so money is saved straight off the bottom line.
Customer Trust
Customers can trust our product. Build a product you can stake your life on to instill the trust of contractors, municipalities, and distributors, so they come back to us product after product and refer others to us.
Certification Readiness
Precise standard-test comparisons make it easy to specify ISO and regulatory measurements.
Future Trends in Pipe Testing
The future of pipe testing is moving toward greater automation, digital data logging, and integration with Industry 4.0 technologies. Smart testing labs will use AI to detect anomalies, IoT sensors for remote monitoring, and cloud platforms for real-time reporting.
Manufacturers investing in such future-ready technologies will be better positioned to address global challenges such as water conservation, infrastructure resilience, and sustainable development.
Final Thoughts
The plastics industry heavily depends on product performance, especially in plastic pipe production. Through the use of sophisticated pipe testing equipment—like the units provided by Testron Group—manufacturers ensure the most rigorous levels of quality, safety, and performance.
Whether you’re testing for crack resistance, opacity, UV durability, or pressure handling, the right testing equipment makes all the difference. With evolving technologies and stricter standards, now is the time to upgrade your quality control lab with reliable, efficient, and compliant instruments.
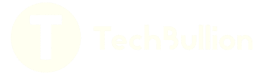