At AWS re:Invent 2021, the tech industry’s premier cloud computing conference, over 20,000 in-person attendees and 600,000 virtual participants gathered for Amazon Web Services’ major cloud computing announcements and product launches. Among these innovations, an industrial IoT solution emerged as a highlight for manufacturing and operations leaders. A team of AWS IoT Data Architects, led by Senior IoT Data Architect Leader Avik Ghosh, demonstrated a practical approach to industrial equipment monitoring – addressing one of the most pressing challenges in asset-intensive industries – while showcasing applications across mining, manufacturing, pharmaceutical, and automotive sectors.
| Avik Ghosh is building the IoT technology revolutionizing industrial monitoring operations
For industrial enterprises, monitoring geographically dispersed equipment poses a critical operational challenge. In mining operations with conveyor belts spanning several miles, manufacturing plants with multiple sites across a region, and distribution centers scattered throughout a country, maintaining operational excellence is complex. With maintenance costs typically accounting for 20 to 60 percent of operational expenditure, preventing equipment failures is not just crucial – it’s a business imperative. Manual inspections prove especially inefficient for equipment like long-distance conveyor systems, requiring extensive labor hours and travel time that drive up operational costs. The situation is complicated by non-optimal maintenance schedules, limited visibility into asset conditions, and disparate workforce knowledge, particularly when managing distributed assets across vast distances.
“The core challenge in industrial operations isn’t data collection, but transforming raw information into actionable insights that prevent failures and reduce costs,” explains Avik. His perspective reflects years of experience implementing IoT solutions across various industrial sectors. These insights, when properly implemented, drive measurable improvements in operational efficiency and equipment performance. Using an industrial conveyor system as a practical example, Avik demonstrated how these principles address common challenges in asset-intensive industries. A McKinsey study on industrial maintenance reveals that intelligent condition monitoring solutions can reduce maintenance costs by 20 to 30 percent.
Leveraging AWS IoT SiteWise, a managed service for industrial equipment data management, integrated with Amazon Monitron, a condition monitoring service, Avik designed and implemented comprehensive monitoring algorithms. The system’s analytics engine processes critical operational data including belt speed, tension, and vibration patterns – parameters that help predict potential equipment failures. The solution enables enterprises to monitor their industrial operations effectively, providing comprehensive insights through continuous monitoring of temperature patterns, vibration signals for misalignment detection, and near-real-time visualization of operational efficiency metrics. This predictive maintenance system integrates with existing enterprise infrastructure for maintenance, asset management, and quality control, while demonstrating real-time control capabilities through automated responses to critical situations, such as automatically stopping conveyor belts during overweight conditions or pile-ups – a practical example of how industrial IoT can enhance operational safety and efficiency.
The framework demonstrates broad applicability across industrial sectors, where the combination of distributed sensors, local processing at equipment sites (edge computing), and advanced analytics can be adapted for various industrial processes requiring continuous monitoring,” explains Avik. The architecture addresses common challenges in environments with high-value assets and complex operations.
In regulated industries like pharmaceutical manufacturing, similar monitoring principles could help maintain equipment performance while supporting compliance requirements. For automotive production lines, where equipment reliability directly impacts quality and throughput, the framework’s predictive maintenance approach could help optimize operations.
The solution’s architecture efficiently handles geographically distributed assets through a scalable data processing framework. “The key is creating a scalable architecture that can effectively process data from remote locations while maintaining centralized analysis capabilities,” notes Avik. The system processes both real-time data streams for immediate operational decisions and historical data for long-term performance analysis. This comprehensive approach to data processing enables both rapid response to operational issues and systematic improvement of processes over time. This approach provides a practical reference for organizations planning their industrial IoT implementations.
Through the practical application of cloud computing and IoT services, Avik’s work demonstrates how organizations can systematically improve operational efficiency, safety, and cost optimization – key priorities as industrial operations continue to evolve in the digital era.
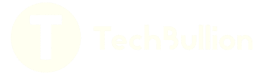