In today’s industrial landscape, energy efficiency has emerged as a pivotal focus for manufacturers, plant operators, and businesses striving to reduce operational costs and minimize their environmental impact. Large industrial motors are critical components in various sectors, powering equipment used in manufacturing, processing, and transportation. With the increasing demand for sustainable practices, regulatory bodies have established energy efficiency standards aimed at optimizing motor performance and promoting energy savings. This article delves into the key energy efficiency standards for large industrial motors, what they mean for businesses, and how they can impact operations. If you’re in the market for large industrial motors for sale, understanding these standards will help you make informed decisions.
Understanding Energy Efficiency Standards
Energy efficiency standards for large industrial motors are designed to ensure that electric motors consume less energy while providing the required performance levels. These standards vary by region, with major guidelines established by organizations such as the U.S. Department of Energy (DOE), the International Electrotechnical Commission (IEC), and the National Electrical Manufacturers Association (NEMA). Here’s a closer look at these standards:
1. NEMA Efficiency Standards
The National Electrical Manufacturers Association (NEMA) has set standards that categorize motors based on their efficiency. NEMA Premium motors, for example, are designed to operate at higher efficiency levels than standard motors. The efficiency of these motors is measured using a specific test procedure outlined in NEMA MG 1.
- Standard Efficiency Motors: These motors meet the minimum efficiency requirements set by NEMA. While they can be less expensive upfront, they may result in higher energy costs over time due to lower efficiency.
- NEMA Premium Efficiency Motors: These motors exceed the minimum efficiency requirements and typically offer energy savings of 3% to 8% compared to standard motors. Though they may have a higher initial cost, the long-term savings in energy consumption can make them a cost-effective choice.
2. IE Energy Efficiency Standards
The International Electrotechnical Commission (IEC) has established a global standard for motor efficiency known as the IEC 60034-30. This standard classifies motors into efficiency classes, which are designated as IE1, IE2, IE3, and IE4:
- IE1: Standard Efficiency
- IE2: High Efficiency
- IE3: Premium Efficiency
- IE4: Super Premium Efficiency
IE3 and IE4 motors are increasingly becoming the standard for new installations, as they provide significant energy savings and lower operational costs.
The Importance of Energy Efficiency Standards
Energy efficiency standards are critical for various reasons:
1. Cost Savings
Energy-efficient motors consume less electricity, leading to lower energy bills. For industrial operations where motors run continuously, these savings can be substantial. The reduction in energy costs can often offset the higher initial investment in premium efficiency motors within a few years.
2. Environmental Impact
Reducing energy consumption contributes to lower greenhouse gas emissions, supporting corporate sustainability initiatives and compliance with environmental regulations. Energy-efficient motors help companies reduce their carbon footprint and contribute to global efforts to combat climate change.
3. Regulatory Compliance
Many regions have adopted regulations mandating minimum efficiency standards for industrial motors. Non-compliance can result in fines and operational disruptions. Understanding and adhering to these standards is essential for manufacturers and businesses to avoid penalties.
4. Improved Performance and Reliability
Energy-efficient motors are designed with advanced technologies that enhance their performance and reliability. These motors often have longer lifespans and require less maintenance, reducing the total cost of ownership for businesses.
Selecting Energy-Efficient Large Industrial Motors
When considering the purchase of large industrial motors, it’s essential to evaluate options that meet or exceed energy efficiency standards. Here are some key factors to consider:
1. Motor Type and Design
Different types of motors have varying efficiencies based on their design. For example, squirrel cage induction motors are widely used due to their robust design and reliability. When choosing a motor, consider the application, required torque, speed, and load characteristics to ensure optimal performance.
2. Efficiency Ratings
Look for motors with high-efficiency ratings, such as NEMA Premium or IE3 and IE4 classifications. These ratings indicate that the motor meets stringent efficiency standards and will provide significant energy savings over its operational life.
3. Size and Capacity
Ensure that the motor’s size and capacity align with the specific needs of your application. Oversized motors can lead to inefficiencies, while undersized motors may struggle to meet performance demands. Conducting a thorough assessment of your application’s requirements will help determine the right motor size.
4. Vendor and Manufacturer Reputation
Choosing a reputable manufacturer ensures you receive a quality product that adheres to energy efficiency standards. Research manufacturers’ certifications, warranty offerings, and customer reviews to gauge their reliability and product performance.
The Role of Energy Audits
Conducting an energy audit is a proactive step toward understanding energy consumption and identifying opportunities for efficiency improvements. An energy audit assesses current motor operations, evaluates performance metrics, and identifies potential upgrades or replacements. Here’s how energy audits can contribute to energy efficiency:
1. Identifying Inefficient Motors
An energy audit can reveal which motors are underperforming or consuming excessive energy. By replacing these motors with energy-efficient models, businesses can significantly reduce their energy consumption and costs.
2. Optimizing Motor Usage
Energy audits can help identify how motors are being utilized within processes. By optimizing usage, such as implementing variable frequency drives (VFDs) for better speed control, businesses can enhance overall efficiency.
3. Benchmarking Performance
Energy audits establish benchmarks for motor performance, allowing businesses to monitor improvements over time. This data is valuable for setting goals for energy efficiency and sustainability initiatives.
Challenges in Implementing Energy Efficiency Standards
While energy efficiency standards provide numerous benefits, challenges can arise when implementing them:
1. Initial Costs
Although energy-efficient motors can save money in the long run, the initial investment may be higher compared to standard motors. Some businesses may be hesitant to invest in new technology due to budget constraints. However, financial incentives, rebates, and government programs may offset these costs.
2. Resistance to Change
Changing existing systems and processes can be met with resistance from employees and management. To mitigate this, it is essential to communicate the benefits of energy efficiency, such as cost savings and improved performance, to gain buy-in from stakeholders.
3. Integration with Existing Equipment
Upgrading to energy-efficient motors may require additional modifications or investments incompatible equipment. Businesses should assess their current infrastructure to determine how new motors will integrate into existing systems.
The Future of Energy Efficiency Standards
As the demand for sustainable practices grows, energy efficiency standards for large industrial motors will likely continue to evolve. Future trends may include:
1. Stricter Regulations
Regulatory bodies may implement stricter energy efficiency requirements, pushing businesses to adopt higher-efficiency motors. Staying informed about upcoming regulations will be essential for compliance.
2. Technological Advancements
Innovations in motor technology, such as smart motors and IoT connectivity, will further enhance energy efficiency. These technologies can enable real-time monitoring and data analysis to optimize performance and energy consumption.
3. Focus on Sustainability
As businesses prioritize sustainability, energy efficiency will remain a key focus. Large industrial motors will play a significant role in achieving these goals, with increased demand for environmentally friendly solutions.
Conclusion
Energy efficiency standards for large industrial motors are crucial for promoting sustainable practices and reducing operational costs in the industrial sector. Understanding these standards, including NEMA and IEC classifications, allows businesses to make informed decisions when purchasing motors. By selecting energy-efficient motors, conducting energy audits, and implementing best practices, companies can enhance their operational efficiency, comply with regulations, and contribute to environmental sustainability.
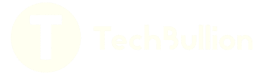