In today’s competitive manufacturing landscape, maintaining impeccable quality standards is no longer just an advantage—it’s a necessity. As consumer expectations rise and regulatory requirements become more stringent, manufacturers are turning to cutting-edge technologies to ensure their products meet the highest quality benchmarks. Among these innovations, machine vision system has emerged as a game-changer in defect detection and quality control, revolutionizing the way industries approach product integrity.
The Evolution of Quality Control
Traditionally, quality control relied heavily on human inspectors or basic automated systems. While these methods served industries well for decades, they came with inherent limitations. Human inspectors, no matter how skilled, are susceptible to fatigue, inconsistency, and the inability to detect minute defects consistently. Basic automated systems, while more consistent, often lack the flexibility to adapt to new products or subtle variations in defects.
Enter machine vision systems. These sophisticated technologies combine high-resolution cameras, advanced lighting techniques, and powerful image processing algorithms to create a quality control powerhouse. By leveraging the latest advancements in artificial intelligence and deep learning, machine vision defect detection is setting new standards for accuracy, speed, and reliability in manufacturing environments.
The Anatomy of Machine Vision Defect Detection
At its core, a machine vision system for defect detection consists of several key components:
- High-Resolution Cameras: These capture detailed images of products as they move along the production line.
- Image Processing Software: Sophisticated algorithms analyze the captured images, identifying deviations from predefined quality standards.
- Data Management Systems: Results are logged and analyzed, providing valuable insights for continuous improvement.
- Integration with Production Systems: Detected defects can trigger automated responses, such as product rejection or production line adjustments.
The Power of Precision
One of the most significant advantages of machine vision defect detection is its ability to identify flaws that would be imperceptible to the human eye. These systems can detect:
- Microscopic surface imperfections
- Subtle color variations
- Dimensional inaccuracies down to fractions of a millimeter
- Misaligned components in complex assemblies
- Inconsistencies in texture or finish
This level of precision ensures that even the most minor defects are caught before products reach the end consumer, dramatically reducing the risk of recalls and enhancing brand reputation.
Speed Without Compromise
In addition to unparalleled accuracy, machine vision systems operate at speeds that far surpass human capabilities. Modern systems can inspect hundreds or even thousands of products per minute, depending on the application. This high-speed operation doesn’t come at the expense of quality—in fact, the consistency of machine vision often leads to improved overall quality metrics.
The speed of machine vision defect detection allows manufacturers to:
- Increase production throughput
- Reduce bottlenecks in quality control processes
- Implement 100% inspection protocols without sacrificing efficiency
Adaptability Across Industries
While initially adopted primarily in electronics and automotive manufacturing, machine vision defect detection has found applications across a wide range of industries:
- Pharmaceutical Production: Ensuring the integrity of medications and packaging.
- Food and Beverage: Detecting contaminants and verifying product consistency.
- Textile Manufacturing: Identifying weaving errors and color inconsistencies.
- Aerospace: Inspecting critical components for microscopic flaws.
- Consumer Electronics: Verifying the quality of displays, casings, and internal components.
This versatility demonstrates the adaptability of machine vision systems to diverse manufacturing environments and quality control requirements.
Beyond Defect Detection: Comprehensive Quality Assurance
While identifying defects is a primary function, modern machine vision systems offer much more in terms of quality assurance:
- Dimensional Verification: Ensuring products meet precise size and shape specifications.
- Assembly Verification: Confirming that all components are present and correctly positioned.
- Label and Packaging Inspection: Verifying the accuracy and quality of product labeling and packaging.
- Traceability: Tracking products through the manufacturing process using barcodes or other identifiers.
By combining these capabilities, manufacturers can implement comprehensive quality control strategies that address multiple aspects of product integrity simultaneously.
The Role of Artificial Intelligence and Machine Learning
The integration of AI and machine learning has dramatically enhanced the capabilities of machine vision defect detection:
- Adaptive Learning: Systems can learn from new data, improving their ability to detect novel or evolving defect types.
- Pattern Recognition: Advanced algorithms can identify complex patterns that might indicate underlying quality issues.
- Predictive Maintenance: By analyzing defect trends, AI can predict when equipment might be at risk of producing faulty products.
- Contextual Decision Making: Machine learning models can consider multiple factors to make nuanced decisions about product quality.
These AI-driven capabilities allow machine vision systems to go beyond simple pass/fail criteria, providing deeper insights into quality trends and potential process improvements.
Overcoming Implementation Challenges
While the benefits of machine vision defect detection are clear, implementing these systems does come with challenges:
- Initial Investment: The upfront cost of machine vision systems can be significant, requiring careful ROI analysis.
- Integration with Existing Systems: Incorporating machine vision into established production lines may require process adjustments.
- Training and Skill Requirements: Operators and maintenance personnel need specialized training to manage these sophisticated systems.
- Continuous Calibration: Ensuring ongoing accuracy requires regular system calibration and maintenance.
Despite these challenges, the long-term benefits in terms of improved quality, reduced waste, and enhanced productivity often far outweigh the initial hurdles.
The Future of Machine Vision in Quality Control
As technology continues to advance, we can expect to see even more sophisticated applications of machine vision in defect detection and quality control:
- Hyperspectral Imaging: Detecting defects based on material composition, not just visual appearance.
- 3D Inspection: More advanced 3D imaging techniques for complex geometric analysis.
- Edge Computing: Faster processing and decision-making at the point of inspection.
- Augmented Reality Integration: Combining machine vision data with AR displays for enhanced human-machine collaboration in quality control.
These emerging technologies promise to further elevate the capabilities of machine vision systems, enabling even higher standards of quality assurance in manufacturing.
As we move further into the age of Industry 4.0 and smart manufacturing, machine vision will undoubtedly play an increasingly central role in ensuring product integrity and consumer satisfaction. For manufacturers looking to stay ahead in a competitive global market, embracing machine vision defect detection isn’t just an option—it’s a necessity for elevating quality standards and securing a reputation for excellence.
By investing in these advanced technologies, companies can not only meet but exceed the ever-increasing demands for product quality, positioning themselves as leaders in their respective industries. The future of manufacturing is here, and it’s being viewed through the lens of machine vision.
Read More From Techbullion And Businesnewswire.com
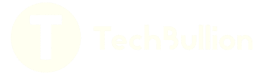