- Introduction
In modern manufacturing and engineering, welding processes play a pivotal role in joining metals and materials. Over the years, various welding techniques have emerged, each with advantages and limitations. Electron Beam Welding (EBW) has gained significant attention due to its unique benefits and applications. This article explores the advantages of Electron Beam Welding, shedding light on its capabilities and why it is preferred for specific applications over other welding methods.
- What is Electron Beam Welding?
Electron Beam Welding (EBW) is an exact and advanced welding technique that employs a concentrated beam of high-velocity electrons to join materials. The process occurs in a vacuum environment, eliminating the need for atmospheric interference. The focused electron beam generates intense heat upon striking the workpiece, resulting in localized melting and fusion of the materials. The shaft is precisely controlled, allowing for exceptional welding accuracy and control.
- How Does Electron Beam Welding Work?
In Electron Beam Welding, electrons are generated by an electron gun and accelerated through an electromagnetic field, gaining tremendous kinetic energy. These high-energy electrons are then focused into a narrow beam and directed towards the welding area. The beam’s power is transferred to the workpiece, causing the material to melt and form a weld pool. The molten material solidifies as the shaft moves along the joint, creating a robust and reliable weld.
- Advantages of Electron Beam Welding
4.1 High Precision and Control
EBW excels in providing precise and intricate welds, making it ideal for applications where accuracy is critical. The focused electron beam enables welds with minimal width, ensuring that heat-affected zones are kept to a minimum. This precision is especially beneficial for delicate components and intricate structures.
4.2 Deep Welding Capability
EBW has an excellent depth-to-width ratio, allowing it to penetrate deeply into thick materials. This deep welding capability is advantageous when joining materials with substantial thicknesses, offering superior weld strength and quality throughout the joint.
4.3 Minimal Distortion
Compared to conventional welding methods, EBW produces less distortion in the workpiece. The focused and localized heat input minimizes thermal expansion, reducing the risk of warping or deformation in the welded components.
4.4 Limited Heat-Affected Zone (HAZ)
One of the primary benefits of EBW is its ability to create welds with a narrow and well-defined heat-affected zone. This characteristic is vital when working with heat-sensitive materials, as it helps prevent undesirable changes in material properties.
4.5 Joining Dissimilar Materials
EBW can effectively join dissimilar materials, such as metals, with vastly different melting points. The precise control over the welding process ensures that the materials are entered without compromising their individual properties.
4.6 Vacuum Environment Benefits
Operating in a vacuum environment offers several advantages. It eliminates the risk of atmospheric contamination and oxidation during welding, resulting in higher-quality welds with improved mechanical properties.
4.7 Cost-Effectiveness
Though the initial setup for EBW can be costly, it offers long-term cost-effectiveness due to reduced material waste, minimal post-welding processing, and enhanced productivity.
4.8 Environmentally Friendly
The absence of filler materials in EBW and the minimized need for post-welding treatments contribute to a more environmentally friendly welding process.
4.9 Versatility in Applications
EBW finds applications in various industries, including aerospace, automotive, electronics, medical devices, and more, showcasing its versatility in meeting diverse manufacturing needs.
4.10 Reduced Post-Welding Processing
The high-quality welds produced by EBW often require minimal post-welding processing, saving both time and costs for manufacturers.
4.11 Non-Contact Welding Process
EBW is a non-contact welding process, which means the electron beam does not physically touch the workpiece. This attribute makes it suitable for welding delicate or easily deformed materials.
4.12 Joining High-Temperature Materials
EBW can join high-temperature materials without compromising their properties, making it an ideal choice for aerospace and advanced materials applications.
4.13 Enhanced Weld Quality
The controlled and focused nature of the electron beam results in welds with exceptional quality, offering high joint strength and integrity.
4.14 Welding of Complex Shapes
EBW’s ability to weld intricate and complex shapes makes it a preferred method for joining components with unique geometries.
4.15 Automation and Efficiency
EBW can be easily integrated into automated manufacturing processes, increasing efficiency and productivity.
- Conclusion
Electron Beam Welding (EBW) is a highly advanced and precise welding technique with numerous advantages. Its ability to deliver high precision, deep welding, minimal distortion, and limited heat-affected zones makes it an excellent choice for various applications. Moreover, EBW’s non-contact welding process, vacuum environment benefits, and cost-effectiveness further add to its appeal. As technology advances, the significance of Electron Beam Welding is expected to grow, revolutionizing various industries and enabling innovative designs.
- FAQs
Q1: Is Electron Beam Welding safe for delicate electronic components?
A: Electron Beam Welding is safe for delicate electronic components due to its non-contact welding process and precise heat control.
Q2: Can Electron Beam Welding join dissimilar materials?
A: Absolutely! Electron Beam Welding can join dissimilar materials with varying melting points and properties.
Q3: Does EBW produce environmentally friendly welds?
A: EBW is environmentally friendly due to its minimal waste generation and reduced need for post-welding processing.
Q4: What industries commonly use Electron Beam Welding?
A: Electron Beam Welding finds applications in industries such as aerospace, automotive, electronics, medical devices, and more.
Q5: Can EBW be automated for large-scale production?
A: EBW can be easily integrated into automated manufacturing processes, making it efficient for large-scale production.
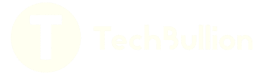