In the dynamic landscape of modern manufacturing, businesses are constantly seeking ways to enhance efficiency, reduce waste, and optimise productivity. One approach that has gained widespread recognition for achieving these goals is Lean Manufacturing. At the heart of Lean Manufacturing principles lies the 5S methodology, a system designed to organise the workplace for maximum efficiency and effectiveness. In this article, we will delve into the symbiotic relationship between Lean Manufacturing and 5S, with a particular focus on the role of 5S Shadow Boards.
Understanding Lean Manufacturing:
Lean Manufacturing is a systematic method that originated from the Toyota Production System, emphasising the elimination of waste, continuous improvement, and the pursuit of perfection. At its core, Lean Manufacturing seeks to deliver maximum value to customers while minimising resource utilisation.
The five pillars of Lean Manufacturing, often referred to as the 5S framework, include:
1) Sort (Seiri): Sorting involves eliminating unnecessary items from the workplace. By keeping only the essential tools and materials, a company can reduce clutter and streamline its operations.
2) Set in Order (Seiton): This step focuses on arranging the necessary items in a logical and efficient manner. The goal is to enhance accessibility, minimise search time, and prevent the loss of valuable resources.
3) Shine (Seiso): Cleaning and maintaining a clean workspace is crucial in Lean Manufacturing. A clean environment not only promotes safety but also helps identify abnormalities and potential issues.
4) Standardise (Seiketsu): Standardisation involves creating and implementing consistent procedures and practices across the organisation. This ensures that the gains made in sorting, arranging, and cleaning are sustained over time.
5) Sustain (Shitsuke): Sustaining the improvements achieved through the 5S methodology requires ongoing commitment and discipline. It involves creating a culture of continuous improvement within the organisation.
The Role of 5S Shadow Boards:
As companies embrace Lean Manufacturing principles, they often implement tools and techniques to facilitate the 5S methodology. One such tool that has proven to be highly effective is the 5S Shadow Board.
5s tools shadow boards is a visual management tool that provides a designated space for each tool, equipment, or material required for a specific task. The board typically outlines the shape and size of each item, making it immediately apparent if something is missing. This visual cue not only aids in quickly locating tools but also highlights any deviation from the standardised process.
Let’s explore how 5S Shadow Boards contribute to the broader context of Lean Manufacturing:
- Enhanced Organisation: By providing a designated space for each tool, 5S Shadow Boards contribute to the “Set in Order” principle of Lean Manufacturing. This systematic organisation minimises the time spent searching for tools, reducing downtime and improving overall efficiency.
- Waste Reduction: The primary objective of Lean Manufacturing is to eliminate waste in all its forms, including time, resources, and effort. 5S Shadow Boards directly address this by preventing the misplacement or loss of tools, thus minimising the waste associated with searching for or replacing missing items.
- Visual Management: Lean Manufacturing places a strong emphasis on visual management to facilitate quick decision-making and problem-solving. 5S Shadow Boards serve as a visual indicator of the status quo, making it easy for employees to identify discrepancies and take corrective action.
- Standardisation: The use of 5S Shadow Boards promotes standardisation by establishing a uniform and organised system for tool storage. This adherence to standardised procedures aligns with the “Standardise” principle of Lean Manufacturing, ensuring consistency in processes across the organisation.
- Continuous Improvement: The “Sustain” principle of Lean Manufacturing emphasises the need for continuous improvement. 5S Shadow Boards act as a tangible reminder of the established standards, encouraging employees to uphold and improve upon these standards over time.
Conclusion:
In conclusion, the integration of 5S Shadow Boards into the broader framework of Lean Manufacturing represents a powerful strategy for organisations seeking to enhance efficiency and reduce waste. These visual management tools not only contribute to the 5S methodology but also embody the principles of Lean Manufacturing by promoting organisation, waste reduction, visual management, standardisation, and continuous improvement.
As businesses navigate the ever-evolving landscape of manufacturing, embracing the synergy between Lean Manufacturing and 5S Shadow Boards can be a game-changer. By fostering a culture of efficiency and continuous improvement, organisations can position themselves for sustained success in a competitive market.
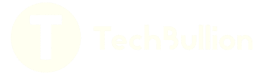