Executive take‑away: Unscheduled breakdowns now drain more margin than rising fuel prices for many U.S. fleets. New sensor platforms and AI models can predict component failure days in advance, slashing roadside events by up to 55 %. The dollars at stake—anywhere from $300,000 to $500,000 per hour of lost uptime—justify a fast pivot from reactive to predictive programs.
A Hidden Expense Bigger Than Fuel Spikes
A 2024 survey of 1,000 global enterprises found that 90 % now peg the cost of an hour of downtime above $300,000—up 27 % versus 2022. For fleets, that figure includes tow bills, missed service‑level agreements, and per‑diem driver pay. Meanwhile, the Federal Motor Carrier Safety Administration reports that vehicle‑maintenance violations made up 59 % of all roadside citations last year, with brakes and tires topping the list.
Why Time‑Based Maintenance Isn’t Working
Traditional service intervals assume uniform wear. Reality looks different:
- Brake wear is load‑dependent. CVSA’s 2024 Brake Safety Week found that 13 % of inspected trucks were pulled out of service for brake issues despite being “on schedule.”
- Tire costs escalate when pressure drifts. DOE testing shows under‑inflation can shave up to 3 % off fuel economy and accelerate tread loss.
Because these failures hit randomly, fleets pay a “downtime tax” that finance teams rarely model.
Sensor Fusion Meets Edge AI
Over the past 18 months, heavy‑duty suppliers have merged wheel‑end temperature probes, TPMS, and vibration microphones into hub‑mounted sensor packs. Data is processed on a credit‑card‑sized gateway running embedded AI, then pushed via MQTT to shop bays.
- Thermal drift >40 °F in a single hour often flags dragging brakes.
- Spectral vibration signatures detect bearing pitting up to 500 miles before audible noise appears.
- Pressure delta curves spot slow tire leaks within 20 minutes of departure.
McKinsey calculates that predictive models can cut reactive maintenance labor by 15 – 30 % at scale.
Sidebar | Route Optimization + Maintenance
ROI Math: Two Scenarios
Fleet Size |
Baseline Unscheduled Events/Year |
Downtime Cost/hr |
Predicted Reduction |
Net Annual Saving |
250 tractors |
140 events |
$350 k |
45 % |
$22 M |
40 tractors |
22 events |
$120 k |
35 % |
$0.9 M |
CapEx for sensors + software averages $1,200 per tractor; payback arrives inside nine months for either fleet.
Early‑Warning KPIs
- Brake Stroke Variance > 0.25 in. across axles
- Bearing RMS Vibration > 7 mm/s for 30 min
- Tire Pressure Loss Rate > 0.5 psi/min (compounded)
- Coolant Dielectric Drop > 15 % in 24 h (signals liner pitting)
Shop supervisors who track these KPIs reported 25 % fewer CSA maintenance points at the 2024 FMCSA Safety Forum.
Regulatory Tailwinds
- CARB’s Omnibus Warranty Rule extended emissions‑component coverage from 350 k to 450 k miles, adding $3,400 per truck if failures occur post‑warranty. Predictive alerts help fleets schedule warranty work before the clock runs out.
- CVSA Brake Safety Week visibility pressures shippers to select fleets that can prove compliance via sensor logs, not paper.
Implementation Blueprint
Phase |
Duration |
Pilot (60 days) |
Identify worst‑performing lane; install 10 sensor kits; benchmark fault frequency. |
Scale (6 months) |
Connect gateway feed to TMS; automate work‑order creation; train drivers on cab alerts. |
Monetize (Year 1+) |
Use downtime deltas to renegotiate detention rates and secure green‑lane contracts with data‑hungry shippers. |
Field Insight: Integrating Routes with Maintenance
In an in‑depth study, Valerii Khomynskyi reports that linking hub‑sensor alerts to the TruckSync routing platform lets dispatchers steer equipment toward pre‑approved service bays without missing delivery slots. His analytics show a 55 percent drop in roadside failures and an 8 percent fuel saving thanks to fewer last‑minute detours.
What Could Stall Adoption?
- Data silos—suppliers insist on proprietary dashboards.
- Cyber‑risk—edge devices need signed firmware; NIST’s IoT security framework offers a template.
- Culture—techs paid by billable hours may resist “fix before fail” models.
Forward‑leaning fleets counter these hurdles by:
- Requiring open MQTT feeds in RFPs.
- Integrating sensor data with CSA scorecards to keep safety managers engaged.
- Paying techs a bonus for each prevented roadside call versus hours billed.
Fuel hedging once separated winning carriers from the pack; in 2025, predictive maintenance will become the new hedge. Fleets that treat downtime like diesel—an expense to be priced, monitored, and algorithmically reduced—are positioned to bank double‑digit margin gains while boosting safety and ESG scores.
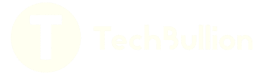