A double jacketed 5L glass reactor is a type of laboratory equipment used for chemical reactions, mixing, and heating or cooling of substances. It consists of a glass vessel with two layers: an inner vessel or “reactor” and an outer jacket. The two layers are separated by a space, often filled with a heat transfer fluid or coolant.
The inner vessel, or reactor, is where the chemical reaction takes place. It is made of high-quality borosilicate glass, which is resistant to thermal shock and chemical corrosion. The glass material allows for excellent visibility of the reaction inside the vessel.
The outer jacket surrounds the inner vessel and provides a space for temperature control. It can be filled with a circulating liquid, such as water or oil, which can be heated or cooled using an external temperature control system. By circulating the temperature control fluid through the jacket, the temperature of the reaction can be precisely regulated.
The double jacketed design offers several advantages in laboratory applications. It provides better temperature control compared to single-walled reactors and helps maintain a consistent temperature throughout the reaction. The jacket also acts as a safety feature by preventing direct contact between the reactants and the external environment, reducing the risk of contamination or heat loss.
Double jacketed 5L glass reactor is commonly used in various scientific fields, including chemistry, pharmaceuticals, biotechnology, and research laboratories. They are especially useful for reactions that require precise temperature control and for processes involving sensitive or corrosive substances.
Features of double jacketed glass reactors
Stirring and Mixing: Double jacketed glass reactors often come with a built-in stirring mechanism, such as a magnetic stirrer or an overhead mechanical stirrer. This enables efficient mixing of reactants and helps to maintain uniformity throughout the reaction.
Temperature Control: The double jacket design allows for precise temperature control during chemical reactions. The circulating temperature control fluid in the outer jacket helps to regulate the temperature of the reaction inside the inner vessel. This feature is particularly beneficial for reactions that require specific temperature conditions or temperature gradients.
Versatility: Double jacketed glass reactors can accommodate a wide range of chemical processes, including synthesis, distillation, reflux, crystallization, and more. They are compatible with various types of chemical reactions, such as organic reactions, polymerizations, and reactions involving corrosive substances.
Safety: The double jacketed glass construction provides a layer of protection for both the reactants and the operators. It helps contain any potential spills or leaks within the system, reducing the risk of exposure to hazardous materials. Additionally, the transparent glass walls allow operators to visually monitor the reaction without the need to open the vessel, minimizing the chances of accidental contact or contamination.
Easy Maintenance: Double jacketed glass reactors are relatively easy to clean and maintain. The glass material is resistant to many chemicals, making it suitable for a wide range of applications. Additionally, the modular design of these reactors allows for easy replacement or upgrade of individual components, such as the stirring mechanism or the temperature control system.
Scale-up Challenges: While double jacketed glass reactors are commonly used in laboratory settings, scaling up processes to larger volumes can be challenging. Glass reactors are generally limited in size due to the mechanical strength of the glass material. For larger-scale industrial applications, alternative reactor types, such as stainless steel reactors, are often used.
It’s important to note that while double jacketed glass reactors are versatile and widely used, they do have limitations. They are typically limited in size and capacity and may not be suitable for large-scale industrial processes. Additionally, they may not be suitable for highly exothermic reactions or reactions involving high pressures. In such cases, alternative reactor designs may be more appropriate.
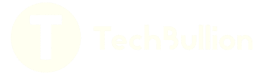