Manufacturing Execution Systems (MES) are used to track and document the transformation of raw materials into finished products. With the help of MES, manufacturing decision-makers can analyze how current conditions on the manufacturing floor can be optimized to improve production efficiency. This technology is more than a set of tools for collecting data.
Most MES applications are incorporated into a distributed control system (DCS) that controls factory equipment and an enterprise resource planning (ERP) system that controls activities throughout the organization.
MES is best understood through its functions. Among its key functions are:
-
Scheduling
An MES schedule can be created from the ERP schedule or control the ERP schedule. It is based on production requirements, which include customer orders, order due dates, finished goods inventory levels, WIP inventory levels, and lot size requirements.
-
Execution
The MES provides information on what is required for a work center to produce a product or assembly. This includes machine setup instructions and operator activities such as applying labels or loading material into a machine. These instructions can be visual displays that operators can view on a PC screen or mobile device.
-
Collection
Production data from machines, operators, and bar code scans need to be collected by the MES in real-time and available for instant visibility. This includes the capture of scrap, labor time, downtime reason codes, and other important metrics for tracking productivity.
The most important tasks an MES performs:
- Planning: Scheduling, loading, dispatching, and tracking of personnel
- Manufacturing: Monitoring, collection, and analysis of data from machines, operators, and shop floor activities
- Control: Optimization of key performance indicators such as OEE (Overall Equipment Effectiveness)
- Reporting: Generating reports for decision-makers to improve productivity
- ERP integration: Seamless integration between ERP applications
One of the benefits of MES is that it provides real-time feedback, thus allowing you to make changes if things do not proceed as planned. If something goes wrong on one part of the line, then it can be escalated immediately to deal with any problems or delays.
To learn more about it, visit FMCG Manufacturing – ANT Solutions.
Summing-up:
A manufacturing execution system (MES) is a software program designed to assist in the manufacturing process. The MES can be seen as the missing link between enterprise resource planning (ERP) and the shop floor control system (SCS).
It helps you integrate your entire manufacturing operation, from materials management to quality control, into a centralized system with real-time visibility for every aspect of production. This allows more efficient processes, accurate reporting and means you’re better placed to meet customer demand.
The MES is a business application, and therefore it’s not a simple IT solution. It’s an operational tool that takes data from processes and makes them available to operations in order to improve efficiency and productivity.
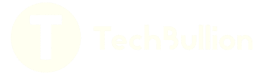