Innovation is not merely an advantage—it’s a necessity. One of the most transformative technologies making waves in the industry is Digital Twin technology. Essentially, a Digital Twin is a virtual replica of a physical object, system, or process. It leverages data from sensors, AI, and analytics to simulate, predict, and optimize operations in real time. For manufacturers in the USA, this powerful innovation is unlocking a new era of efficiency, cost-savings, and competitive advantage.
Understanding the Concept of Digital Twins in Manufacturing
To begin with, it’s important to clarify what makes Digital Twin technology so revolutionary. Unlike traditional simulation models, Digital Twins are dynamic and real-time, continuously updating based on live input. They replicate not just the physical appearance but also the behavior and performance of machinery, systems, or even entire manufacturing facilities.
Moreover, these models integrate with Industrial Internet of Things (IIoT) devices, cloud computing platforms, machine learning algorithms, and big data analytics. Consequently, manufacturers can monitor production processes, predict equipment failures, optimize workflows, and even simulate future scenarios—without disrupting ongoing operations.
Key Benefits of Digital Twins in Enhancing Manufacturing Efficiency
Manufacturing efficiency is about more than just speed. It encompasses cost-effectiveness, product quality, sustainability, and adaptability. Here’s how Digital Twins contribute across these dimensions:
Real-Time Monitoring and Predictive Maintenance
One of the most impactful applications of Digital Twins is in predictive maintenance. By continuously collecting and analyzing sensor data from machinery, the twin can detect early signs of wear or malfunction. This allows engineers to schedule repairs proactively, thereby avoiding unplanned downtime and costly breakdowns.
Furthermore, real-time monitoring provides deep insights into performance trends, enabling companies to fine-tune equipment settings for optimal output. In turn, this extends the lifespan of assets while minimizing maintenance costs.
Process Optimization and Workflow Efficiency
Manufacturers are under constant pressure to do more with less. With a Digital Twin, it’s possible to simulate production processes to identify bottlenecks, waste, and inefficiencies. For example, adjusting machine sequences, reassigning labor, or tweaking material inputs can all be tested virtually before any physical changes are made.
Additionally, these optimizations are not static. Because Digital Twins are live systems, adjustments can be made on-the-fly as conditions change—such as a shift in customer demand or supply chain disruptions.
Enhanced Product Design and Customization
Digital Twins are not just for machines—they also apply to products. In product development, manufacturers can create virtual prototypes and simulate various use-case scenarios. This speeds up design cycles and ensures products meet performance and safety requirements before going into production.
Besides that, the feedback loop from customers and real-world usage data can be integrated into the twin, allowing companies to evolve their products more quickly and cost-effectively. This adaptability is a significant advantage in markets that demand rapid innovation and personalization.
Reduced Operational Costs
Efficiency improvements naturally lead to cost savings. Whether it’s through lower energy consumption, fewer material losses, reduced downtime, or improved labor utilization, the financial gains can be substantial. Many American manufacturers are already reporting ROI within months of deploying Digital Twin solutions.
What’s more, these savings aren’t just one-time—they compound over time. As systems learn and improve, the twin becomes more accurate and valuable, delivering continued returns.
Tailored Digital Twin Services for U.S. Manufacturers
The United States manufacturing sector is highly diverse, ranging from automotive and aerospace to pharmaceuticals and consumer electronics. Therefore, service providers have developed customized Digital Twin solutions that address the unique needs of different industries.
Industry-Specific Solutions
Digital Twin platforms can be tailored to meet the specifications of particular manufacturing environments. For instance:
- Automotive manufacturers use Digital Twins to simulate entire assembly lines and manage complex supply chains.
- Aerospace companies employ them to test critical components under extreme conditions.
- Pharmaceutical firms use twins to ensure compliance with stringent quality regulations and monitor sensitive production environments.
- This specificity ensures that every deployment is aligned with industry best practices and regulatory requirements.
Integration with Existing Systems
Transitioning to Digital Twin technology doesn’t mean starting from scratch. Leading service providers in the U.S. offer solutions that integrate seamlessly with existing ERP systems, MES platforms, and SCADA architectures. This ensures that companies can maximize their current investments while adopting future-ready technology.
Moreover, modular solutions allow manufacturers to scale gradually—starting with a single machine or process and expanding as needed.
Cloud and Edge Computing Capabilities
To handle the vast amounts of data generated, many Digital Twin services leverage cloud and edge computing. While cloud platforms offer scalable storage and analytics, edge computing allows real-time data processing closer to the source. This hybrid approach ensures low latency, high responsiveness, and robust data security—key concerns for U.S. manufacturers handling sensitive intellectual property.
Challenges to Adoption and How to Overcome Them
Despite the numerous advantages, some manufacturers hesitate to adopt Digital Twin solutions due to perceived barriers. These may include cost concerns, data privacy issues, or a lack of internal expertise.
Nevertheless, these challenges are increasingly manageable. Government incentives, such as the Manufacturing Extension Partnership (MEP) Program, provide support and funding for technology adoption. Additionally, many service providers now offer subscription-based models or pilot programs, reducing upfront costs.
Training and change management are also critical. Companies that invest in workforce upskilling and cross-functional collaboration are better positioned to reap the full benefits of Digital Twin technology.
The Prospect of Manufacturing Efficiency Through Digital Twins
Looking ahead, the role of Digital Twins in manufacturing is only expected to grow. As AI becomes more advanced and 5G connectivity becomes widespread, Digital Twins will evolve into even more sophisticated systems—capable of autonomous decision-making, real-time collaboration, and closed-loop optimization.
In particular, we can expect to see their integration into smart factories, where machines, robots, and humans work in unison, guided by predictive analytics and intelligent automation. In this environment, inefficiency becomes an exception rather than the rule.
For American manufacturers striving to maintain global leadership, embracing Digital Twin services is a strategic imperative. Those who do so today will not only streamline their operations but also position themselves for sustainable, long-term success.
Conclusion
To summarize, Digital Twin technology offers a paradigm shift in how manufacturing operations are managed, optimized, and scaled. With services specifically designed for the American manufacturing ecosystem, companies can overcome operational challenges, unlock new efficiencies, and outpace the competition.
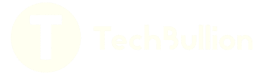