Metal Inert Gas (MIG) welding technique was first developed in 1948. H.E. Kennedy from Battelle Memorial Institute invented this welding process. In contrast, Arthur Bernard invented Flux-cored arc welding in 1957.
Mig welding is easier to learn and apply on different projects. Especially in diy projects mig welding has no better competitor. Flux core is similar to mig welding except for the use of gas. Mig uses gas but flux core uses special type of flux electrode that work as decontaminator- says Maidul Islam of weldingintro.com.
We must know the differences between mig welding and flux core welding to understand which one is the best.
In this article we will cover how mig and flux core welding differ and which one you should choose.
Differences between MIG and Flux Core
The followings are the most important attributes that set up these two welding techniques.
01. Shielding gas
MIG welders need a shielding gas to prevent exposure to the molten weld pool and produce faster and cleaner welds.
Carbon dioxide, argon, oxygen, and helium are the most common gas used in MIG welding.
In contrast, flux core welders don’t need any external shielding gas as it produces a particular gas internally to protect the weld pool
02. Polarity
MIG welding machines use DC electrode positive (DCEP) or reverse polarity to generate more heat at the workplace and decrease the chance of lack-of-fusion defects.
DC electrode negative or straight polarity is used in flux core welding. It is necessary to alter the terminal to negative when using the flux core welding technique.
03. Indoor Vs. Outdoor
MIG welding technique is only suitable for indoor usage because the wind o rain can interfere with the shielding gas and affect your welding results.
On the other hand, the flux core welding technique is a better choice for outdoor purposes to ensure adequate ventilation and allow chemicals and fumes to spread quickly.
04. Wire Construction
You can use three types of welding wires for MIG welding: solid, stainless steel, and aluminum.
Solid wires are pretty versatile. You can use it in any position. This makes it ideal for beginners.
Stainless steel wires can provide an appealing and rigid finish, whereas aluminum wires are perfect for saving space.
On the contrary, people generally use self-shielded flux-cored wires for flux-core welding.
It has a special flux material coating that includes deoxidizers. This provides shielding gas to protect the weld and improve the weld quality.
05. Strength
MIG and flux core welding provide strong welding joints if you correctly join the metal.
However, flux-core welding can be a bit stronger in some particular situations, as flux-cored electrodes produce slag to safeguard the weld from contaminants and impurities.
06. Penetration
Flux Core welding usually produces deeper penetration than MIG welding, especially for welding cast iron, ferrous metals, or thicker metals.
However, the welding current will play a vital role in the penetration depth and deposition rate.
You can’t use too much heat; it may affect the welding result negatively.
Pros & cons of mig and flux core welding
Pros of MIG Welding
- MIG welding is a versatile technique allowing welders to weld various iron, magnesium, copper, nickel, silicon, bronze, and other alloys.
- This welding process works fast. Hence, you can achieve reduced lead times. It will decrease your production costs too.
- Learning MIG welding is pretty simple and straightforward. This makes it beginner-friendly. You can be a good MIG welder within 6-12 months.
- MIG welder can generate high-quality welds with minimal defects and metal contamination. It can be a practical choice for thicker metals as the wire is continuously fed.
Cons of MIG Welding
- MIG welding is a bit expensive due to its expensive equipment, wire electrodes, and gas cost.
- The excessive heat input of MIG welding may lead to undesirable open holes and cross-sectional thickness of the base metal.
Pros Of Flux Core Welding
- Flux core welding is pretty portable due to its lightweight construction. More importantly, it does require an external shielding gas. Welders can use it in hard-to-reach areas.
- Flux core welders contain flux materials that include deoxidizers. It can effortlessly remove rust from the metal surface by undergoing chemical reactions during welding.
- You can use this welding technique outdoors, in windy conditions, and even in harsh weather conditions, as there is no external shielding gas to set up.
- Flux core welding is an energy and cost-saving option due to its no external shielding gas, higher welding speed and deposition rates, and fewer consumable requirements.
Cons of Flux Core Welding
- Incorrect weld settings, poor electrode settings, and incomplete fusion of flux core welding are more likely to produce bead irregularities, spatter, and slag inclusions.
- Flux core welding is a bit dirty as it produces a lot of gas and slag.
Which One Is Better, MIG Or Flux Core?
MIG and Flux Core welding can produce good-quality and strong welds when used correctly.
But the Flux Core welding technique is better for thicker materials due to its increased heat output. It is best suited for outside jobs.
On the contrary, the MIG welding process is the best choice for thinner materials to avoid burning the metal. It is a better option for indoor work.
Last Words
Both MIG and flux core welding are popular welding techniques. They have their own benefits and drawbacks.
MIG welding is faster and more precise, while flux core welding offers deeper penetration.
Before choosing a particular option, you must consider your project requirements and choose a specific the best welding option.
Hopefully, you got a clear overview of the difference between MIG and flux core welding.
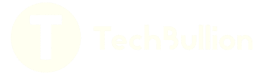