The field of electronics and instrumentation engineering serves as a cornerstone for innovation and operational integrity across numerous modern sectors. This ranges from the high-reliability demands of military and medical applications to the complex systems powering energy infrastructure and advanced automotive technologies. Within these critical domains, engineers capable of navigating intricate technical challenges, ensuring system robustness, and tailoring solutions to precise, demanding specifications are indispensable.
Dhriti Chakraborty brings over a decade of expertise to engineering projects where precision and reliability are non-negotiable. Her career spans the successful design and commissioning of critical infrastructure, including a water treatment plant for the Steel Authority of India Limited (SAIL), one of India’s major public sector enterprises.
Her work extends beyond national borders, contributing to the development of sophisticated components and systems for global markets. Through each phase of her career, Chakraborty has consistently demonstrated engineering excellence in high-stakes environments, earning recognition for her ability to deliver robust, efficient solutions in complex technical domains.
Holding both a diploma in Instrumentation Engineering and a subsequent degree in Electronics and Instrumentation Engineering, complemented by training from Instrumentation Limited, her foundation is built on rigorous technical knowledge.
This expertise has been applied across a diverse range of projects, including earthquake simulators, micro modular programmable logic controllers (PLCs), human-machine interfaces (HMIs), automotive infotainment systems leveraging Autosar standards, and the development of custom and standard passive components for mission-critical use in military, energy, and healthcare sectors.
Chakraborty’s contributions extend beyond pure design and development. Her work encompasses vital market research and new product development initiatives, ensuring that engineered solutions align with evolving industry needs and technological advancements. In her global role as an Application Engineer, she serves as a key technical point of contact across the Americas, Canada, Mexico, and EMEA, providing crucial support for critical applications.
This position involves extensive technical training delivery to manufacturing representatives, distributors, and the broader engineering community across diverse verticals like energy, military, medical, industrial, and electric vehicles (EV).
Furthermore, she plays an integral role in creating essential technical documentation, including application notes, white papers, and datasheets, and actively supports sales and marketing efforts through technical expertise and product demonstrations.
This unique combination of deep technical skill and effective global communication highlights an ability to bridge the gap between complex engineering concepts and practical market application.
Navigating early challenges: The SAIL water treatment plant project
Embarking on her professional journey, Chakraborty was immediately immersed in the complexities of large-scale industrial engineering. Her initial role involved significant contributions to the design and commissioning of a water treatment plant for SAIL, India’s largest steel producer. This project presented a formidable learning ground, demanding the practical application of theoretical knowledge in a high-stakes environment.
“I started my career as a design engineer, and in the process, I learned various aspects of engineering and technology,” Chakraborty recalls. “Starting as a hands-on technical engineer, I gained in-depth knowledge of core applications, including the architecture, the functionality, and the troubleshooting procedures.” The steel industry’s water requirements are substantial and complex, involving vast quantities of water for cooling, cleaning, and process use, while simultaneously generating effluents containing suspended solids, heavy metals, and other contaminants that necessitate effective treatment.
The primary engineering hurdles identified early in the SAIL project centered on the critical aspects of industrial water management. These included ensuring consistent water quality, mitigating the pervasive issues of scaling and corrosion within the plant’s systems, and optimizing for both energy and cost efficiency, factors crucial for the economic viability of large industrial operations.
“The main challenge with the design was to keep various aspects in mind, like managing water quality and consistency and dealing with scaling and corrosion energy and cost efficiency,” Chakraborty notes. “Handling the techno-commercial aspect was a challenge in such a large project.” Successfully addressing these interconnected issues required a holistic perspective, recognizing that factors like water quality directly influence scaling and corrosion rates, which in turn impact heat transfer efficiency and operational costs.
Balancing the technical specifications required to manage these challenges with the project’s budget and procurement constraints added another layer of complexity, demanding careful techno-commercial navigation from the outset.
Designing and commissioning for industrial efficiency and scalability
The process of commissioning an industrial plant is a critical phase that ensures the transition from construction to operation is seamless and successful. It serves as a methodical verification that all systems are not only installed correctly but also function according to the original design intent and meet the operational needs of the end-user.
“Commissioning of a plant is used to ensure that all process systems have been properly constructed, are operational, and are verified to perform according to the design intent and the user’s operational needs,” explains Chakraborty. “The main objective of commissioning is to confirm that the design intent of the components, the systems, and the plant as a whole is achieved.” This verification is not merely a final check; effective commissioning relies heavily on meticulous planning initiated during the earliest design stages.
Incorporating considerations for operability and maintainability into the design itself is crucial, allowing these aspects to be validated during commissioning and preventing the creation of systems that become burdensome and costly to operate over their lifecycle. In tackling the SAIL water treatment plant, Chakraborty’s approach prioritized efficiency and scalability, essential attributes for large-scale industrial facilities that may face changing demands over time.
The design incorporated several key strategies to meet these objectives. “To ensure efficiency and scalability for industrial water treatment, we have designed solutions with modular components that can be easily scaled up or down to meet changing demands, automation system to optimize treatment processes monitor performance and respond to change in flow rates, and adaptable technologies to handle varying water quality and flow rates, while also considering energy efficiency and cost-effectiveness,” she details.
The use of modular components provides inherent flexibility, allowing capacity adjustments without complete system overhauls. Automation plays a vital role in optimizing treatment processes in real-time, monitoring key performance indicators, and adapting to fluctuations in water characteristics or plant throughput.
Furthermore, selecting adaptable treatment technologies ensures the system can effectively handle the variable water quality often encountered in industrial settings, all while keeping energy consumption and operational costs under control.
This foresight in design, focusing on lifecycle performance and maintainability validated through commissioning, is indicative of a mature engineering approach aimed at long-term operational success.
Fostering collaboration and learning in complex engineering projects
Large-scale industrial projects, like the SAIL water treatment plant, rarely occur in isolation. They typically involve a network of specialized teams, vendors, and consultants working in concert to achieve the overall objective. The SAIL project exemplified this collaborative model.
“The scope of the project was distributed among various vendors and design engineering companies,” Chakraborty notes. “As a fresher, I got a great opportunity to collaborate and cross learn with consultants from various organizations.” This distribution of work necessitates robust coordination mechanisms and clear communication channels to ensure all components integrate seamlessly and progress stays on track.
For Chakraborty, entering this multi-stakeholder environment early in her career provided invaluable experience beyond the purely technical aspects of design engineering. The project structure facilitated interaction and knowledge sharing among the diverse teams involved.
“There were regular meetings and catch-ups every week on the progress from individual areas,” she mentions. These interactions offered a platform for cross-learning, allowing junior engineers like Chakraborty at the time to gain insights from experienced consultants and specialists from different organizations.
Such environments implicitly foster the development of critical soft skills – communication, coordination, negotiation, and inter-organizational collaboration – which are essential for navigating complex technical projects and are particularly relevant for roles involving extensive interaction with customers, sales teams, and global partners, such as the application engineer position Chakraborty holds today.
Defining technical specifications for mission-critical applications
Moving beyond large infrastructure projects, Chakraborty’s expertise extends to defining requirements for components and systems in sectors where failure can have severe consequences, such as military, energy, and medical applications. Determining the most critical technical specifications in these high-stakes environments demands a rigorous and comprehensive methodology.
“In high-stakes industries like military and energy, determining the most important technical specifications for mission-critical applications requires a holistic approach that prioritizes reliability, safety, and performance, while also considering the potential impact of failures,” Chakraborty states.
This approach acknowledges that component or system failure in these contexts can jeopardize missions, endanger lives, or lead to significant financial and environmental damage.
The process of defining critical specifications involves a series of intentional, collaborative steps to ensure the final engineered solution aligns seamlessly with the application’s requirements. Chakraborty describes this approach as beginning with a deep understanding of the customer’s application, followed by selecting the appropriate product – whether standard or custom. This is supported by an initial technical discussion with the customer, then detailed coordination with internal teams across product development, manufacturing, and quality assurance to ensure all technical specifications, safety requirements, and industry standards are thoroughly met.
This involves a deep dive into the specific operational context, followed by a crucial decision point: whether a standard, off-the-shelf component can meet the requirements or if a custom-designed solution is necessary. This decision weighs the benefits of proven, readily available standard parts against the potential performance or integration advantages of a tailored solution.
Subsequent discussions with the customer refine the requirements, while internal collaboration with product development, manufacturing, and quality assurance teams ensures that the chosen solution can be reliably produced and meets all relevant technical benchmarks and stringent industry-specific safety and compliance standards (e.g., military specifications).
Adherence to standards in critical application design
The decision-making process for critical applications often involves navigating the line between leveraging established practices and innovating for specific needs. However, when it comes to fundamental engineering principles and safety standards, the path is clear. Tailoring a design for a critical application rarely permits significant deviation from established engineering practices.
“It’s not possible to deviate from standard engineering practice when tailoring a design for a critical application, as it might cause a bigger issue in breaking the entire application,” Chakraborty emphasizes. The risks associated with such deviations are simply too high in fields where system integrity is non-negotiable.
Departing from proven standards introduces unacceptable levels of uncertainty and potential vulnerabilities. The consequences can be severe and far-reaching.
“It can lead to various negative consequences, including compromised safety, reduced reliability, and potential legal issues, as well as impacting the professional reputation of the organization,” she warns. This underscores a core tenet of engineering for critical systems: prioritizing safety and reliability through adherence to rigorously tested and validated standards.
This approach reflects a deeply ingrained principle of risk aversion, where the predictability and trustworthiness achieved through standard practices are valued above potentially novel but unproven design pathways.
It is a philosophy driven by both ethical responsibility and the practical necessity of ensuring dependable performance in applications where failure is not an option.
The pivotal role of materials selection in demanding environments
The performance and longevity of any engineered component, particularly one destined for a demanding environment, are fundamentally tied to the materials from which it is constructed. In sectors like military, aerospace, energy, and even advanced automotive applications, components are routinely subjected to extreme temperatures, high vibration, mechanical shock, corrosive substances, or radiation.
Consequently, the process of selecting materials is not a secondary consideration but a critical design decision with far-reaching implications.
“In designing components for demanding environments, materials selection is paramount as it directly impacts performance, durability, and overall lifespan, requiring a careful balance of properties like strength, resistance to environmental factors, and cost-effectiveness,” Chakraborty explains. The selection process involves a multifaceted evaluation against stringent criteria tailored to the specific application’s challenges.
Key considerations include ensuring the material possesses the necessary mechanical strength and toughness to withstand operational stresses. “Materials must be able to withstand stress, impact, and fatigue, ensuring the component’s structural integrity,” Chakraborty highlights.
Equally important is resistance to environmental degradation: “Components in demanding environments (e.g., harsh chemicals, extreme temperatures, radiation) require materials with excellent resistance to corrosion, oxidation, and degradation.” Beyond these primary factors, considerations extend to wear resistance, overall durability influencing maintenance cycles and lifespan, the ease and cost-effectiveness of manufacturing the component from the chosen material, sustainability aspects related to resource consumption, and strict adherence to relevant industry standards and safety regulations.
The careful balancing of these properties, understanding how factors like thermal conductivity or resistance to specific chemicals will affect the component in its intended use case, demonstrates that a strong grasp of materials science is indispensable for engineers designing reliable solutions for harsh conditions.
Ensuring reliability: Validating solutions for extreme conditions
Designing for reliability is only part of the equation; validating that the designed solution will indeed perform reliably under the anticipated, and often unpredictable, conditions is equally crucial. This requires a structured approach to identifying potential weaknesses and verifying the design’s robustness through targeted testing. Chakraborty utilizes Design Failure Mode Effect Analysis (DFMEA) as a cornerstone of this validation strategy.
DFMEA is a systematic, proactive methodology employed during the design phase to anticipate potential failure modes, their causes, and their effects on the system. “The most effective ways of finding out Testing needs for a design are through developing a Design Failure Mode Effect Analysis,” she states. “The document helps us list all the possible failure modes in various aspects of product performance and then strategize [with] different types of tests to evaluate those failure modes.”
The power of DFMEA lies in its ability to guide the development of an efficient and effective testing plan. By systematically breaking down the design and considering how each element might fail, engineers can pinpoint areas of highest risk.
“By listing down multiple causes from one single failure mode, multiple sources of failure can be discovered, and tests can be designed to detect them in the design and development process,” Chakraborty elaborates. This analytical process ensures that validation testing is not a scattergun effort but is strategically focused on verifying the design’s resilience against the most likely and most critical potential failure mechanisms identified during the DFMEA.
This structured approach, linking potential design flaws directly to specific validation tests, is essential for building confidence in the reliability of custom-engineered solutions intended for operation under extreme or unpredictable conditions.
A commitment to excellence: Driving efficiency and cost reduction
Throughout her career, Chakraborty has demonstrated a consistent commitment to engineering excellence, particularly in projects demanding high reliability and optimal performance within stringent constraints. One project she highlights exemplifies this commitment, involving sophisticated clients in the demanding medical and space industries.
“My leadership in high-stakes projects has led to significant advancements in efficiency and cost reduction for critical applications,” she notes. “One notable example involved a leading medical and space industry client, where I spearheaded a specification and design upgrade that resulted in a 30% cost reduction while enhancing overall performance.” Achieving such a substantial cost reduction while simultaneously improving performance underscores a strategic and technically adept approach to problem-solving.
The success of this project stemmed from a targeted design intervention: replacing multiple standard chip resistors with a single, custom-designed passive component. This custom solution was meticulously engineered not only to consolidate functionality but also to optimize for production costs without compromising the rigorous quality standards of the medical and space sectors.
Chakraborty elaborates on the contributing factors: “This cost reduction resulted from the use of appropriate design, the right selection of materials, application-oriented operating procedures, quality checks, and surveillance at different stages of manufacturing.” This highlights the integration of multiple engineering disciplines – clever design, astute materials selection, process optimization, and rigorous quality control.
She further adds, “Through mock testing, data analysis, and stringent quality control, I successfully guided the project from concept to production, demonstrating the crucial role of technical leadership in delivering innovative and commercially viable solutions.”
This project serves as a compelling case study in value engineering, where intelligent customization delivered superior results compared to relying solely on standard components, showcasing an ability to identify and execute opportunities that yield both technical and commercial benefits.
Components designed for such demanding applications often need to meet stringent reliability standards like AEC-Q200, particularly relevant given Chakraborty’s involvement in automotive and other critical sectors requiring certified components.
Successfully navigating projects that require components meeting such demanding criteria further illustrates the level of engineering rigor involved.
Chakraborty’s career exemplifies the impact of dedicated engineering expertise applied to critical systems across a spectrum of demanding industries. Her journey, beginning with foundational experiences on large-scale projects like the SAIL water treatment plant, has evolved into a global role shaping the development and application of advanced electronic and instrumentation solutions.
Possessing a deep understanding of core engineering principles, she adeptly navigates complex technical challenges, ensuring system reliability through meticulous materials selection, proactive failure analysis using tools like DFMEA, and adherence to stringent industry standards.
Her work demonstrates a unique ability to balance the benefits of standardization with the strategic advantages of customization, consistently delivering solutions that enhance performance and efficiency for critical applications in sectors ranging from energy and industrial automation to military, medical, and automotive.
Through her technical leadership, collaborative approach, and commitment to sharing knowledge via training and documentation, Chakraborty continues to make significant contributions to engineering excellence on an international scale.
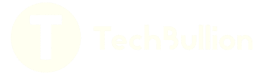