As the world strides toward an increasingly automated future, the robustness and reliability of automation systems become critical. These systems must continue to operate effectively even under adverse conditions or inevitable failures. This is where fault-tolerant process measurement technology comes into play.
Understanding Fault-Tolerance
Fault-tolerant process measurement technology refers to systems designed to ensure the smooth operation of automated processes despite potential faults or failures. It involves creating a redundant and reliable system architecture to prevent faults from leading to significant system degradation or complete failure.
Fault Tolerance and Automation
The importance of fault tolerance in automation systems cannot be overstated. As industries increasingly rely on automated systems for their operations, any system downtime could have severe consequences, including lost productivity, decreased efficiency, increased costs, and potentially hazardous situations.
Developing Fault-Tolerant Technology
Developing fault-tolerant process measurement technology involves several key steps. These include identifying potential points of failure, creating redundant systems, implementing effective fault detection mechanisms, and developing efficient recovery procedures.
Identifying Potential Points of Failure
The first step in developing fault-tolerant process measurement technology is identifying potential points of failure in the automation systems. This requires a thorough understanding of the system architecture and its operation.
Creating Redundant Systems
After identifying potential points of failure, the next step is to create redundant systems that can take over if the primary system fails. Redundancy can be achieved in several ways, including hardware redundancy (duplicate physical components), software redundancy (multiple software instances), and information redundancy (extra bits to detect and correct errors).
Implementing Effective Fault Detection Mechanisms
Implementing effective fault detection mechanisms is a critical part of developing fault-tolerant process measurement technology. These mechanisms monitor the system’s operation and trigger an alarm or initiate a recovery procedure if a fault is detected.
Using Sensors to Measure Security
As central components of any automation system, sensors, especially those from renowned suppliers like Endress+Hauser, play a critical role in process measurement technology. The range of flow measurement parts and sensors available through Endress+Hauser provide the necessary data for monitoring, control, and fault detection, acting as the eyes and ears of the system. Without reliable sensor technology from trusted suppliers, achieving fault tolerance would be impossible.
Importance of Sensors in Measurement Technology
Sensors are responsible for collecting real-time data about various process parameters, such as temperature, pressure, flow rate, and more. This data is integral to system operation and control. In the context of fault-tolerant process measurement technology, sensors are also vital for detecting faults. They can monitor system performance and identify deviations from normal operation, signaling potential faults or failures.
Sensor Redundancy for Fault Tolerance
Just like other components of an automation system, sensors can also fail. Therefore, incorporating redundancy at the sensor level is a key aspect of developing fault-tolerant systems. Multiple sensors monitoring the same process parameter can ensure continuous and accurate data collection, even if one or more sensors fail.
Creating Efficient Recovery Procedures
Finally, developing efficient recovery procedures is vital. These procedures determine how the system responds to a detected fault, including switching to a redundant system, isolating the faulty component, or attempting to correct the error.
Securing Automation Systems
Implementing fault-tolerant process measurement technology can significantly improve the security and reliability of automation systems. By anticipating potential failures and preparing for them, companies can minimize system downtime, enhance efficiency, reduce costs, and ensure safer operations.
Real-time Fault Tolerance for Increased Security
Real-time fault tolerance plays a crucial role in securing automation systems. By detecting and addressing faults in real time, the system can maintain its operation with minimal disruption. This is particularly important for industries where system downtime can have severe consequences, such as the manufacturing and energy sectors.
Enhanced System Resilience through Redundancy
Redundancy enhances system resilience, making it more resistant to faults and failures. By having backup systems ready to take over at a moment’s notice, companies can ensure that their operations continue smoothly even in the event of a system failure.
Reducing Costs with Fault-Tolerant Systems
By reducing system downtime, fault-tolerant process measurement technology can help companies save significantly on costs associated with failures, such as lost productivity, repair costs, and potential penalties for service disruptions.
Fault-Proofing Automotive Systems
Developing fault-tolerant process measurement technology is a vital step in securing automation systems. By identifying potential points of failure, creating redundant systems, implementing effective fault detection mechanisms, and developing efficient recovery procedures, companies can ensure the reliable operation of their automation systems, thereby enhancing efficiency, reducing costs, and ensuring safer operations. As we move towards a future where automation is increasingly prevalent, the importance of fault-tolerant process measurement technology cannot be overstated.
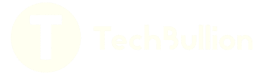