Introduction:
Design for Ease of Manufacture (DFEM) is a design philosophy that focuses on creating products that are optimized for efficient and cost-effective manufacturing. By considering manufacturability early in the design process, companies can minimize production challenges, reduce costs, and enhance overall quality. This article explores the concept of Design for Ease of Manufacture and its significance in streamlining production processes.
The Importance of Design for Ease of Manufacture:
Design for Ease of Manufacture plays a vital role in ensuring that products can be manufactured efficiently and effectively. By considering manufacturing requirements during the design phase, companies can:
- a) Reduce Production Costs: Optimized designs minimize material waste, streamline assembly processes, and decrease the need for costly rework. By designing products with ease of manufacture in mind, companies can achieve significant cost savings throughout the production cycle.
- b) Improve Production Efficiency: DFEM enables manufacturers to identify and address potential manufacturing bottlenecks early in the design process. By optimizing designs for assembly, machining, and other manufacturing operations, companies can streamline production, reduce cycle times, and increase throughput.
- c) Enhance Product Quality: Designing for ease of manufacture ensures that products are manufactured consistently and meet the required quality standards. By considering factors such as tolerance limits, material selection, and assembly techniques, companies can reduce the risk of defects and improve overall product quality.
- d) Accelerate Time-to-Market: By incorporating ease of manufacture principles into the design process, companies can minimize design iterations, production delays, and time-consuming rework. This allows for faster time-to-market, giving companies a competitive advantage in today’s rapidly evolving business landscape.
Principles of Design for Ease of Manufacture:
- a) Simplification and Standardization: Simplifying product designs and standardizing components wherever possible can significantly enhance ease of manufacture. By reducing the number of unique parts, companies can streamline the supply chain, optimize inventory management, and simplify assembly processes.
- b) Designing for Scalability: Considering scalability in the design phase allows for efficient production as demand increases. Modular designs and standardized interfaces enable easy integration of additional components or features, accommodating future product variations and customization.
- c) Designing for Assembly: Designing products with ease of assembly in mind can significantly reduce manufacturing time and costs. Using techniques such as Design for Assembly (DFA) and Design for Manufacturability (DFM), companies can minimize the number of assembly steps, facilitate automation, and improve overall assembly efficiency.
- d) Material Selection and Compatibility: Choosing appropriate materials that are readily available and compatible with manufacturing processes is crucial for ease of manufacture. Considering factors such as material properties, availability, cost, and recyclability can optimize production efficiency and minimize waste.
- e) Tolerance Analysis: Conducting tolerance analysis helps ensure that parts fit together correctly during assembly. By designing products with appropriate tolerances, manufacturers can reduce the need for rework, scrap, and costly adjustments, improving overall manufacturing efficiency.
Leveraging Technology for Design for Ease of Manufacture:
- a) Computer-Aided Design (CAD): CAD tools allow designers to create and modify product designs in a virtual environment. By utilizing CAD software with built-in analysis capabilities, manufacturers can evaluate factors such as structural integrity, tolerances, and assembly feasibility, optimizing designs for ease of manufacture.
- b) Simulation and Virtual Prototyping: Using simulation software, manufacturers can analyze and optimize product designs before physical prototyping. Virtual prototyping allows for the identification of potential manufacturing challenges and enables design modifications to improve ease of manufacture.
- c) Additive Manufacturing (AM): Additive manufacturing technologies, such as 3D printing, offer unique opportunities for designing products with ease of manufacture in mind.
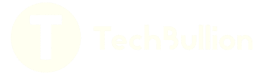