In a world increasingly driven by do-it-yourself projects and personalized products, the custom tool industry is booming. This is specifically true in case of custom saws which according to the reports are marking a significant growth. You might have contemplated purchasing, or perhaps already own a custom saw. Have you ever wondered how these specialized tools are made? Let us delve deeper into the fascinating journey of custom saw manufacturing by exploring the role of custom saw manufacturing companies.
The Importance of Custom Saws
Fundamentally, a saw is an indispensable tool for any kind of woodwork. However, what separates a great piece of work from a shoddy one is often the quality of tools used. A custom saw allows you to handle unique projects that necessitate particular cuts or require working with peculiar materials. Custom saws are designed precisely according to your needs which can elevate the efficiency and quality of your work.
Selecting the Raw Materials
All high-quality custom saws commence their journey in the form of raw materials. Typically, manufacturers take steel blanks that are specifically created for the purpose of making saw blades. Essentially, the choice of raw material has a significant impact on the quality, power, speed and life expectancy of the end product.
The Heat Treatment Process
Following selection and cleaning, the steel goes through heat treatment which enhances its strength and durability. This process involves heating and cooling cycles under regulated conditions to impart specific properties to the steel. This step plays a vital role in determining how well your custom saw will perform in the long run.
Crafting the Blade
Once heat-treated, these blanks are transformed into blades. The blade-making process varies based on the sort of saw being produced. For instance, circular saw blades are cut out using a laser, while band saw blades are created from long strips of metal.
Applying Carbide Tips
Most high-quality custom saws feature carbide-tipped teeth. Carbide, being harder and more durable than steel, allows the saw to maintain its sharpness longer and perform better when cutting through tough materials. The process of applying carbide tips is carried out under strict quality control to ensure they are perfectly aligned and attached.
Precision Grinding for Sharpness
Post the application of carbide tips, the blades undergo precision grinding. This process ensures the sharpness of the saw and gives the necessary shape to the blade teeth. The better grinding process results in a blade that cuts smoother and faster.
The Coating Process
To reduce friction and enhance durability, custom saw blades often receive a special coating. This might range from aluminium coating for added toughness or Teflon for its non-stick properties. The blades undergo multiple coating stages for maximum efficiency.
Customization According to Needs
This is where the “custom” aspect comes into play. Depending on your specific needs or design specifications, blades can be modified or personalized. This could involve adding extra teeth, designing a special tooth form, or even adjusting the size of the blade.
Quality Checks and Testing
Each product undergoes extensive quality checks before being shipped out. This often involves testing them under comparable circumstances as they would face in real-life usage. These checks ensure that all custom saws perform optimally and uphold their promise of quality.
The Packaging Process
Last, but not least, is the packaging of these precision-crafted tools. Manufacturers typically use reinforced packaging to protect them from any possible damage during transport. They also come along with detailed instructions for optimum use and care.
Regulatory Standards in Manufacturing
All custom saw manufacturers must adhere to regulatory standards. This ensures the quality and safety of their products. The regulations may vary from country to country, but they usually set the norms for materials used, manufacturing procedures, safety guidelines and more.
Growth Trend in Custom Saw Industry
With the rise in personal and professional demand for specialized tools, the custom saw industry is witnessing steady growth. As per reports, this niche market is forecasted to continue its upward trajectory in the coming years.
The Role of Technology
Advancements in technology have greatly streamlined the custom saw manufacturing process while maximizing precision. From computer-controlled laser cutters to advanced coating techniques, technology plays a pivotal role in this industry.
Sustainability Efforts
A growing trend in the custom saw industry is focus on sustainable manufacturing practices. This includes using recycled materials, creating energy-efficient designs or utilizing green packaging solutions.
Economic Impact
The custom saw industry not only contributes to the economic development by creating jobs but also aids other industries like construction and carpentry by providing high-quality tools.
In Conclusion
The journey of crafting a custom saw takes meticulous effort, precision and unwavering commitment to quality. Detailed processes involving material selection, heat treatment, blade crafting, grinding, coating are undertaken before a perfect tool reaches your workshop. The industry remains a testament to human ingenuity and craftsmanship as it continues to grow and contribute to various sectors.
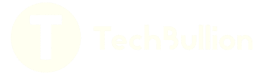