Industrial gearboxes are essential for many industries, including manufacturing, mining, and transportation. When it fails, it can cause significant disruptions to production and be costly to repair or replace. In some cases, these failures can even lead to safety hazards.
Even with the best preventive measures, these complications can still occur. That is why it is necessary to have a crisis management plan in place. Crisis management involves the strategic preparation, response, and recovery from unforeseen incidents. In the context of industrial gearbox failures, crisis management involves taking steps to minimize the impact of a complication on production, safety, and costs.
In this article, we will provide an overview of crisis management for industrial gearbox failures.
Identifying Gearbox Failure
They are intricate mechanical systems with numerous components, and their malfunctions can manifest in various ways. Common signs of malfunctioning include unusual noises, overheating, vibration, and decreased operational efficiency.
If you notice any of these symptoms, it is necessary to have it inspected by a qualified technician. Early detection and treatment of problems can help to prevent catastrophic failures.
To pinpoint the issue, comprehensive diagnostic techniques come into play. The American Journal of Transportation reported that an accident analysis revealed multiple factors contributing to gearbox malfunctioning. These include weak foundations, misalignment, overloading, insufficient contact, and occasionally suboptimal design practices.
This data underscores the importance of regular maintenance and alignment checks as critical components of early breakdown identification.
Immediate Response and Shutdown
When this breakdown occurs, it is crucial to take immediate action to minimize the impact on production, safety, and costs. The first step is to identify the problem and determine whether it can be safely operated until it can be repaired or replaced. If not possible, it is important to shut it down immediately.
Effective communication with stakeholders is critical, ensuring they’re updated on the situation and the actions that will be taken. Safety is of the utmost importance, given the potential risks posed by the failures. Consequently, isolating the equipment, displaying warnings, and providing protective gear for employees and others involved are essential safeguards.
As per research published by MDPI, when this assembly malfunctions, it directly impacts industrial output and daily routines. More severe instances can lead to personal injuries and substantial economic damages. Therefore, a quick shutdown and isolation of the faulty one prevent damage from spreading. It ensures safe inspection and assessment by maintenance personnel.
Diagnosing the Issue
The diagnostic process involves a combination of skilled observation, advanced technologies, and data analysis. Start with a visual inspection for signs of damage like cracks or loose components. Check fluid levels and inspect for leaks, which might indicate issues with seals or fittings.
Also, monitor the temperature and listen for unusual noises to indicate potential problems like overheating or component wear. Advanced diagnostic tools like vibration analysis, oil condition monitoring, and thermography have proven invaluable in accurately pinpointing the problem’s source.
They provide real-time data that aid maintenance teams in understanding the extent of the damage and planning effective repair strategies.
Decision-Making: Repair or Replacement
A crucial decision arises in a malfunctioning industrial gear assembly, i.e., repair or replace the gearbox. This choice is central to the effective crisis management of the breakdown and hinges on several factors.
Repairing is often a viable option, especially when the malfunction is detected early and the damage is not extensive. Gearbox repair can be cost-effective, as it preserves the existing equipment while addressing the specific issue. It involves disassembling the assembly, replacing damaged components, and conducting comprehensive testing and quality assurance.
Also, gearbox repair typically has a shorter turnaround time than replacement, minimizing downtime.
However, it’s crucial to make this decision based on a thorough assessment of its overall condition. If the damage is severe or if multiple components are compromised, repair may not be a sustainable long-term solution. In such instances, replacement is the wiser option for enhancing its reliability and longevity and reducing the risk of recurring defects.
Whatever the decision is, as per Cotta, when seeking gearbox power ratio upgrades, parts replacement, equipment recommissioning, etc., you must rely on professional expertise.
Gearbox Repair Procedures
The specific repair procedures will vary depending on the nature of the malfunctioning and the type of assembly. However, the typical repair process involves several key steps.
It commences with disassembling for a thorough inspection to identify the source of the glitch. After disassembly, components are meticulously cleaned to remove contaminants. Following this, all parts are inspected for damage or wear, with any such components being repaired or replaced as necessary. It is then reassembled using new or repaired parts, followed by rigorous testing to ensure proper functionality.
Once it has been repaired and tested, it can be reinstalled in the machine. It is important to follow the manufacturer’s instructions carefully when reinstalling it.
Emergency Spare Gearbox Implementation
A study featured in UniTrends revealed that among the Fortune 1000 companies surveyed, infrastructure failures resulted in an average hourly cost of $100,000. The research also found that the total annual cost of unplanned application downtime for these companies is $1.25 billion to $2.5 billion.
These significant financial implications underscore the critical importance of robust infrastructure and application reliability for large enterprises.
A breakdown or malfunction can lead to operational disruptions, causing decreased productivity and revenue loss. That’s where the implementation of an emergency spare gearbox system becomes crucial.
To bolster effective crisis management for industrial gear assembly failures, businesses often employ the strategy of emergency spare gearbox implementation. This proactive approach involves having a standby or spare ready for rapid deployment in case of a critical breakdown. Such preparedness can significantly reduce downtime and the associated financial losses.
The implementation of an emergency spare gear assembly system comprises critical steps. First, identify equipment and processes heavily dependent on gearboxes to prioritize deployment. Procure spare one of the same type, ensuring regular maintenance and testing for operational readiness. Develop a comprehensive deployment plan covering removal, installation, and testing procedures.
Lessons Learned and Preventive Measures
The aftermath of an industrial gear mishap can provide valuable insights to enhance crisis management. This data can also help minimize the risk of future failures. These lessons learned play a pivotal role in developing preventive measures that fortify the reliability of industrial processes.
This process involves key steps. Begin with a thorough root cause analysis to identify common culprits like insufficient lubrication, misalignment, and overloading. Generate detailed reports outlining root causes and operational impact.
Ensure knowledge transfer throughout the organization to empower staff in recognizing and mitigating issues. Develop and implement preventive measures, including regular maintenance, condition monitoring, and staff training, based on the identified root causes.
By systematically applying these lessons, businesses can significantly reduce the occurrence of failures.
Final Thoughts
Gearbox failures may be inevitable, but with the right approach, they need not be debilitating. By adhering to these well-defined steps and valuable insights, businesses can effectively navigate these challenges, fortifying their operations. This proactive approach helps minimize costly downtime and assures a resilient and prosperous industrial future.
Crisis management for industrial gear failures is not just a response but a proactive strategy for building stronger and more reliable industrial operations.
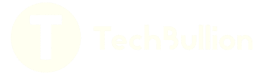