When it comes to maintaining equipment and machinery, solid data is crucial for effective planning. Solid data crucial for effective planning often comes from collecting operational information. Understanding what’s happening in your industry helps determine the state of your maintenance processes. As businesses consider upgrading equipment, having an outside perspective ensures informed decisions get made.
While consulting with experts offers an invaluable external perspective, the real payoff of machinery upgrades lies in their potential return on investment.
The Value of Outside Consultants
Working with consultants from outside your company allows an objective assessment of your machinery needs. They can evaluate factors like your capacity requirements, how employees use the equipment, and what resources you currently have. Consultants perform cost-benefit analyses to help determine where upgrades make the most sense.
The ROI of New Machinery
While consultants provide perspective, the real payoff of new equipment comes down to ROI. Studies show that predictive maintenance saves around 8-12% over preventive maintenance and up to 40% over reactive maintenance. This highlights the importance of investing in machinery with the latest tech – it can provide huge cost savings long-term.
Opting for equipment with built-in monitoring, predictive analytics, and smart alerts minimizes downtime and boosts productivity. Retrofitting existing machines with inexpensive sensor kits enables real-time tracking of temperature, vibration, and other metrics to catch problems early.
Predictive maintenance programs can save approximately 8-12% compared to preventive maintenance and up to 40% compared to reactive maintenance. This highlights the significant cost savings that come from investing in advanced technology. In addition to upgrades, partnering with companies offering comprehensive oil-based reliability services can further optimize uptime and ROI.
For smaller manufacturers, reducing dependence on outside maintenance providers is another benefit. By utilizing user-friendly sensor kits and monitoring dashboards, in-house teams can efficiently address most maintenance requirements in a cost-effective manner.
Evolving from reactive to preventive, and now predictive maintenance can provide exponential returns over equipment lifespan. Given the extensive data validating ROI, manufacturers must consider predictive capabilities when purchasing new machinery.
Digital Technologies for Optimal Outcomes
Studies reveal clear links between adopting digital tech and improved productivity. Predicting and preventing downtime is key for production growth. Real-time monitoring, predictive maintenance, and automation form a cost-saving trifecta. 3D printers help lower engineering expenses and accelerate market launch.
Maintenance and Equipment Longevity
Experts estimate maintenance costs range from 15-40% of total production outlays. Running equipment to failure could cost up to 10X more than a regular maintenance regimen. This shows ensuring longevity through consistent maintenance generates huge savings and prevents disruptions.
While maintenance extends equipment life, we can’t ignore the human side. The impact of new machinery on employee productivity is significant and worth examining.
The Overlooked Aspect – Training
Brand new equipment often involves a productivity learning curve for employees. It’s important to budget for training and expect some initial downtime.
Machinery Upgrades and Staff Productivity
While maintenance boosts longevity, people enable success. New equipment’s impact on productivity is profound. As automation handles repetitive, dangerous tasks, staff do higher-value work – raising satisfaction, skills, and retention. Employees have more time to innovate, improve processes, and tackle bottlenecks.
Upgraded machines that integrate with inventory and order systems provide employees with digital tools to enhance productivity. Paperless workflows, real-time data, and collaboration apps empower the workforce.
With advanced robotics, shop floor roles evolve into supervising automated processes. Diagnosing issues becomes a specialized skill that minimizes idle time. Workers embracing new technical skills enjoy rewarding career growth.
Smart glasses allow remote assistance during maintenance, expanding capabilities and improving fix rates. Staff gain mobility, speed, and on-demand knowledge.
So besides driving excellence, upgrades uplift employee experience and talents. Since people catalyze digital change, investing in change management and training extracts true value from technology.
Creating a Tech Roadmap for Long-Range Planning
It’s crucial to align business goals with tech solutions. Mapping current processes identifies gaps and opportunities to guide investments. Technology also enhances customer experiences.
Tailoring Machinery to Your Goals
Companies need a clear technology roadmap, tying objectives to specific upgrades. This focuses spend on goals like:
– Increasing capacity
– Improving quality
– Lowering operating costs
– Boosting productivity
– Accelerating market speed
Choosing the Right Suppliers
With countless specialized vendors online, how do you identify the best? Post-sale service, reputation, and references matter – beyond just price. Loyalty brings better warranties and service plans.
Key Supplier Considerations:
– Industry experience and reputation
– Equipment quality and service
– Safety and compliance record
– Competitive pricing
– Location proximity
Buying vs. Leasing: Considerations
Purchasing or leasing have pros and cons to weigh. Understand the financial implications and business impact.
Purchase – Higher initial payment, asset ownership, potential tax deductions, flexible upgrade timing
Lease – Lower starting cost, no asset ownership, operating expense, upgrades at end
Prioritizing Safety
Suppliers and owners both play a role in safeguarding staff. Safety rules also improve productivity.
Eco-Friendly Machines
Energy-efficient equipment reduces environmental impact and provides cost benefits. Responsible disposal matters more than ever.
In Closing
Upgrading machinery requires careful planning and preparation, from thoroughly assessing your equipment needs, to selecting the right suppliers, to weighing financing options. While the upfront costs of new machinery may seem high, the long-term benefits of increased productivity, lower operating costs, reduced downtime, and enhanced competitiveness far outweigh the initial investments over time.
Prioritizing critical factors such as worker safety, continuous training, and environmental impact throughout the upgrade process ensures that new equipment upgrades deliver genuine value and ROI to your business. With proper strategic guidance and consultation from industry experts, manufacturers can make smart, cost-effective machinery upgrade decisions tailored to their specific goals and constraints.
When implemented correctly, these upgrades can significantly enhance efficiency and capabilities, driving sustainable business growth and prosperity for years to come. However, none of this is possible without laying the necessary groundwork and planning ahead to ensure that your team and processes are fully prepared to leverage the next generation of equipment.
Frequently Asked Questions
How can a business determine the right time to upgrade its machinery?
Factors to consider include the age of the current machinery, frequency of breakdowns, and advancements in technology that could enhance productivity or reduce operating costs.
What are the long-term financial implications of leasing versus purchasing machinery?
While leasing offers lower initial payments, purchasing provides long-term ownership benefits like tax deductions as well as the potential to resell equipment. Weighing opportunity costs and total lifecycle costs is important.
How can businesses ensure the safety of new machinery while maximizing productivity?
Regular training, adherence to safety guidelines, and choosing suppliers with a strong safety record are crucial. Worker input helps customize equipment usage for optimal safety and efficiency.
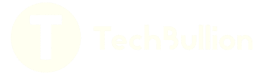