The Key Plastic Prototype Development Solutions
When thinking about plastic prototype creation options, it’s critical to assess the various methods and select the one that best satisfies the objectives of your project. Diverse techniques provide differing degrees of accuracy, economy, and fit for particular manufacturing needs. Let’s examine three popular techniques in more detail: injection molding, CNC machining, and 3D printing.
1. 3D Printing: Rapid and Versatile Prototyping
The creation of plastic prototypes has been transformed by additive manufacturing, commonly referred to as 3D printing. This method uses materials like nylon, plastic, or resin to create objects layer by layer. Because of its adaptability, it can be used to create intricate and complicated designs that would be difficult to accomplish using more conventional techniques.
- Speed and Flexibility:Β The speed of 3D printing is one of its main benefits. Prototypes can be quickly made with itβoften in a couple of hoursβdepending on the size and intricacy of the design. Its speed is perfect for iterative design revisions and testing, allowing teams to swiftly make necessary adjustments to prototypes.
- Cost-effectiveness:Β For short production runs or one-off prototypes, 3D printing is also a cost-effective option. Since it does not require costly molds, it is a cost-effective solution for early-stage prototype creation, particularly for startups or businesses with tight finances.
- Design Freedom:Β Because 3D printing is flexible, designers can experiment with intricate features, complicated geometries, and several design iterations without having to pay a hefty price. This makes it possible to explore design and exercise more creative flexibility during the prototype stage.
For prototypes that need to have precise surface finishes or great mechanical strength, 3D printing might not always be the ideal option. Other techniques, such as CNC machining, might be more suitable in these situations.
2. CNC Machining: Precision and Material Variety
Computer Numerical Control (CNC) machining is an additional useful method for developing plastic prototypes. It entails shaping, drilling, and cutting a solid block of plastic material into the required shape using equipment that is controlled by computers.
- Accuracy and Precision:Β CNC machining is renowned for its accuracy and capacity to produce prototypes that are incredibly exact. This is particularly crucial for tasks requiring close tolerances, like parts for aircraft or medical devices.
- Material Compatibility:Β Engineering-grade polymers such as ABS, polycarbonate, and PEEK are among the many materials that can be used with CNC machining. Because of its adaptability, engineers can work with materials that closely resemble the material used in final production, allowing for more precise testing of the mechanical properties of the prototype.
- Surface Finish:Β Prototypes that are CNC-machined usually have a smoother surface than those that are 3D-printed. Because of this, they are appropriate for uses where the prototype’s look and feel are crucial.
Generally speaking, CNC machining is more costly and time-consuming than 3D printing, particularly for really complex designs. However, it is a useful technique inΒ plastic prototype developmentΒ solutions because to its capacity to generate high-quality and useful prototypes.
3. Injection Molding: Ideal for Functional Prototypes
A common technique for creating plastic prototypes that work and closely resemble the finished product is injection molding. Melted plastic is injected into a mold during this procedure, and the material cools and hardens into the required shape.
- Scalability and Consistency:Β Prototypes that will eventually go into large production can benefit from injection molding’s great scalability. In order to verify the design’s performance at scale, it is essential that the process guarantee that every prototype produced is the same in terms of shape, size, and quality.
- Material Selection:Β Injection molding, like CNC machining, provides a multitude of material choices, including high-performance polymers. This facilitates testing the prototype under real-world circumstances and assessing its overall performance, chemical resistance, and durability.
- Cost and Time Considerations:Β Although making molds can be expensive at first, injection molding turns out to be more economical when producing greater numbers of prototypes. Furthermore, once the mold is made, the production cycle is really quick, which makes it possible to produce several prototypes quickly and effectively.
Although injection molding is a great option for functioning prototypes, the hefty upfront cost of mold development may make it impractical for early-stage prototyping. However, injection molding is frequently the greatest option for testing production-ready prototypes at later phases of development, when the design is almost finalized.
Aligning Design Goals with Production Methods
A key component in the creation of plastic prototypes is matching your design objectives with a suitable manufacturing technique. Every technique has advantages and disadvantages, whether it is injection molding, CNC machining, or 3D printing. The complexity of the design, the kind of material used, the level of precision required, and the project budget all play a role in selecting the best approach.
For instance, 3D printing is the most effective option if the objective is to rapidly iterate on a design concept. However, CNC machining can be a preferable option if the prototype calls for exact tolerances or materials with great strength. Finally, injection molding can produce production-quality prototypes if the design is prepared for functional testing in an actual setting.
Selecting the Right Materials for Your Prototype
Choosing the appropriate materials is another crucial element in the production of a good plastic prototype. The prototype’s strength, flexibility, durability, and look are all influenced by the material selection. It’s crucial toΒ select a plastic materialΒ that complements both the production process and the planned use of the prototype because every production technique has particular material compatibilities.
- Common materials used in 3D printing are PLA and ABS, which work well for visual objects but can not be very durable. For functional prototypes, more sophisticated materials like nylon or polycarbonate can be used.
- Given their strength and machinability, materials including acrylic, ABS, and polycarbonate are frequently used in CNC machining.
- Materials like nylon, polypropylene, and polyethylene are commonly utilized for injection molding because they provide excellent durability and versatility in a range of applications.
Optimizing Design for Manufacturability
When developing plastic prototypes, designing for manufacturability (DFM) is essential. DFM entails optimizing the design to guarantee that the selected production process can produce it effectively and economically. Minimizing intricate geometries, cutting down on material waste, and making sure the design is simple to reproduce in manufacturing are all important factors to take into account.
Draft angles, for instance, are used in injection molding designs to guarantee that the part may be readily removed from the mold without causing harm to the prototype. Similar to this, in CNC machining, reducing the number of tool changes through design simplification can minimize production costs.
Iterative Testing and Collaboration with Manufacturers
Iterative development is the key to creating an effective prototype. Achieving performance goals for the final product requires testing prototypes, getting feedback, and improving the design. Early problem detection through tight collaboration with manufacturers in the prototype development phase enables prompt design or production process modifications.
Transitioning from Prototype to Production
Prototyping to production is the following stage after the prototype has been extensively tested and improved. This entails completing the design, deciding on the best manufacturing technique, and increasing production volume. It will be easier to get from prototype to full-scale manufacture if production-grade materials and methods are used in its development.
Conclusion
The key to developing successful plastic prototype development solutions is to link design goals, materials, and manufacturability with the appropriate technology, be it injection molding, CNC machining, or 3D printing. By working with manufacturers and doing iterative testing, organizations may effectively move from prototype to production while reducing expenses and risks.
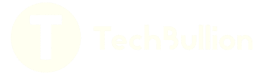