Hardness testing is an important evaluation in material science, assessing resistance to deformation and wear. Rockwell and Brinell hardness tests are among the most widely used methods in this field, each with distinct methodologies and suited to different types of materials. The Rockwell test is known for its efficiency and ease, measuring the depth of an indenter’s penetration under a major load after a minor initial load. This method is ideal for uniform materials and provides quick results with minimal surface preparation.
Conversely, the Brinell test is more suited to heterogeneous materials like castings and forgings. It uses a large-diameter ball indenter to determine surface resistance by the indentation’s diameter. This method is particularly useful for materials with coarse or uneven structures, providing data on hardness that reflects the material’s average properties over a large area.
In this article, we will discuss the specifics of each testing method, comparing their techniques, advantages, and ideal applications. By understanding the operational nuances and suitability for different materials, professionals can make informed decisions about the right method to use for their specific hardness testing needs.
Understanding the Rockwell and Brinell Hardness Tests
The Rockwell and Brinell hardness tests are fundamental tools in material science, each designed to measure material hardness but through distinctly different approaches and equipment. Understanding these methods is vital for selecting the appropriate test based on material properties and intended application.
Rockwell Hardness Test: The Rockwell test is known for its quick execution and minimal preparation of the material being tested. It measures the permanent indentation depth produced by a specific force on an indenter. The test begins with an initial minor load to establish a zero position, followed by a major load that creates an indentation. Once the major load is removed, only the minor load remains, and the indentation depth is measured. This method uses different indenters and loads depending on the material’s hardness, typically employing a diamond cone for harder materials and a steel ball for softer materials.
Brinell Hardness Test: In contrast, the Brinell test assesses the diameter of an indentation left by a ball indenter under a known load applied for a fixed time period. This method is particularly suited to materials with uneven or coarse structures. This is because it averages hardness over a larger area, making it less sensitive to specific surface irregularities. The Brinell test typically uses a larger indenter and applies a higher load than Rockwell, making it ideal for testing a greater range of material hardnesses.
Both methods have been standardized (Rockwell: ASTM E18, Brinell: ASTM E10), providing consistent testing protocols for different laboratories and applications. Each test provides a hardness value, but the scale and the unit of measurement differ: Rockwell results are given directly from the machine as a Rockwell hardness number (e.g., HRC, HRB), while Brinell results are calculated from the indentation measurements to give a Brinell hardness number (BHN).
Advantages and Limitations of Each Method
When choosing between Rockwell and Brinell hardness tests, it is extremely important to consider the advantages and limitations of each method to determine their suitability for specific materials and applications.
Advantages of the Rockwell Hardness Test
- Speed and Efficiency: The Rockwell test is much quicker than the Brinell test, typically taking only seconds to complete, which makes it highly efficient in high-volume testing situations.
- Immediate Results: Rockwell hardness values are directly displayed on the testing machine, facilitating rapid assessments without additional calculations or measurements.
- Minimal Material Impact: Due to the smaller indentation, the Rockwell test is less destructive to the test sample, a significant consideration when samples are scarce or expensive.
Limitations of the Rockwell Hardness Test
- Surface Sensitivity: While the Rockwell test is less sensitive to imperfections than Brinell, it can still be influenced by surface conditions and may not be suitable for materials with heterogeneous structures.
- Material Restrictions: The Rockwell test is not recommended for very hard or very soft materials, as the indenter may not produce accurate results in these extremes​.
Advantages of the Brinell Hardness Test
- Suitability for Coarse Materials: The Brinell test is ideal for rough or uneven materials such as castings and forgings because it averages the hardness over a larger area, providing a more representative measure of the material’s overall hardness.
- Flexibility: This method can be used on almost any type of metal, regardless of its structure, making it extremely useful for industrial applications​.
Limitations of the Brinell Hardness Test
- Time-Consuming and Destructive: The Brinell test is slower and more invasive, often leaving a large indentation that may not be acceptable for finished products or smaller samples.
- Complex Measurement: Unlike the Rockwell test, Brinell hardness values require careful measurement of the indentation diameter and subsequent calculation, which can introduce errors if not done precisely.
Making the Right Choice: Factors to Consider
Selecting the right hardness testing method – Rockwell or Brinell – depends on many factors including material type, required precision, and the specific application. Also, it must be mentioned that both methods require advanced, specialized equipment: Brinell hardness testers and Rockwell hardness testers. Each type of equipment is designed to meet the unique demands of its respective testing method.
Importance of Advanced Equipment: Modern advancements in testing equipment greatly enhance hardness testing precision. Advanced Brinell and Rockwell hardness testers offer digital readouts, automated load applications, and improved optical systems for measuring indentations. These improvements facilitate quicker tests with higher accuracy and repeatability, which are necessary for maintaining quality control across manufacturing processes.
Choosing a Responsible Supplier: When acquiring hardness testing equipment, be sure to purchase it from a reputable and responsible company. A reliable supplier guarantees equipment that meets industry standards and provides comprehensive support, including calibration, maintenance, and training services. This support is essential to guarantee the equipment performs at its highest level and delivers precise measurements over its operational life.
Other Considerations for Selection: In deciding between the Brinell and Rockwell tests, consider the following:
- Material Hardness and Structure: Choose Brinell for heterogeneous and coarse materials, and Rockwell for uniform materials where minimal surface damage is preferable.
- Test Efficiency and Speed: Opt for Rockwell if speed is a critical factor and Brinell for applications where detailed, averaged hardness measurements are required.
- Sample Size and Condition: Rockwell may be better for smaller or finished products due to its non-destructive nature, whereas Brinell is suitable for larger raw samples.
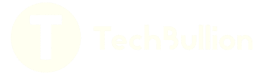