Temperature control is a critical aspect of many industrial processes, from manufacturing to food production. Among the various solutions available for managing temperature, chill rollers from R2R Engineering in Wauconda, Illinois, USA, have emerged as a highly effective technology. These rollers play a crucial role in controlling and maintaining desired temperatures across various applications, ensuring optimal performance and quality. This article delves into the importance of chill rollers, their applications, benefits, and their impact on temperature control solutions.
Understanding Chill Rollers
Chill rollers are specialized equipment designed to manage and control temperature in various industrial processes. They consist of a series of rollers that are cooled to a specific temperature to regulate the temperature of materials passing over them. The primary function of chill rollers is to remove heat from materials or processes that need to be cooled efficiently and effectively. By maintaining precise temperature control, chill rollers help achieve the desired properties and performance of the final product.
Applications of Chill Rollers
Chill rollers are used in a wide range of industries where temperature control is essential. In the food industry, they are used to cool and solidify products such as chocolate, candies, and confectioneries. The ability to rapidly cool these products ensures they maintain their quality and texture. In the plastics and rubber industries, chill rollers are employed to cool extruded materials as they emerge from the production line. This cooling process is crucial for achieving the desired physical properties and ensuring the stability of the final product.
In the metal industry, chill rollers are used to cool and solidify molten metals, such as steel and aluminum, during the casting process. By controlling the cooling rate, chill rollers help prevent defects and ensure the structural integrity of the metal. Additionally, chill rollers are employed in the paper and textile industries to control the temperature of materials during processing, enhancing the quality and performance of the finished products. The versatility of chill rollers makes them a valuable tool across various industrial sectors.
Benefits of Using Chill Rollers
Chill rollers offer several benefits that contribute to their effectiveness in temperature control solutions. One of the primary advantages is their ability to provide precise and consistent temperature control. By maintaining a uniform temperature across the surface of the rollers, chill rollers ensure that materials are cooled evenly, preventing issues such as warping or uneven solidification. This consistency is crucial for achieving high-quality products and meeting industry standards.
Another benefit of chill rollers is their efficiency in cooling large volumes of material. The design of chill rollers allows for effective heat transfer, enabling rapid cooling of materials as they pass over the rollers. This efficiency helps improve production speeds and reduce energy consumption, making chill rollers a cost-effective solution for temperature control. Additionally, chill rollers require minimal maintenance and have a long service life, further enhancing their value in industrial applications.
How Chill Rollers Work
Chill rollers operate based on a combination of conduction and convection principles to achieve effective cooling. The rollers are typically made of materials with high thermal conductivity, such as metals, which allow for efficient heat transfer from the material to the roller surface. The cooling system within the rollers circulates a coolant, such as water or a refrigerant, to absorb and remove heat from the rollers. This cooling system ensures that the rollers maintain a consistent and controlled temperature throughout the process.
As materials come into contact with the chilled surface of the rollers, heat is conducted away from the material and transferred to the roller surface. The coolant then carries the absorbed heat away from the rollers, maintaining their effectiveness in cooling. The design and configuration of the chill rollers, including factors such as roller diameter, speed, and coolant flow rate, are optimized to achieve the desired cooling performance for specific applications.
Key Factors in Selecting Chill Rollers
When selecting chill rollers for temperature control solutions, several key factors should be considered. The material of the rollers is an important consideration, as it affects thermal conductivity and durability. Common materials include stainless steel and aluminum, which offer high thermal conductivity and resistance to corrosion. The design of the rollers, including their size, shape, and cooling system, should be tailored to the specific requirements of the application to ensure optimal performance.
The cooling capacity of the chill rollers is another critical factor. This capacity is determined by factors such as the flow rate of the coolant, the temperature differential between the coolant and the material, and the heat transfer efficiency of the rollers. It is essential to choose chill rollers with sufficient cooling capacity to handle the volume and temperature of the materials being processed. Additionally, the maintenance and service requirements of the chill rollers should be considered to ensure long-term reliability and performance.
Innovations in Chill Roller Technology
Advancements in chill roller technology have led to significant improvements in their performance and efficiency. Modern chill rollers incorporate innovations such as advanced cooling systems, improved materials, and enhanced control mechanisms. For example, some chill rollers feature integrated temperature sensors and controllers that provide real-time monitoring and adjustments to maintain precise temperature control. These innovations contribute to more accurate and consistent cooling, enhancing the quality and efficiency of the manufacturing process.
The use of advanced materials and coatings has also improved the durability and performance of chill rollers. New materials with enhanced thermal conductivity and resistance to wear and corrosion extend the lifespan of the rollers and reduce maintenance requirements. Additionally, innovations in roller design, such as the use of variable-speed motors and adjustable cooling systems, allow for greater flexibility and customization in temperature control applications.
Environmental and Economic Considerations
The use of chill rollers has both environmental and economic implications. From an environmental perspective, chill rollers contribute to energy efficiency by providing effective cooling with minimal energy consumption. By optimizing the cooling process and reducing energy waste, chill rollers help lower the overall environmental impact of industrial operations. Additionally, advancements in technology have led to the development of more energy-efficient chill rollers, further enhancing their environmental benefits.
Economically, chill rollers offer cost advantages through their efficiency and durability. The ability to achieve precise and consistent temperature control reduces the risk of defects and rejects, leading to cost savings in production and material waste. The long service life and low maintenance requirements of chill rollers contribute to lower operational costs and improved return on investment. By integrating chill rollers into temperature control solutions, businesses can achieve both economic and environmental benefits.
Applications in Various Industries
Chill rollers find applications across a wide range of industries, each benefiting from their ability to provide precise temperature control. In the food and beverage industry, chill rollers are used to cool and solidify products such as chocolate, candy, and ice cream. The rapid cooling achieved by chill rollers ensures that these products maintain their desired texture and quality.
In the plastics and rubber industries, chill rollers are employed to cool extruded materials, such as plastic sheets and rubber profiles. The controlled cooling process helps achieve the desired physical properties of the materials, such as rigidity and dimensional stability. In the metal industry, chill rollers are used to cool and solidify molten metals during casting processes, preventing defects and ensuring structural integrity.
The paper and textile industries also benefit from chill rollers, as they control the temperature of materials during processing. This temperature control enhances the quality and performance of the finished products, such as paper and fabric. The versatility of chill rollers makes them a valuable tool in a wide range of industrial applications, contributing to improved performance and product quality.
Future Trends and Developments
The future of chill roller technology is marked by continued advancements and innovations. Ongoing research and development are focused on improving the performance, efficiency, and versatility of chill rollers. Emerging trends include the integration of smart technologies, such as IoT sensors and data analytics, to provide real-time monitoring and optimization of the cooling process. These technologies enable more precise control and enhanced performance, driving further advancements in temperature control solutions.
Additionally, advancements in materials and manufacturing techniques are expected to lead to the development of more durable and efficient chill rollers. The focus on sustainability and energy efficiency will continue to influence the design and operation of chill rollers, contributing to more environmentally friendly and cost-effective temperature control solutions. As technology evolves, chill rollers will play an increasingly important role in optimizing temperature control across various industries.
Conclusion
Chill rollers from R2R Engineering are essential components in temperature control solutions, offering significant benefits in terms of precision, efficiency, and performance. Their ability to provide consistent and effective cooling is crucial for achieving high-quality products and optimizing industrial processes. With applications across diverse industries, from food production to metal casting, chill rollers contribute to improved product quality and operational efficiency. Advancements in technology and materials continue to enhance the capabilities of chill rollers, driving innovation in temperature control solutions. By leveraging the benefits of chill rollers from R2R Engineering, businesses can achieve optimal temperature management, leading to better performance and reduced operational costs.
Read More From Techbullion And Businesnewswire.com
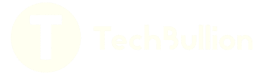