In the world of industrial development, the demand for materials that combine durability, flexibility, and efficiency is ceaseless. Cable Ladder, Chopped Strand Mat, and Fiberglass Sheets are three such materials that have become fundamental to building robust and efficient infrastructures across a variety of industries, from telecommunications to construction, and aerospace to automotive.
Cable Ladder: Essential for Organized Cabling
Overview of Cable Ladder
Cable Ladders are robust structures used primarily for managing and supporting cables in various industrial and commercial environments. They serve as the backbone for cable management systems, offering an organized pathway that ensures safe routing and accessibility. The primary function of a Cable Ladder system is to provide a strong, reliable support structure that can handle heavy loads of network cables, power cables, and communication wiring, reducing the risk of tangled wires and potential hazards. They facilitate better airflow and cooling, which is crucial for maintaining the integrity of cables over time.
Types and Specifications
Cable Ladders come in various types, each designed to meet specific environmental and load requirements:
- UL Classified Cable Runway: These cable ladders are tested and certified to meet strict safety standards set by Underwriters Laboratories. They are ideal for applications where safety is a paramount concern, such as in public buildings or electrical substations.
- Universal Cable Runway: Known for their versatility, these runways can be used in almost any installation. With features like variable support intervals and adaptable fittings, they are suitable for a wide range of environments from data centers to industrial facilities.
- TELCO-Style Cable Runway: Specifically designed for telecommunications rooms, these cable ladders feature specific stringer and cross member dimensions optimized for the unique needs of telecommunication cabling.
Installation and Maintenance
Installation Guidelines:
- Planning: Before installation, plan the layout carefully to ensure that the Cable Ladder will serve its purpose without interfering with other infrastructure components.
- Mounting: Securely mount the Cable Ladder to the floor, wall, or ceiling with appropriate fittings. Ensure that all joints and connections are tightened and that the ladder is level and stable.
- Integration: Integrate with existing cable management systems, ensuring that cables are evenly distributed along the Cable Ladder to avoid overloading any section.
Chopped Strand Mat: Versatile Composite Material
Introduction to Chopped Strand Mats
Chopped Strand Mats (CSM) are non-woven materials made from randomly distributed glass fibers that are held together by a resin binder. These mats are commonly used in the composites industry due to their ease of handling and ability to conform to complex shapes. The random fiber orientation provides uniform strength and stiffness in all directions, making CSM an ideal base material for a variety of composite products. Typically used in processes such as hand lay-up and spray-up molding, Chopped Strand Mats are a fundamental component in the manufacture of products ranging from boat hulls and automotive components to water tanks and roofing.
Product Range and Applications
Chopped Strand Mats are available in a range of weights, typically measured in ounces per square foot (oz/ft²), with common weights including .75 OZ, 1.5 OZ, 2 OZ, and 3 OZ. Each weight category serves specific applications and processing techniques:
- .75 OZ Mats: Often used for detailed work or in layers for creating complex curves without adding significant weight or thickness.
- 1.5 OZ and 2 OZ Mats: Popular for general-purpose applications, offering a balance between strength and flexibility. Ideal for automotive parts and sports equipment.
- 3 OZ Mats: Best suited for larger, more robust applications requiring higher structural integrity, such as in boat hulls and large containers.
Advantages and Handling Techniques
Advantages:
- Versatility: Chopped Strand Mats can be used in various manufacturing processes and for a wide range of products due to their easy handling and adaptability.
- Uniform Properties: The random orientation of the fibers provides isotropic mechanical properties, which are beneficial in applications requiring uniform strength from all directions.
- Cost-Effective: Compared to woven fabrics, CSM tends to be less expensive and can be more cost-effective in producing large-scale or thick-laminated objects.
Handling Techniques:
- Cutting and Laying: Use sharp scissors or a knife to cut the mat to the required size. Lay the mat into the mold carefully, ensuring it conforms to the shape without any air pockets or overlaps.
- Resin Application: Apply resin uniformly using a brush or roller. Ensure thorough saturation for optimal bond strength and integrity of the composite.
- Curing and Finishing: Allow the resin to cure completely according to manufacturer guidelines before removing the composite from the mold. Finish with sanding or painting as required for the final application.
Fiberglass Sheets: Advanced Material Solutions
What are Fiberglass Sheets?
Fiberglass Sheets, particularly those known as G10 and FR4, are high-pressure laminates composed of a fiberglass cloth impregnated with an epoxy resin binder. These sheets are engineered to provide superior strength and durability while maintaining light weight and resistance to corrosion. G10 refers to the type of fiberglass sheet that is not fire retardant, whereas FR4 includes a fire-retardant additive, making it suitable for electronic applications where fire resistance is crucial. These materials are renowned for their exceptional electrical insulation properties, dimensional stability, and uniformity, making them ideal for a wide range of demanding applications.
Manufacturing Process and Features
The manufacturing process of Fiberglass Sheets involves multiple steps:
- Preparation of Prepreg Material: The fiberglass cloth is first impregnated with an epoxy resin mixture, creating what is known as prepreg.
- Lay-Up and Stacking: The prepreg layers are stacked to the desired thickness in alignment or at varying angles to achieve specific strength characteristics.
- Curing in an Autoclave: The stacked layers are then placed in an autoclave, where they are subjected to controlled heat and pressure. This process cures the epoxy, turning the prepreg into a rigid, solid sheet that is integrally bonded.
Features of Fiberglass Sheets include:
- High Mechanical Strength: Provides robustness needed for structural components in demanding applications.
- Excellent Electrical Insulation: Essential for electronic and electrical applications, preventing electrical arcing and insulation failures.
- Superior Chemical Resistance: Enables use in chemically harsh environments without degrading.
- Thermal Stability: Maintains its integrity and performance over a wide range of temperatures.
Read More From Techbullion
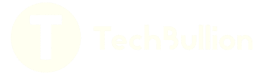