As U.S. manufacturers and mobility providers grapple with fragmented digital ecosystems, protracted development cycles, and mounting safety and efficiency demands, the need for a visionary who can translate advanced technologies into practical solutions has never been greater. Ankush Keskar rises to this challenge, leveraging 23 years of cross-industry expertise to help organizations design safer, smarter, and more efficient products by weaving AI, IoT, 5G, EDGE-Cloud computing and digital-twin methodologies into their workflows.
A Unified Vision for Convergence-Driven Innovation
At the heart of Ankush’s philosophy lies a single, unifying principle: convergence. By blending advanced capabilities— ranging from Internet of Things sensor fusion, AI-powered analytics, and Machine Learning models to private 5G/CBRS networks and Geographical Information Systems —he empowers organizations to transcend traditional boundaries. This approach transforms isolated data streams into rich, actionable insights, fueling smarter product features, automated decision-making, and end-to-end supply-chain visibility. Whether companies manufacture vehicles, process food, consumer packages, or precision industrial machinery, this convergence model lays the groundwork for accelerated development, improved quality, and rapid time-to-market.
From Early Simulation Tools to Today’s Digital Twins
Keskar’s journey began with a fascination for how individual components coalesce into complex systems. His initial work involved designing simulation platforms that rendered power-electronics and motor-control interactions in vivid detail—offering engineers an unprecedented window into subsystem behaviors. At that time, limited computational capacity constrained large-scale data gathering.
Fast forward to today: by leveraging IoT-enabled data acquisition, machine-learning algorithms, and dedicated 5G/CBRS backbones, Keskar has elevated those early simulations into full-scale Digital Twins as a design input into Layered and for Advanced Manufacturing and. These virtual replicas now predict system performance across every phase—design, prototyping, production, and even maintenance—enabling organizations to anticipate issues, optimize parameters, and slash costly downtime.
A Blueprint for Smart Factory Transformation
Keskar has been instrumental in guiding U.S. manufacturers toward Industry 4.0, which, according to McKinsey, is expected to create value for suppliers and manufacturers of greater than $3 trillion worldwide. He begins by evaluating each plant’s existing processes and physical assets through the lens of the ISA-95 model, identifying integration points where IT and operational technology (OT) can merge. From there, he blueprints factory specific private 5G/CBRS network that securly carry high-volume IoT data, deploys AI/ML-driven quality-control systems to detect anomalies in real time, and embeds cloud and edge computing for scalable analytics.
He also integrates GIS-based planning tools to optimize facility layouts and logistics. This comprehensive architecture gives companies in sectors as varied as paper packaging, food and beverage, specialty chemicals, and agricultural equipment the agility to respond to fluctuating demand, minimize waste, and keep lines running without interruption.
Tangible Benefits: Efficiency, Quality, and Cost Savings
Keskar’s smart-factory interventions yield measurable returns. Through his approach of foundationally looking at factory architecture and by applying predictive-maintenance algorithms, equipment downtime shrinks by about 20 percent. AI-guided quality checks reduce raw-material waste by close to 10 percent. Production flexibility and optimized scheduling can deliver up to a 30 percent lift in output.
Maintenance turnaround times improve by roughly 15 percent. For a mid-sized plant, these gains translate into annual savings of around $250,000; when extended across an entire product lifecycle, cumulative benefits can reach $25 million to $50 million. And as multi-site enterprises adopt standardized processes, networked supply chains, and economies of scale, aggregate savings have the potential to soar to $100 million–$400 million—fueling enduring competitiveness for U.S. manufacturers on the global stage.
Thought Leadership: Sharing Frameworks and Best Practices
A firm believer in community-driven progress, Keskar actively disseminates his insights through peer-reviewed journals and industry conferences. His widely cited papers include “Advancing Industrial IoT and Industry 4.0 through Digital Twin Technologies,” which outlines a step-by-step guide to implementing virtual system replicas for intelligent manufacturing; “Enhancing Manufacturing Operational Excellence through Cloudification,” presenting strategies to boost agility and scalability; and “Driving Operational Excellence in Manufacturing through Generative AI,” detailing how AI can generate new process optimizations and design innovations.
Shaping a Smarter, Safer, and More Connected Future
As the United States accelerates its digital transformation, Ankush Keskar’s work offers a proven roadmap: start with a holistic systems perspective, converge disparate technologies into cohesive platforms, and rigorously validate every innovation against real-world criteria. From architecting end-to-end smart-factory ecosystems, his contributions demonstrate that ambitious digital goals can be matched with disciplined execution.
In an era defined by rapid change, Keskar’s vision remains clear: to harness innovation as means to build resilient and human-centered systems. As companies seek to navigate the complexities of tomorrow’s markets, his blueprint for convergence-driven transformation offers both inspiration and a practical path forward—ensuring that technology truly fulfills its promise of progress for US manufacturing and society at large.
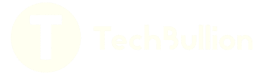