Planning an effective box build assembly is a critical stage in the assembling system of electronic gadgets. Functionality, dependability, manufacturability, and cost-effectiveness must all be taken into account during the design process. A comprehensive guide to the box build assembly design for manufacturing will be provided in this article.
Plan Considerations
Prior to beginning the plan cycle, taking into account the accompanying factors is fundamental:
Functionality: The electronic device’s functional requirements must be met by the design.
Reliability: The electronic device’s long-term dependability must be guaranteed by the design.
Manufacturability: Taking into account the available materials, processes, and equipment, the design must be machinable.
Cost-effectiveness: The plan should be practical, thinking about the materials, cycles, and hardware accessible.
PCB Design
A crucial step in the box build assembly design process is PCB design. The PCB fills in as the establishment for the electronic parts and sub-congregations.
During the PCB configuration process, taking into account the accompanying factors is fundamental:
Size of PCB: The size of the PCB should be viable with the fenced in area or box.
Number of PCB layers: The layer count of the PCB should be viable with the electronic parts and sub-congregations.
Spacing and width of the trace: The electronic sub-assemblies and components designed by reputed pcb assembly manufacturer must be compatible with the trace width and spacing.
Placement of components: For functionality, dependability, and manufactureability, the placement of the components must be optimized.
Design Of The Enclosure
Another important step in the process of designing the box build assembly is the design of the enclosure, or box. The nook or box fills in as the external shell of the electronic gadget, safeguarding the electronic parts and sub-congregations from outside components.
During the walled in area or box configuration process, taking into account the accompanying factors is fundamental:
Size of enclosure or box: The size of the walled in area or box should be viable with the PCB and other sub-gatherings.
Selection of materials: The material chosen needs to be able to work with the electronic sub-assemblies and components and protect them sufficiently from the outside world.
Chosen fasteners: The choice of fasteners must be strong enough and reliable enough to work with the material of the box or enclosure.
Sub-Assembly Design
A crucial step in the box build assembly design process is the sub-assembly design. Power supplies, displays, and sensors are examples of sub-assemblies that must be designed to be compatible with the PCB and box.
It is essential to take the following aspects into consideration when designing a sub-assembly:
Similarity with PCB and nook or box: The PCB and the enclosure or box must be compatible with the design of the sub-assembly.
Functionality: The electronic device’s functional requirements must be met by the sub-assembly.
Reliability: The electronic device’s long-term dependability must be guaranteed by the sub-assembly.
Manufacturability: Taking into account the available materials, processes, and equipment, the sub-assembly design must be machinable.
Cost-effectiveness: Taking into account the available materials, processes, and equipment, the sub-assembly design must be cost-effective.
Design For Assembly
A crucial step in the box build assembly design process is Design for Assembly (DFA). The process of making products that are simple to assemble is known as DFA. DFA’s objective is to improve product quality and dependability while simultaneously reducing assembly time and costs.
It is essential to take into consideration the following aspects during the DFA procedure:
Part direction: For ease of assembly, the orientation of the components needs to be optimized.
Clasp determination: The latch determination should be viable with the get together interaction and give satisfactory strength and unwavering quality.
Choosing a connector: The choice of connector must be appropriate in terms of strength and dependability and compatible with the assembly procedure.
Design For Testing
Design for testing (DFT) is an essential step in the process of designing a box build assembly. DFT is the method involved with planning items to be not difficult to test. The objective of DFT is to decrease testing time and cost while further developing item quality and dependability.
It is essential to take into consideration the following aspects during the DFT procedure:
Test focuses: To make testing easier, the test points need to be optimized.
Exam coverage: To ensure that all electronic components and sub-assemblies are adequately tested, the test coverage needs to be optimized.
Test gear similarity: The test hardware should be viable with the test focuses and give exact and solid experimental outcomes.
Design Review
Design review is a basic move toward the box build assembly plan process. The process of looking over a design to see if it meets the requirements for functionality, dependability, manufacturability, and cost-effectiveness is known as design review.
During the plan audit process, taking into account the accompanying factors is fundamental:
Requirements for use: The electronic device’s functional requirements must be met by the design.
Requirements for dependability: The electronic device’s long-term dependability must be guaranteed by the design.
Needs for manufacturability: Taking into account the available materials, processes, and equipment, the design must be machinable.
Needs for cost-effectiveness: Taking into account the available materials, processes, and equipment, the design must be cost-effective.
Design Documentation
Design documentation is an essential step in the process of designing a box build assembly. The process of documenting the design, which includes the PCB design, enclosure or box design, sub-assembly design, DFA, DFT, and design review, is known as design documentation.
During the plan documentation process, taking into account the accompanying factors is fundamental:
Accuracy: The design must be accurately represented in the design documentation.
Completeness: All aspects of the design must be included in the complete design documentation.
Clarity: The documentation for the design needs to be easy to read and understand.
Conclusion
The design of a box build assembly is a complicated process that takes into account cost-effectiveness, reliability, manufacturability, and functionality. By keeping the rules framed in this article, you can guarantee that your box build assembly is intended for assembling, diminishing get together time and cost while further developing item quality and dependability.
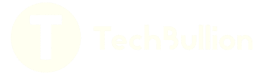