Manufacturers today face growing pressure to improve output, maintain precision, and reduce operational costs, all without sacrificing quality. In response, many fabrication businesses are rethinking how their production lines are designed. Instead of relying on isolated, single-function machines, more operations are turning to integrated systems that offer flexibility, scalability, and performance. This is where modular equipment, such as Fom Machinery, comes into play.
With its emphasis on automation, consistency, and adaptability, modular fabrication equipment helps streamline complex workflows. It allows manufacturers to link various stages of production, cutting, milling, drilling, welding, and assembly, into a seamless process. This reduces handling time, improves throughput, and supports lean manufacturing goals.
The Benefits of a Modular Approach
One of the greatest advantages of modular equipment is its ability to grow with a business. Unlike traditional setups that require costly overhauls as demand increases, modular systems can be expanded incrementally. New modules can be added or existing ones upgraded to support higher volumes or more advanced processes, without disrupting the core workflow.
This flexibility is especially valuable in industries where production needs fluctuate or where bespoke projects demand different configurations. A modular setup means businesses are no longer limited by rigid layouts or equipment that only serves a single purpose. It enables faster changeovers and allows production teams to respond more easily to market shifts.
Reducing Human Error and Improving Consistency
Automation is often central to modular machinery. By reducing manual input, manufacturers can eliminate variability and ensure each product is fabricated to exact specifications. This is especially important in aluminium and uPVC fabrication, where precision is vital and tolerance for error is low.
Consistent output improves customer satisfaction and reduces the cost of rework. It also frees up skilled workers to focus on value-added tasks like quality assurance or custom assembly, rather than repetitive manual operations. In this way, modular automation doesn’t just improve production, it also supports better use of human resources.
Enhancing Safety and Ergonomics
Safety is a top concern in any fabrication environment. Modular equipment is typically designed with operator safety in mind, incorporating features such as automatic stops, guarded work zones, and intuitive controls. This helps minimise the risk of injury, particularly during repetitive or physically demanding tasks.
In addition to safety, these systems often support improved ergonomics. Workers are less likely to be exposed to vibration, repetitive strain, or heavy lifting when equipment is designed to handle material movement and processing. Over time, this can reduce fatigue and support a healthier, more efficient workforce.
Supporting Quality from First Cut to Final Finish
When every stage of production is connected, it becomes easier to maintain quality control across the entire process. Modular systems allow for real-time monitoring, digital calibration, and feedback loops that catch errors early and ensure consistent standards.
Whether you’re cutting profiles, drilling holes, or preparing surfaces for finishing, each module works in coordination with the next. This minimises variation, supports traceability, and makes it easier to comply with industry regulations. For manufacturers looking to scale their operations while maintaining a reputation for reliability, this integrated approach offers a strong foundation.
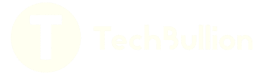