Welding is a fabrication process that joins materials, typically metals or thermoplastics, using high heat to melt the parts together. The process can involve the application of pressure or may be performed using filler material. Welding is essential in various industries, including construction, manufacturing, automotive, and aerospace. Understanding the different welding methods, equipment, and techniques is crucial for selecting the right welder for your needs.
Understanding Welding Processes
Gas Metal Arc Welding (GMAW)
Overview:
Gas Metal Arc Welding, commonly known as MIG Welder, utilizes a continuous wire electrode fed through a welding gun. A shielding gas protects the molten weld pool from contamination.
Advantages:
- Ease of Use: MIG welding is relatively easy to learn, making it suitable for beginners.
- Speed: Faster welding process due to the continuous wire feed.
- Minimal Cleanup: Produces clean welds with less spatter compared to other methods.
Disadvantages:
- Gas Dependency: Requires shielding gas, which can be problematic in outdoor environments.
- Equipment Cost: Initial setup costs can be higher due to the need for gas cylinders and regulators.
- Material Preparation: Requires clean surfaces for optimal results.
Gas Tungsten Arc Welding (GTAW)
Overview:
Gas Tungsten Arc Welding, or TIG Welder, is a precise and versatile welding process using a non-consumable tungsten electrode. This method allows for high-quality welds, especially on thin materials.
Advantages:
- Quality: Produces high-quality, clean welds with minimal contamination.
- Versatility: Can weld various metals, including aluminum, stainless steel, and exotic materials.
- Control: Offers precise control over the welding process.
Disadvantages:
- Skill Level: This requires a higher skill than MIG and stick welding.
- Speed: Slower welding speed, making it less suitable for large projects.
- Equipment Cost: Typically more expensive due to specialized equipment.
Shielded Metal Arc Welding (SMAW)
Overview:
Shielded Metal Arc Welding, commonly called Stick Welder, is one of the oldest and most versatile welding processes. It involves using a coated electrode that produces an electric arc between the electrode and the workpiece. This process melts the electrode and the base metal, allowing them to fuse.
Advantages:
- Versatility: Can be used on various metals and in different positions.
- Cost-Effective: Equipment is generally less expensive compared to other welding processes.
- Portability: Stick welders are often lightweight and easy to transport.
- Outdoor Use: Effective in windy conditions since the flux coating provides a protective shield.
Disadvantages:
- Skill Requirement: Requires more practice to master compared to MIG welding.
- Post-Weld Cleanup: Leaves slag that needs to be chipped away after welding.
- Limited to Thicker Metals: It could be better for thin materials, as they can quickly burn through.
Flux-Cored Arc Welding (FCAW)
Overview:
Flux-cored arc Welding is similar to MIG welding but uses a tubular wire filled with flux. This process can be performed with or without shielding gas, making it versatile for applications.
Advantages:
- Outdoor Use: Effective in windy conditions without requiring external shielding gas.
- High Deposition Rate: Can weld thicker materials more quickly than MIG welding.
- Flexibility: Suitable for various welding positions and environments.
Disadvantages:
- Slag Production: Leaves slag that requires post-weld cleanup.
- Spatter: Generally produces more spatter compared to other processes.
- Welding Quality: It may achieve a different quality than TIG welding.
Submerged Arc Welding (SAW)
Overview:
Submerged Arc Welding is an automatic or semi-automatic process that uses a continuously fed bare wire electrode and a granular flux. The arc is submerged under the flux, providing excellent protection against contamination.
Advantages:
- High Productivity: Ideal for large-scale welding operations due to its high deposition rate.
- Quality: Produces high-quality, consistent welds.
- Minimal Cleanup: The flux protects the weld from oxidation, reducing the need for post-weld cleaning.
Disadvantages:
- Limited Applications: Mostly used for flat or horizontal welding.
- Equipment Cost: More extensive and expensive equipment is required than other methods.
- Less Portable: Not suitable for field applications due to equipment size.
Choosing the Right Welder
Factors to Consider
When choosing a welder, several factors must be taken into account to ensure that the selected equipment meets your specific needs:
Material Type
The type of material you will be welding is crucial in determining the appropriate welding method. Different processes excel with various materials:
- Mild Steel: MIG and Stick welding are ideal.
- Stainless Steel: TIG and MIG welding are preferred for quality welds.
- Aluminum: TIG welding is often the best choice for precision work.
Material Thickness
The thickness of the materials you plan to weld will influence your decision:
- Thin Materials: MIG and TIG welding are suitable for thin metals.
- Thick Materials: Stick and Flux-Cored welding work best for thicker sections.
Welding Environment
The environment in which you will be welding is a significant factor:
- Indoor Use: MIG and TIG welding are excellent for clean, controlled environments.
- Outdoor Use: Stick and Flux-Cored welding are better for windy or dirty conditions.
Skill Level
Your welding experience will dictate which method you choose:
- Beginners: MIG welding is recommended for its ease of use.
- Advanced Users: TIG welding requires more precision and quality but more skill.
Power Requirements
Different welders require various power sources:
- 110V Welders: Suitable for home use and light projects.
- 220V Welders: Necessary for heavy-duty applications and thicker materials.
Duty Cycle
The duty cycle indicates how long a welder can operate before it needs to cool down. A higher-duty cycle is essential for continuous or heavy work.
Portability
Consider its weight and size if you need to move your welder frequently. Some models are designed for portability, making them ideal for fieldwork.
Welder Types Explained
Stick Welders
Stick welders are perfect for heavy-duty work and outdoor applications. They can be used on dirty or rusty materials, making them versatile. While they require more skill, the low cost and portability make them popular among DIY enthusiasts.
MIG Welders
MIG welders are the go-to choice for beginners due to their ease of use and speed. They offer a clean and efficient welding process, ideal for various applications. The requirement for shielding gas may limit their use outdoors, but their versatility makes them a favorite among hobbyists and professionals.
TIG Welders
TIG welders excel in producing high-quality, precise welds. They are commonly used in applications where aesthetics and strength are crucial. While they require a more advanced skill level, they are invaluable for welding thin materials and intricate designs.
Flux-Cored Welders
Flux-cored welders are ideal for outdoor use and projects that require high deposition rates. They are effective for welding thicker materials and are a solid choice for construction and heavy repair work.
Multi-Process Welders
Multi-process welders offer the flexibility to switch between different welding methods. They are ideal for users who work on various projects and need the ability to adapt quickly.
Essential Welding Equipment
To get started with welding, you will need several key pieces of equipment beyond the welder itself:
Personal Protective Equipment (PPE)
Safety is paramount in welding. Essential PPE includes:
- Welding Helmet: Protects your eyes and face from UV rays and sparks.
- Gloves: Provides hand protection and enhances grip.
- Protective Clothing: Flame-resistant jackets, aprons, and pants help protect against burns.
- Safety Boots: Steel-toed boots prevent foot injuries.
Filler Material
Depending on the welding method and material, you will need the appropriate filler material:
- Electrodes: Used in Stick welding; available in various types for different applications.
- Filler Rods: These are used in TIG welding to provide additional material for the weld pool.
- MIG Wire: Continuous wire used in MIG welding.
Welding Accessories
Several accessories can enhance your welding experience:
- Clamps: Keep your workpieces secure during welding.
- Chipping Hammer: Removes slag from stick welds.
- Wire Brush: Cleans welds for better adhesion.
- Carts: Facilitate easy movement of equipment and supplies.
Gas Supply
For MIG and TIG welding, a gas supply is necessary:
- Argon: Commonly used for TIG welding of non-ferrous metals.
- CO2: Often used for MIG welding, particularly with flux-cored wire.
- Mixed Gasses: A combination of argon and CO2 provides better results for MIG welding on steel.
Maintenance and Care for Welders
To ensure longevity and optimal performance, proper maintenance of your welder is essential:
Regular Cleaning
Keep your welder clean by removing dust, debris, and spatter. Regularly inspect and clean the nozzle and contact tip for optimal gas flow and arc stability.
Inspect Cables and Connections
Check power cables, ground clamps, and hoses for wear or damage. Replace any frayed or damaged components to prevent electrical hazards.
Store Properly
Store your welder in a dry, cool place when not in use. Protect it from moisture and extreme temperatures to prevent rust and deterioration.
Follow Manufacturer Guidelines
Refer to the manufacturer’s instructions for specific maintenance tasks and schedules. Regular servicing can help catch potential issues before they become significant problems.
Welding Safety Tips
Safety is paramount in welding. Here are essential tips to ensure a safe welding environment:
Wear Proper PPE
Always wear appropriate protective gear, including a welding helmet, gloves, and protective clothing. Ensure that all equipment fits properly and is in good condition.
Ensure Proper Ventilation
Welding produces harmful fumes and glasses. Work in a well-ventilated area and consider using exhaust fans or fume extractors when necessary.
Check Equipment Regularly
Inspect your welding equipment before use. Check for leaks in gas lines, frayed cables, and proper functionality of all components.
Be Aware of Your Surroundings
Clear the work area of flammable materials and ensure that no one is in the immediate vicinity when welding. Use fire-resistant curtains or screens to protect others from sparks and UV radiation.
Keep Fire Extinguishers Nearby
Always have a suitable fire extinguisher readily available in case of an emergency. Ensure that you and your coworkers know how to use it effectively.
Welding Projects for Beginners
Starting with manageable projects can help you build confidence and skills. Here are a few project ideas for beginners:
Welding a Simple Metal Frame
Create a basic frame using square tubing or angle iron. This project will help you practice your cuts and joints while learning to control the welder.
Fabricating a Tool Holder
Design and build a tool holder for your workshop. This project allows you to practice various welding techniques and improve your organizational skills.
Repairing a Metal Fence
Use your welding skills to repair a broken or damaged metal fence. This practical project will help you gain experience with real-world applications.
Building a Fire Pit
Construct a simple fire pit using steel sheets or old metal drums. This project lets you practice your welding skills while creating something functional for your backyard.
Creating Art from Scrap Metal
Use scrap metal to create sculptures or decorative pieces. This project encourages creativity while allowing you to experiment with different welding techniques.
Advanced Welding Techniques
As you become more experienced, you may explore advanced welding techniques. These techniques can enhance your skills and broaden your project capabilities:
Pulsed TIG Welding
Pulsed TIG welding involves adjusting the current to create a pulsing effect, allowing for better control over heat input. This technique is beneficial for thin materials and can reduce distortion.
TIG Welding with Filler Material
Mastering the adding filler material while TIG welding allows for more robust and more controlled welds, especially in critical applications.
Vertical and Overhead Welding
Practicing vertical and overhead welding can significantly improve your skill set. These positions require more control and technique, making them valuable for advanced welders.
Welding Aluminum and Exotic Materials
Learning to weld aluminum and other non-ferrous metals requires specialized techniques and equipment. Understanding the unique properties of these materials can expand your project possibilities.
Fabrication Techniques
Developing fabrication techniques, such as cutting, bending, and shaping metal, can enhance your overall welding capabilities. This knowledge allows for the creation of complex assemblies.
Conclusion
Choosing the right welder is crucial for achieving successful welding projects. Understanding the different welding processes, equipment, and techniques will help you make an informed decision based on your specific needs. Whether you’re a beginner or an advanced user, this comprehensive guide is valuable for selecting the best welder and enhancing your welding skills. Prioritize safety, practice regularly, and embrace the art of welding to create solid and lasting bonds in your projects.
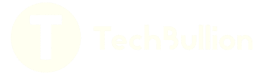