No doubt, cost estimation is an integral part of any construction project. Submitting a wrong estimate is like a nightmare for the owner or contractor of the project. It has to do a lot with the project’s planning, budgeting, and of course, its successful progression. Accurate cost evaluations set contractors free in making informed decisions and creating realistic timelines. Similarly, it helps in avoiding project delays, cost overruns, and team disputes. Creating an accurate construction budget can serve as a profit booster for a company. With a focus on construction estimation accuracy, this article will tell you ways to have considerable improvements in your estimating processes.
Key Pointers for Enhancing the Accuracy in Construction Estimation
1. Build up a Systematic Approach
Building a systematic approach to construction cost estimation is significant for ensuring accuracy. It involves the establishment of standard measures and guiding principles for each phase of the estimation process. The main chunks of this process comprise material takeoff, material pricing, and labor costs. Moreover, creating a standardized procedure reduces all the possible errors that are endangering the success of the company and ensures consistency throughout the project’s lifecycle. Thus, following such an approach result in more accurate cost estimates.
2. A Detailed Assessment of the Project Plans
Assessing the project plans from point to point is imperative to ensure complete accuracy in the process. This evaluation is useful for considering the entire cost elements of the project, particularly the material cost requirements for it. It engages with a careful examination of the project plans incorporating the architectural, structural, and mechanical drawings. Envisioning the whole plan in detail takes time but is of great assistance to the company from several ends. A thorough understanding can help in identifying potential issues or challenges that may impact the project’s cost estimates.
3. Utilization of Advance Technology
Undeniably, Technological breakthrough has drastically revolutionized the world and more specifically the construction industry. Its footprints are playing a vital role in improving construction estimation accuracy. Using digital tools like Building Information Modeling (BIM) software can help automate the takeoff process which reduces the chance of error occurrence and makes the accuracy rate of the estimates better. BIM software can also help in identifying potential design issues or contradictions before the start of any construction phase. This allows for making necessary adjustments to the plans for the purpose of circumventing delays or cost overruns.
4. Maintain Up-to-date Records
Maintaining updated records of all material quantities and procedures used in previous projects is significant to venture out successfully. The information present is used for trends or pattern identification in relevance to the material usage and resource allocation. This structure brings about ultimate accuracy in carrying out future projects. It also helps contractors keep track record of the material purchases at a certain cost in a specific location, which can be useful when negotiating prices with suppliers.
5. Application of Historical Data
Historical data is a useful source in providing valuable insights into past projects. It may include material used in a particular type of project, its labor requirements, and challenging concerns associated with it that may impact future projects. However, it is proved by analyzing the result of multiple projects that referring and applying the historical data for construction estimates in the current projects helps improve the accuracy in entirety. Historical data is helpful to all the parties to the construction i.e., contractors, investors, owners or estimators, etc. for making informed decisions about future projects.
6. Collaboration and Coordination with Suppliers
Collaborating and coordinating with suppliers is vital for contractors if they need exactness in figures. It improves construction estimation accuracy by providing contractors with up-to-date pricing information and availability of materials. Building strong relationships with suppliers can empower the contractors for having better negotiations on prices and delivery schedules. Moreover, it has a great impact on the overall cost of a project. Suppliers are the chief part of the market where innovative materials are introduced on daily basis. They can provide valuable insights into new materials or technologies that may help in proliferating future projects.
7. Contingent Plan for the Project
It is a common saying, construction projects are inherently unpredictable. Consequently, unexpected situations can affect the cost of a project. To cope with this, contractors should factor in contingencies when corresponding with the construction estimator. A contingent plan in place can cover all the gaps derived from unforeseen happenings during the construction work progress.
Role of Material Takeoff in the Estimation
Material takeoff or Quantity takeoff is the process of calculating the quantities of materials needed for a construction project. It comprises concrete, steel, lumber, wood, iron, and other building materials. Identifying the correct quantities for the construction project is the foundation of maintaining balanced estimation with utter accuracy. It involves reviewing the project plans and setting the quantities of each material needed. However, takeoffs are a fundamental step in the construction estimation process, as they develop the base for precisely measured material cost estimates.
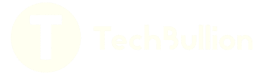