From rubber handles on toothbrushes to insulating covers on electrical components, overmolding is how many of the most common plastic products are manufactured today.
A type of injection molding whereby one material is overlaid onto a substrate, overmolding carries many benefits with it, but there are plenty of design factors to be considered.
Material compatibility, chemical composition, application, and mold design are all important variables in the overmolding process, so be sure to consult an expert as you prepare your injection molding design.
What Is Overmolding?
When a product is made by the injection molding process, a molten material such as plastic or metal is forcibly injected into a cavity, or mold. Once the material sets, it is ejected from the mold, creating a foundational layer called a substrate.
In standard injection molding processes, the substrate is the final (albeit unfinished) product. However, overmolding takes the process one step further by injecting a second molten material on top of the substrate to create an additional layer.
This allows the product to have a core component made from one material, and an outer layer made from another. However, some overmolded composites are made from the same material, but have different external properties, like varying colors.
If a product consists of a multilayer composite material that can be separated into constituent layers, there is a good chance overmolding was involved in its manufacture. That’s quite a few products, but a few examples of industries that rely on overmolding and the goods they produce are:
- Household products: Toothbrushes, cosmetics, insulated cups
- Automotive: Electrical sensors, gears, belts
- Medical devices: Probes, sensors, medical grade tubing
- Electronics: Phone covers, controllers, electrical wiring
- Labeling: Buttons, signs, gauges
These applications alone cause overmolding to be one of the most versatile forms of injection molding — and many other applications exist.
By adding an outer layer to a substrate, overmolding builds upon the principles of standard injection molding.
Benefits of Overmolding
One of the reasons that overmolding is so popular is that it greatly increases the value of the finished product. This form of injection molding is highly efficient, and is especially useful when the exterior surface of a product needs to possess different material properties than its core. Some examples are:
- Comfort. Products that are held must be able to be gripped and handled comfortably by their users. Overmolding enables products to have the sturdy core created from harder materials while still being soft and smooth enough to accommodate the customer.
- Electrical conductivity. Electronics must often have a metallic core as they make contact with circuit components underneath, but must be insulated to protect them from their environment. If a product must have varying insulative or conductive properties, overmolding may be a good way to achieve this effect.
- Vibration/impact dampening. Vibrating devices can cause discomfort to users that hold them, and objects that are dropped can be destroyed upon impact if left exposed. By overmolding an impact-resistant layer on top of the core component, both product and user can be protected from collisions and vibrations.
- Chemical stability. Some products can deteriorate when left exposed to the elements, and others must regularly operate under extreme conditions. Corrosion-resistant and insulative overmolds can protect valuable substrates, greatly prolonging their lifespan.
- Color. Many brands convey their image by using specific color schemes on all of their products. Overmolded layers can be colored according to the customer’s preference, enabling them to articulate their brand without compromising their substrate.
Another benefit of overmolding is that it simplifies the manufacturing process relative to other techniques. For example, a multilayer product created without overmolding might require two different substrates to be fabricated, and fused together afterward to form the final composite.
Such a process would require multiple added manufacturing steps, with all the extra equipment and labor attached. Unless such an elaborate manufacturing process was a necessity, overmolding is a vastly more efficient method.
Material Selection During the Overmolding Process
As beneficial as overmolding is, it must still be carried out with a great deal of caution. Mold creation, injection mechanism, and flow rate are just a few parameters to be considered during the overmolding design process, but perhaps the most important one is that of material selection — both for the substrate and the added layer.
Not only must each layer possess the desired material properties, but chemical and thermal compatibility is a must if the added layer is to adhere properly.
Nearly all metal-to-plastic surface interfaces are compatible with one another, but plastic-to-plastic, plastic-to-silicone, and plastic-to-rubber overmolds may perform differently. Plastic-to-plastic interfaces offer many benefits in aesthetics and functionality, but are more susceptible to incompatibilities and subsequent failure to perform as designed.
The best way to ensure that an overmolding product comes together as planned is to consult an injection molding expert, but familiarity with the wide variety of plastic resins available for use is highly beneficial. Here are a few of the most common plastics used in the overmolding process, along with some of their strengths:
- High Density Polyethylene (HDPE): Relatively high strength-to-weight ratio, good impact/weather resistance, highly malleable; often used in corrosion-resistant piping.
- Acrylonitrile Butadiene Styrene (ABS): Low electrical conductivity, low melting point, glossy surface finish, highly recyclable, cost-effective, easily colorable, highly moldable; often used in electronics.
- Polymethyl Methacrylate Acrylic (PMMA): High light transmissibility (up to 95%), UV/weather resistant, greatest surface hardness of any plastic, colorable with added dyes; often used in lighting applications.
There are many other plastics that can be considered, all of which have unique thermal, chemical and material properties.
Those designing an overmolding process should consider the substrate’s required material properties, and after deciding what properties the outer layer should possess, they should choose a material that is compatible both with their specifications and the substrate.
Overmolding Lends to Quality Product Manufacturing
Efficient, economical, and effective, overmolding is an excellent way to manufacture a multilayer product, but it’s not without its complexities. While providing the material properties needed for the job, many factors such as surface chemistry and thermal compatibility must be considered.
Other manufacturing concerns like mold fabrication and extraction methods exist, so it is best to consult an experienced injection molding expert like Fictiv to make a product come together.
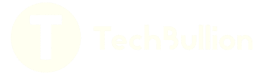