In this day and age, testing out the impact certain environments have on products we use in our daily lives has become a need. This helps identify how exactly certain conditions impact a product as well as how to better its efficiency and durability. In this article, we will look at salt spray testing and the workings, features as well as advantages of the salt spray corrosion testing chamber.
Salt Spray Chamber
The purpose of a salt spray chamber is to test the protective layer of electrical and electronic components, metal-based materials, and industrial goods. It assists in determining the corrosion resistance of coatings and materials of various items using a corrosive saline environment laboratory simulation.
An accelerated corrosive attack is performed in order to better predict how well the coating protects the metal during salt spray testing. Salt spray chambers are commonly used to test the corrosive qualities of organic or paint coatings, non-electrolytic coatings, zinc and zinc alloy plating, and electroplating.
Corrosion Testing
In salt spray testing, a corrosive attack on coated samples is used to verify whether the coating is suitable for use as a protective finish. The appearance of corrosive products, such as rust or other oxides, is evaluated after a defined amount of time to determine how effectively the product resists corrosion. Salt spray testing is the most used corrosion test method since it is quick, repeatable, and economical.
Features of Salt Spray Chamber
To conduct efficient and effective tests, LISUN salt spray chamber works in accordance with various international standards such as ISO9227, IEC60068-2-11 (GB/T2423.17), GB/T1771, and GB/T10125 amongst others.
To prevent salt spray overflow in the chamber, a waterproof structure is used between the chamber lid and the chamber body. Furthermore, to provide even salt spray dispersion and flexibly adjustable settlement, the chamber has a tower spraying system, a salt solution filtration system, and a non-crystal nozzle. Because the setting value cannot be lower than the current ambient temperature, the working room temperature range of the salt spray chamber is between 5°C and 50°C. Similarly, the temperature of the saturated barrel is between +40°C and +63°C, while the temperature of the brine is preheated by laboratory temperature. Additionally, the temperature uniformity is less than or equal to 2 degrees Celsius, while the temperature fluctuation is less than or equal to 1 degree Celsius. The Salt Spray testing time can be adjusted from 0 to 99,999 minutes.
The copper acceleration test, neutral test, custom test, acidic test, and programmable test are just a few of the spray methods available in the salt spray test chamber. In accordance with the industry requirements, each test can choose between continuous and intermittent spraying. Similarly, in the test setting interface, each test solution’s ratio has a corresponding explanation. The sample holder of the chamber is at a 15-30 degree angle to the vertical surface and it is advised that other irregular samples be kept inverted. The single weighing capacity of the V-groove is 3KG, while the single bearing capacity of the O-bar is 5KG. Placing samples under heavyweight is definitely prohibited.
Advantages of corrosion testing
The salt spray testing can be conducted on a variety of materials since it can be done on either bare or painted metal. In comparison to the time taken to test out products in the natural environment, corrosion testing lasts only a few minutes. A combined material and surface finish test is also available in the chamber which leads to easier testing. Furthermore, the test results are straightforward to grasp, and a diverse set of objects and parts can be tested.
LISUN’s salt spray test chamber also has the precision and flexibility needed to meet today’s stringent corrosion testing requirements. Here, the machine can produce salt spray, high humidity, and air drying within the chamber at a specific temperature. The corrosion cycle can be repeated automatically for a set number of times as well.
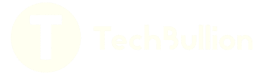